I worked several summer internships while in college, and as an employer I find them to be mutually beneficial. Companies are able to complete tasks they haven’t had time for, and students gain valuable work experience. I have been lucky to have two very good engineering interns this summer. In the spirit of having interns do my work for me, I thought it appropriate to have Robert write a blog post this week. Robert will be finishing up his degree in Architectural Engineering from Cal Poly San Luis Obispo this winter. Here is what Robert wrote about what it’s like to be an engineering intern:
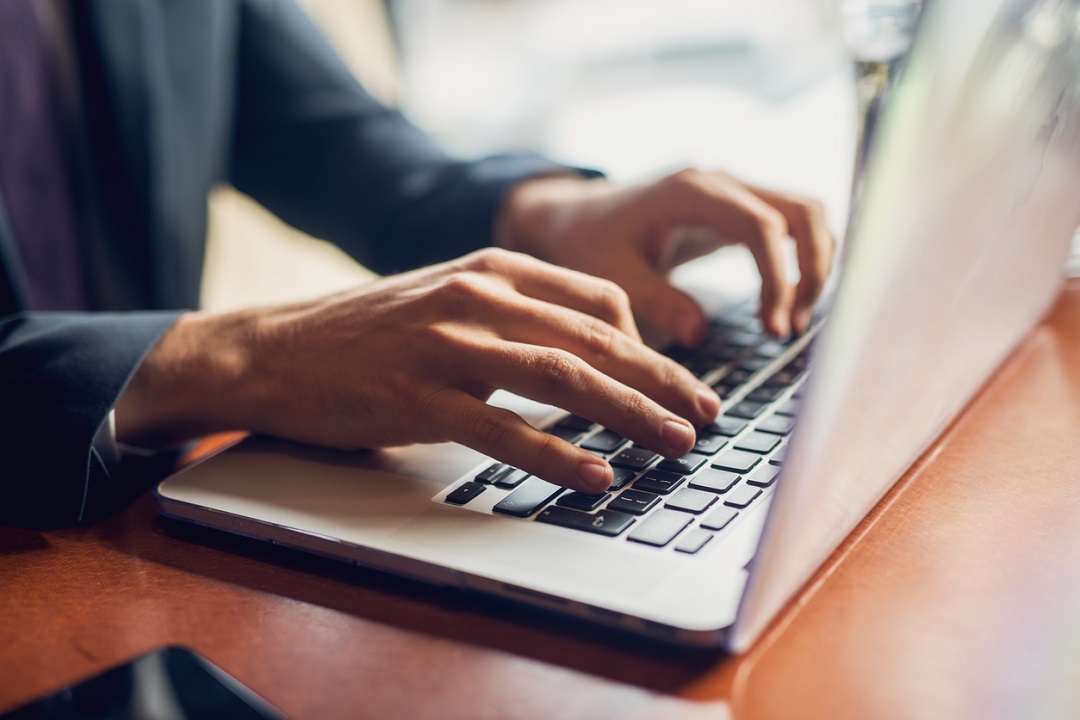
When Paul first asked me to write a blog post, I was a bit mystified for two reasons. First because of the fact that Paul even knew what a blog was, and second, it meant summing up everything I’ve done for the past few months into approximately 400 words. I guess the best way to go about this is to describe one of the projects that covers most of the other projects I’ve been working on in detail and finish by touching on some of the more unique ones.
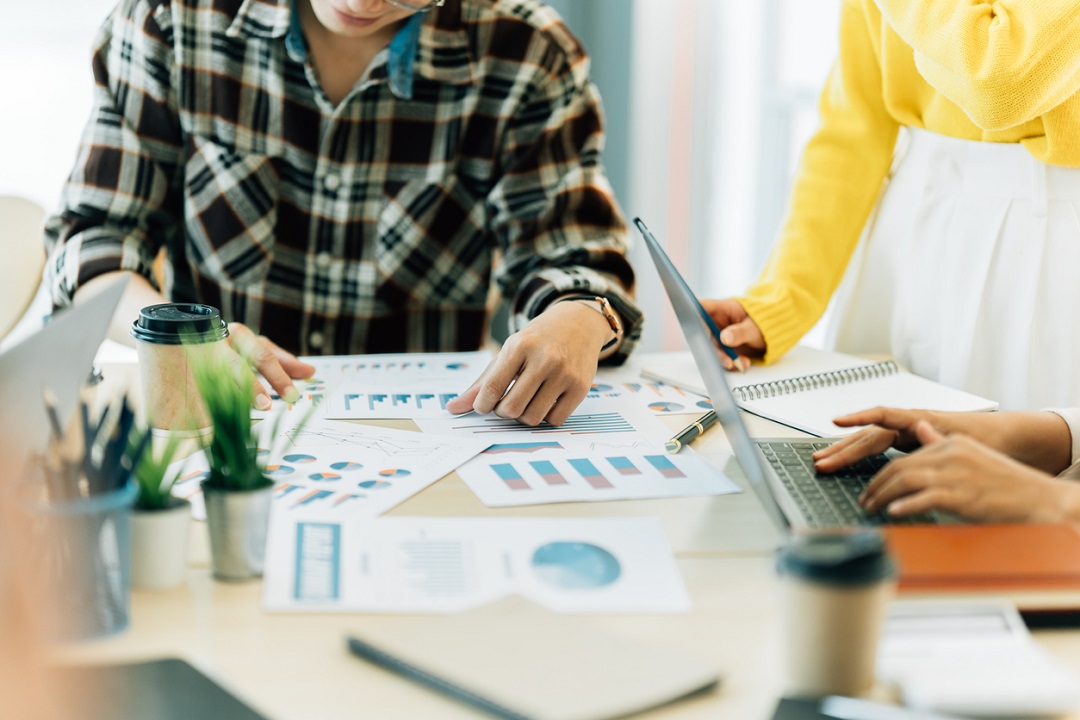
My initial project was a comparative analysis of the current holdown line with that of a competitor product line. This involved finding and categorizing all the different loading options for each holdown, either by looking up the values in the catalog or finding and deciphering the ICC-ES report. This project was particularly interesting because it exposed me to the world of code reports, which, other than the references in the Simpson Strong-Tie catalog, I had never seen before. Along with the code reports, I was able to explore the library of test data that is either digital or on paper. After running a few hundred bolt, screw, and nail calculations and comparing them to the test data, I was able to produce a rather larger spreadsheet that cross-listed everything I had researched.
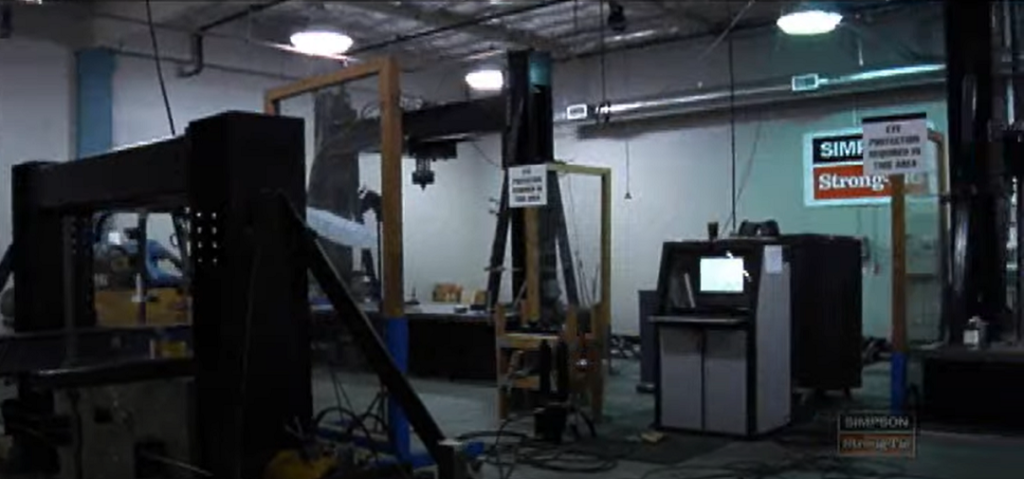
The result of the spreadsheet was to test one of the holdowns in a specially-designed steel fixture to determine the effect of boundary conditions on test results. For this I had to spend some time in the R&D lab to learn how exactly things were tested. Up until this point I had only seen the results of the testing; now I was able to actually see how different products were tested. After spending some time in the lab and witnessing some testing, I had a better idea of how to tackle the test fixture. Once I had designed the fixture (by that I mean after 10 or so revisions), it was sent to the Stockton, Calif. branch to get built.
With the fixture designed, my next process was to set up the test reports for all the testing that needed to get done. As this was my first time through this process, I had quite an interesting time figuring out how to work the database and have it save what I input. Doing the test write-ups probably took five times as long as necessary, but now when others ask me to do test write-ups, it takes me no time at all. Hopefully the fixture will get built in time for me to see the testing.
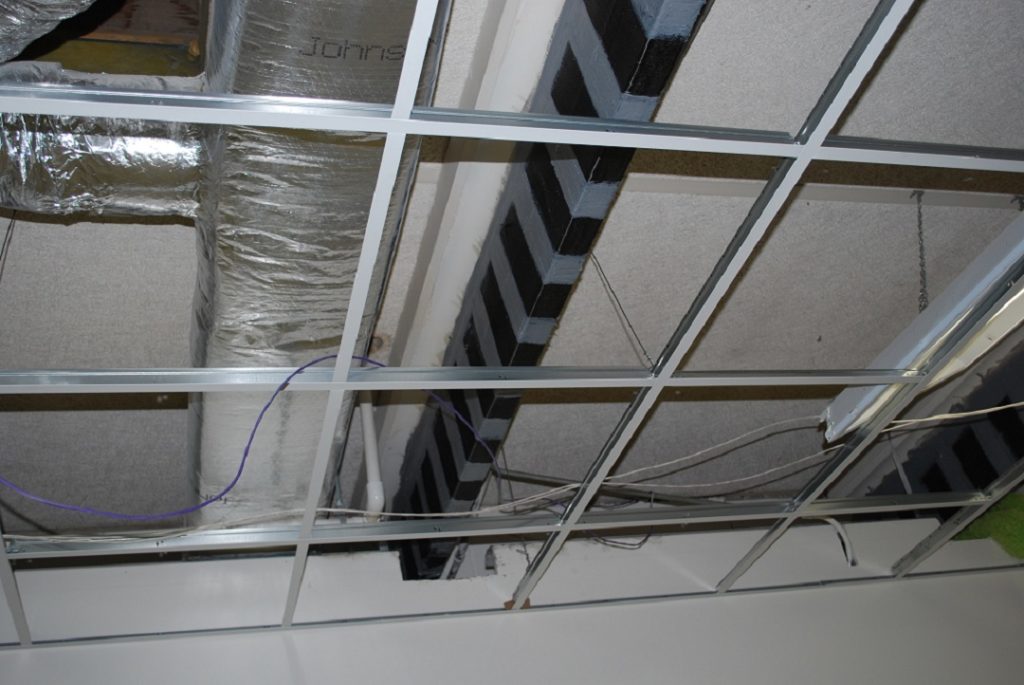
Along with doing more test write ups, I have had the grace of helping the Marketing Department with their Product Information Management (PIM) project, which by the reactions I get from most of the engineers over here, they are very glad I am the one working on it. I have also had the unique experience of digitizing the future and current maps of how products are designed, manufactured and sold. I’ve also been put on the front lines when it comes to testing our FRP (fiber reinforced polymer) products and cleaning rust from metal samples to determine their rust rate.
To sum up everything, it is nothing like I expected but definitely an experience I’ll remember.
– Robert
What are your thoughts? Visit the blog and leave a comment!
Did he get minimum wage That will prepare him for the real world
I hope you will enjoy being a Engineer.
I worry about our future
GOD LUCK——–Bring honor to our profession