This summer we welcomed engineering student Sam Lewis to intern at our Gallatin, Tennessee branch. He discusses his hands-on opportunity to test our fasteners, learn more about our company culture and people.
Greetings, Simpson Strong-Tie readers! My name is Sam Lewis, an Auburn mechanical engineering student who’s been investing the summer as an intern at your branch in Gallatin, Tennessee. I, like many engineers, love the process of taking things apart and learning how they function. I’ve grown up with Legos, erector sets, and the dream to fix up a project car from the ‘60s. As a mechanical engineer, I’ve studied physics, forces, and trajectories in depth, and I really never expected to see myself in a fastener manufacturing plant working with screws. However, after logging countless hours working with several of your great leaders, I found it’s really scratched my building itch.
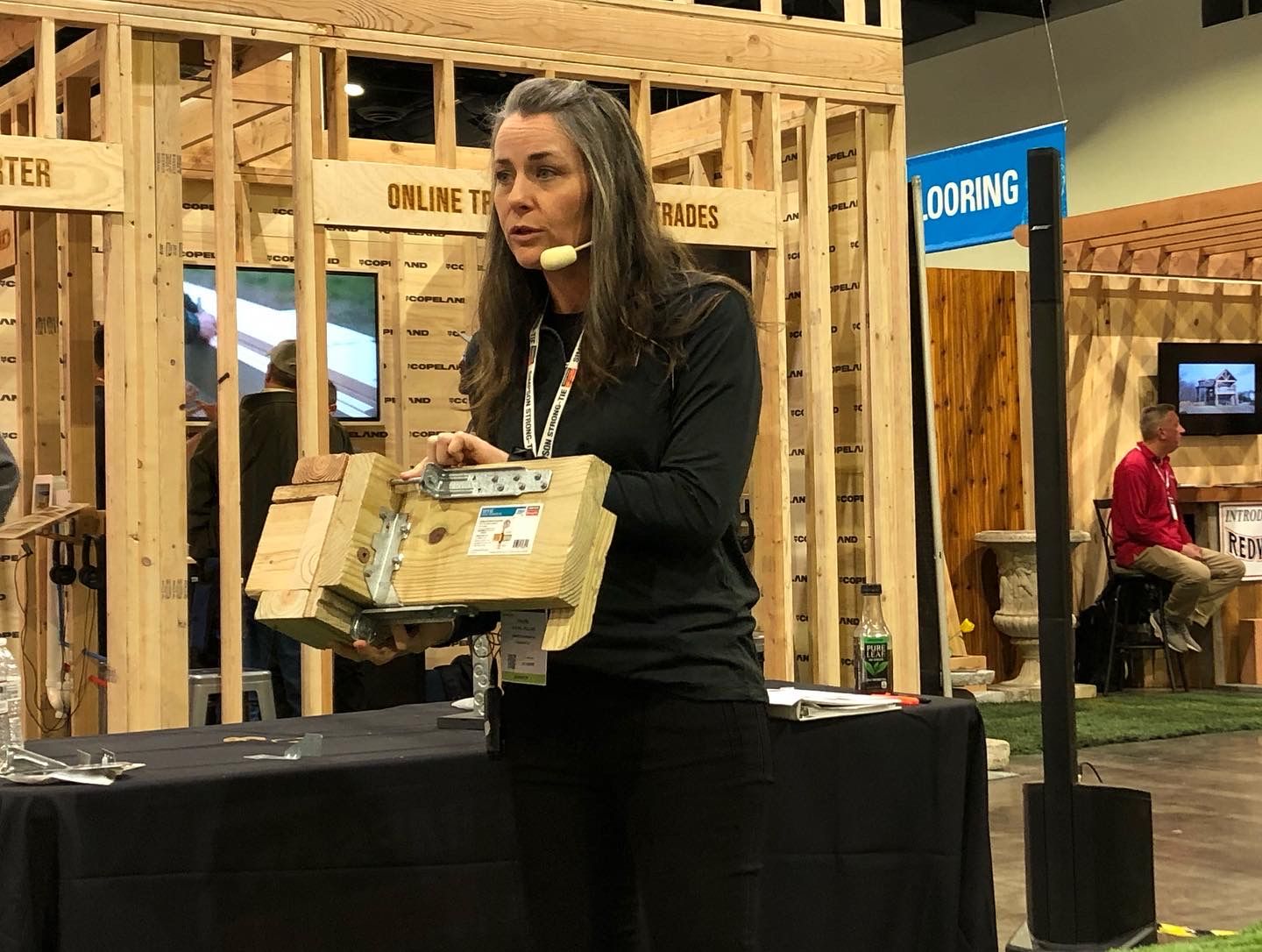
Finding Simpson Strong-Tie was a pretty funny story for me. If someone had asked me this past year who Simpson-Strong-Tie was or what they did, they would have been met with a blank stare. Little did I know I had been using their products for years with my dad building decks, framing houses, and completing rehabs. It wasn’t until by coincidence I overlapped with engineer Rachel Holland that I finally connected the product with the brand. After I finished my spring semester, my parents invited me to join them for a quick trip to San Diego, California, to visit my older sister. We hiked, thrifted, and explored several locations along that coast. Midpoint during our travels, we randomly met Rachel Holland and her family at the hotel pool and struck up a fabulous conversation and discovered she was an engineer. She described her position at Simpson as part of a community of “Engineers with personality.” I was sold. Weeks later, I found myself at a follow-up interview with Adam Tillinghast — a rock-climbing enthusiast engineer just like me! I now work with Collin Rountree, an engineer with a personality as big as his truck. FYI, he could probably tow your house down the street if it’s not anchored with Simpson’s Titen HD® heavy-duty screw anchors.
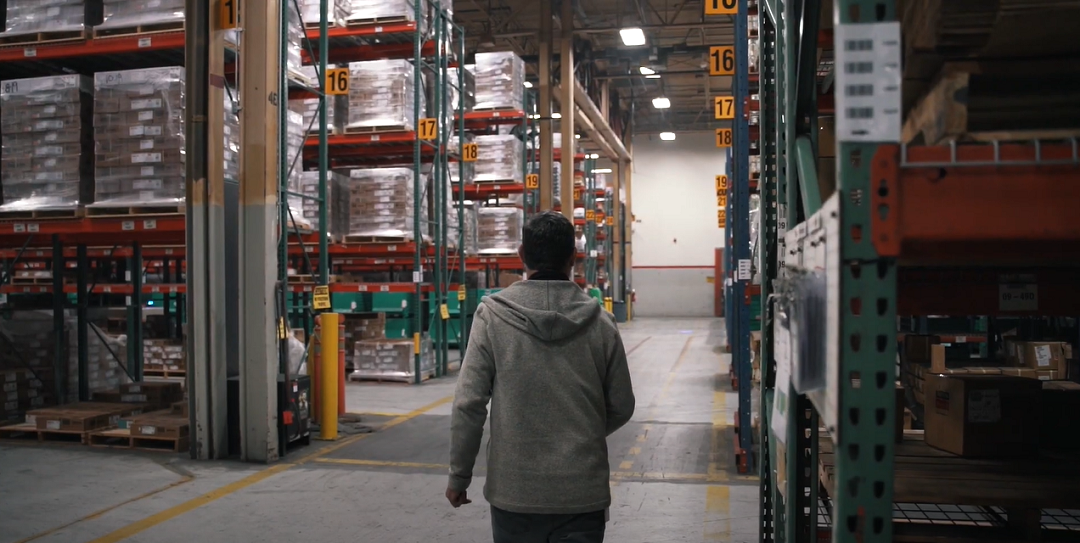
This summer I was able to explore Gallatin’s plant entirely and have been given a project to work on that has stretched my limits as an engineer. At Auburn, one of my favorite classes was machine manufacturing. I worked daily on lathes and milling machines fabricating incredibly simple devices and gigs. The work was simple but satisfying. I’d slowly scrape a tenth of an inch at a time off an aluminum block or another material, and I didn’t realize the real-world connection until now.
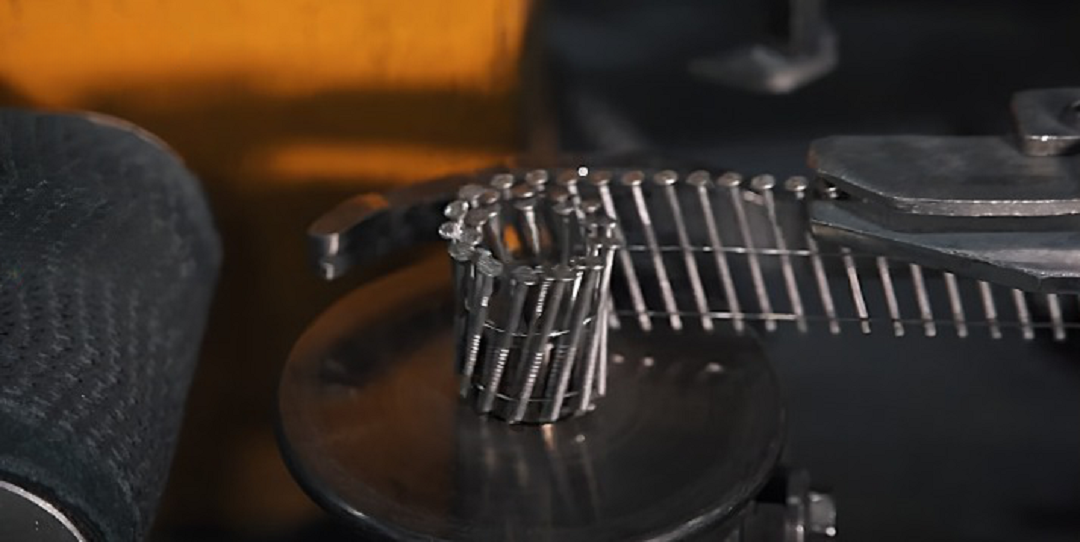
Upon arriving here in Gallatin, I was quickly blown away by the complexity of the manufacturing process for high-production screws and nails. There’s magnetized bowls that vibrate to orient and move screws upwards! They also create stronger fasteners than I ever could have at school, making use of cold forging to roll threads to make them stronger as opposed to cutting them. There’s plenty more I learned from the manufacturing process, but what I have enjoyed the most this summer has been exploring the design process.
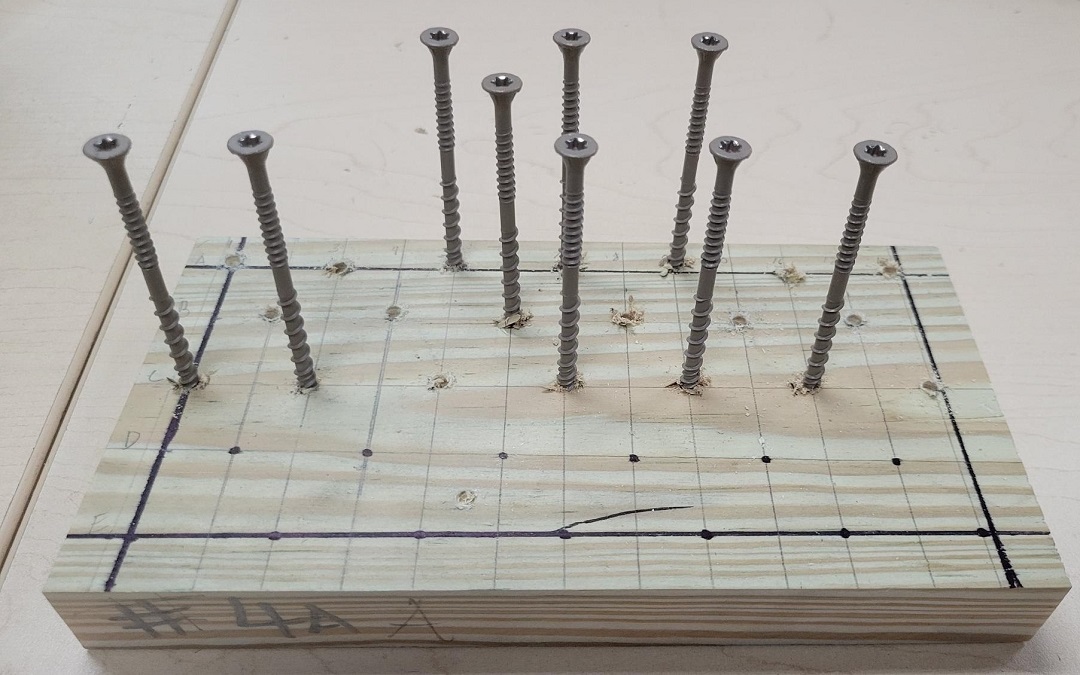
Here in Gallatin, I’ve been tasked with devising a new methodology. This methodology must explain the concept of “easability” in driving/starting a screw. In lay terms, when you apply pressure to a drill in driving a screw, there are several results you can expect. Some fasteners would buckle, others would drive in the wrong direction, and still others would burn out the wood instead of exploiting its structural strength. I’m seeking a way to test screws that would provide insight on which are the best for a specific task. What features are necessary or unnecessary?
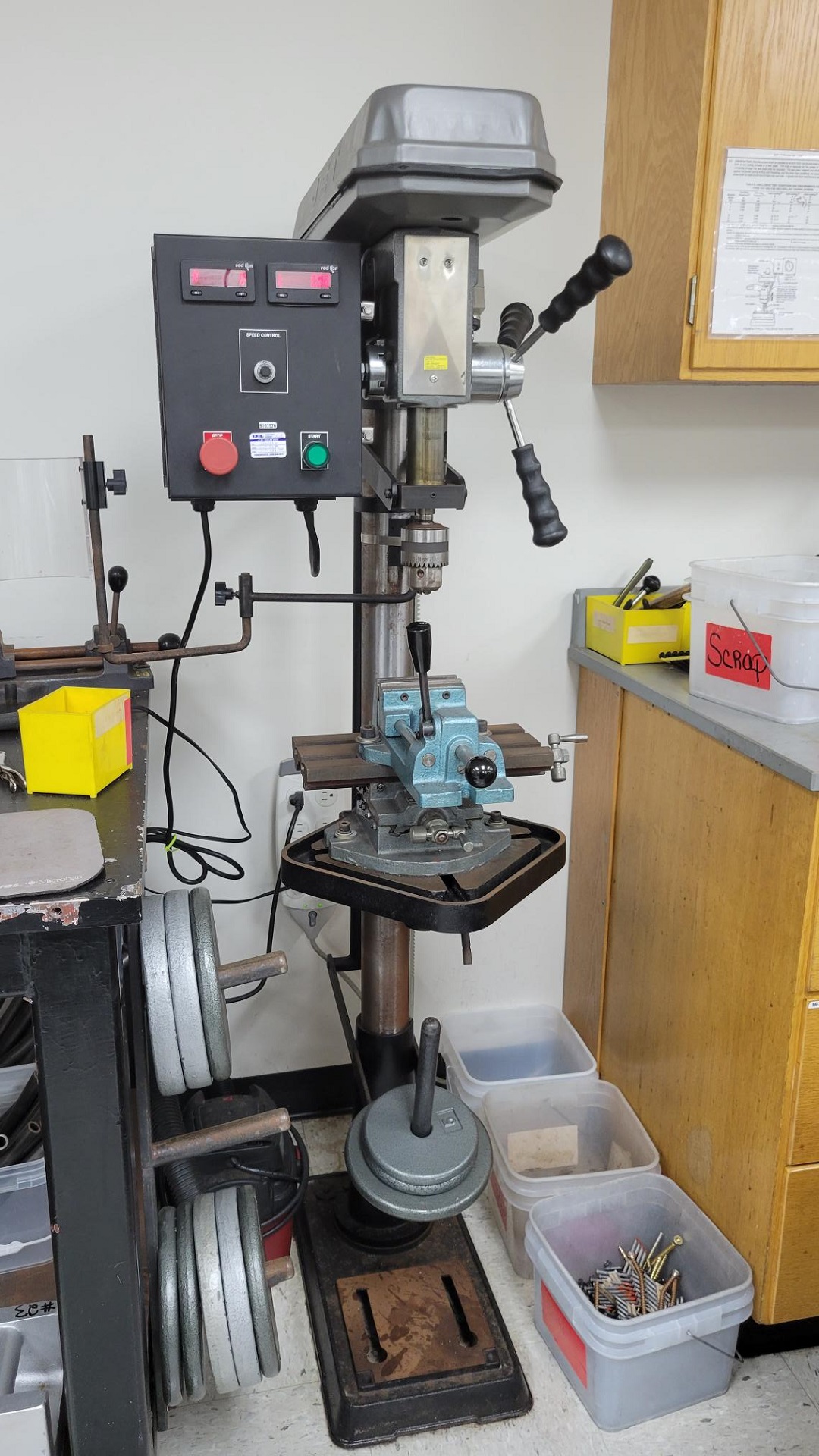
My testing strategy sent me first to the testing lab for preliminary findings. I then took a small amount of the screw testing data along with my knowledge from studying the wood handbook to develop a prototype piece of testing equipment. I came across several challenges along the way causing that caused me to revise my prototype until it was acceptable for my purposes. I then created work instructions for using the equipment and set up a list of the fastener attributes it could be used to test in the future.
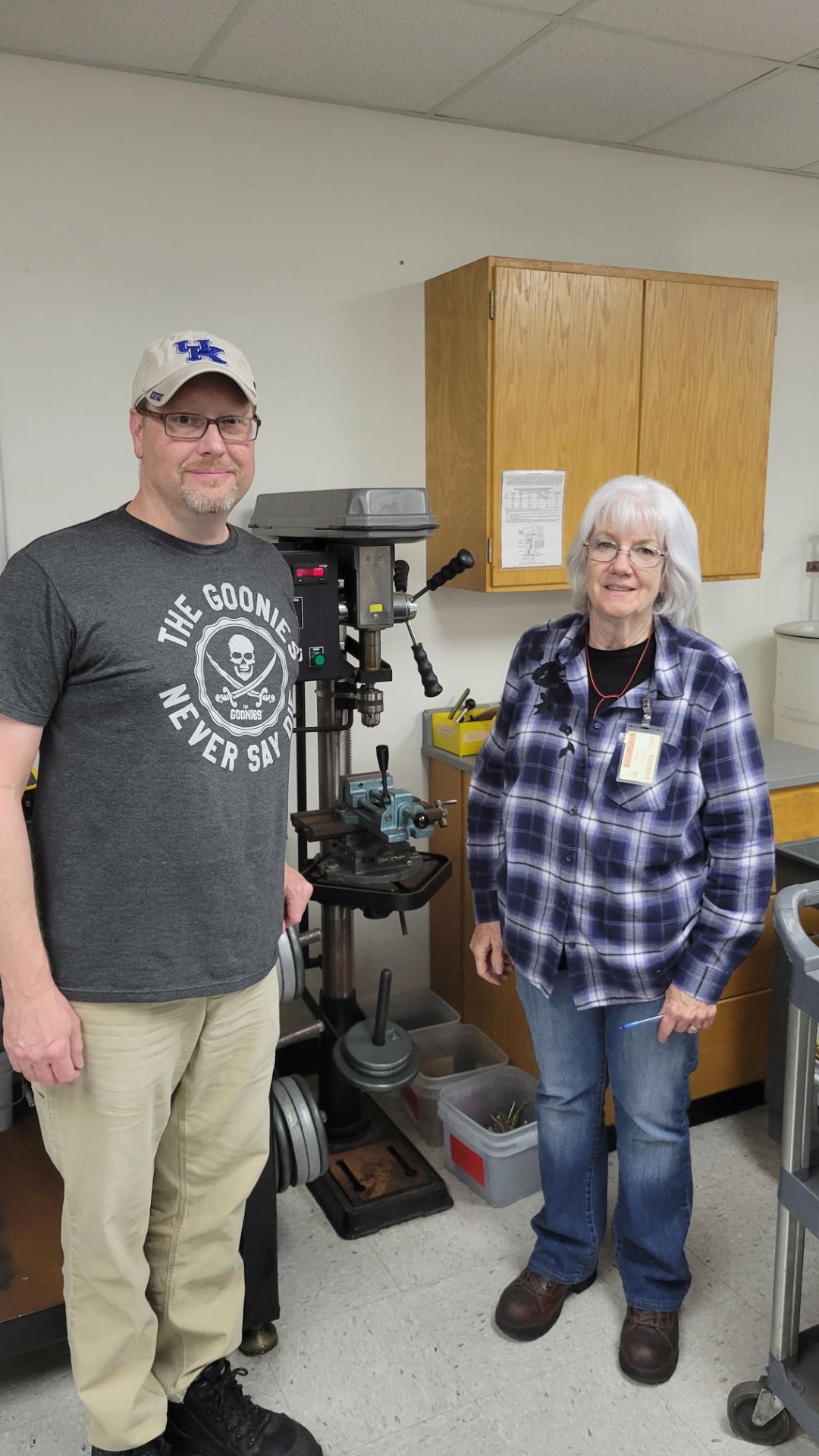
All told, this summer has been a fantastic experience. It has given me a glimpse into the workplace of an engineer and provided me with advice and professional connections I can carry with me in my engineering career. Already I know that the classes I’ll take in the next two years will make much more concrete sense to me than mere mathematical formulas on a page, and I’m so grateful for that. To everyone at Simpson Strong-Tie who has supported me — from Rachel Holland to all the mentors and leaders that have invested in me this past summer — I say THANK YOU. It has been a rich summer of experience for me, and I hope I can repay you in the impact I can go on to make within the career path we all love, being “engineers with a personality.”