On day three, I talked about our first holdowns, the HD2 thru HD15, which were welded holdowns that use bolts. A major innovation in bolted-holdown manufacturing was the introduction of our HD2A through HD20A holdowns in 1988. The “A” stood for automated because these products were manufactured on a die that stamps out finished parts, eliminating welding and significantly decreasing costs.
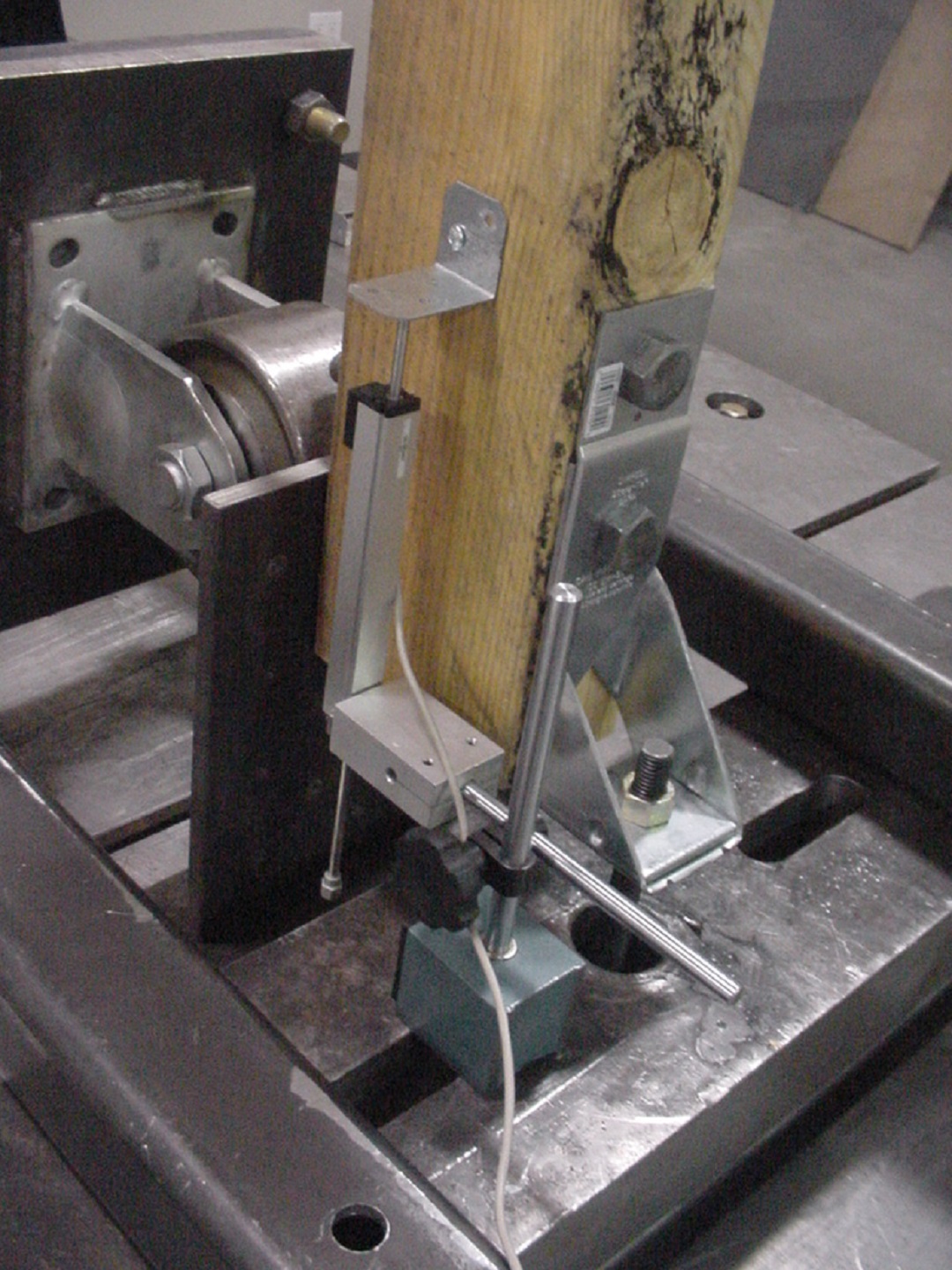
A number of years ago, I wrote a series of blog posts discussing product testing, including how we test holdowns. The test standard for holdowns, AC155 — Acceptance Criteria for Hold-Downs (Tie-Downs) Attached to Wood Members, was adopted in 2005 and required new testing for all holdown devices. In the course of retesting, we took the opportunity to incorporate new features into our bolted holdowns to improve their deflection performance. The outcome was that the HDAs became the HDBs.
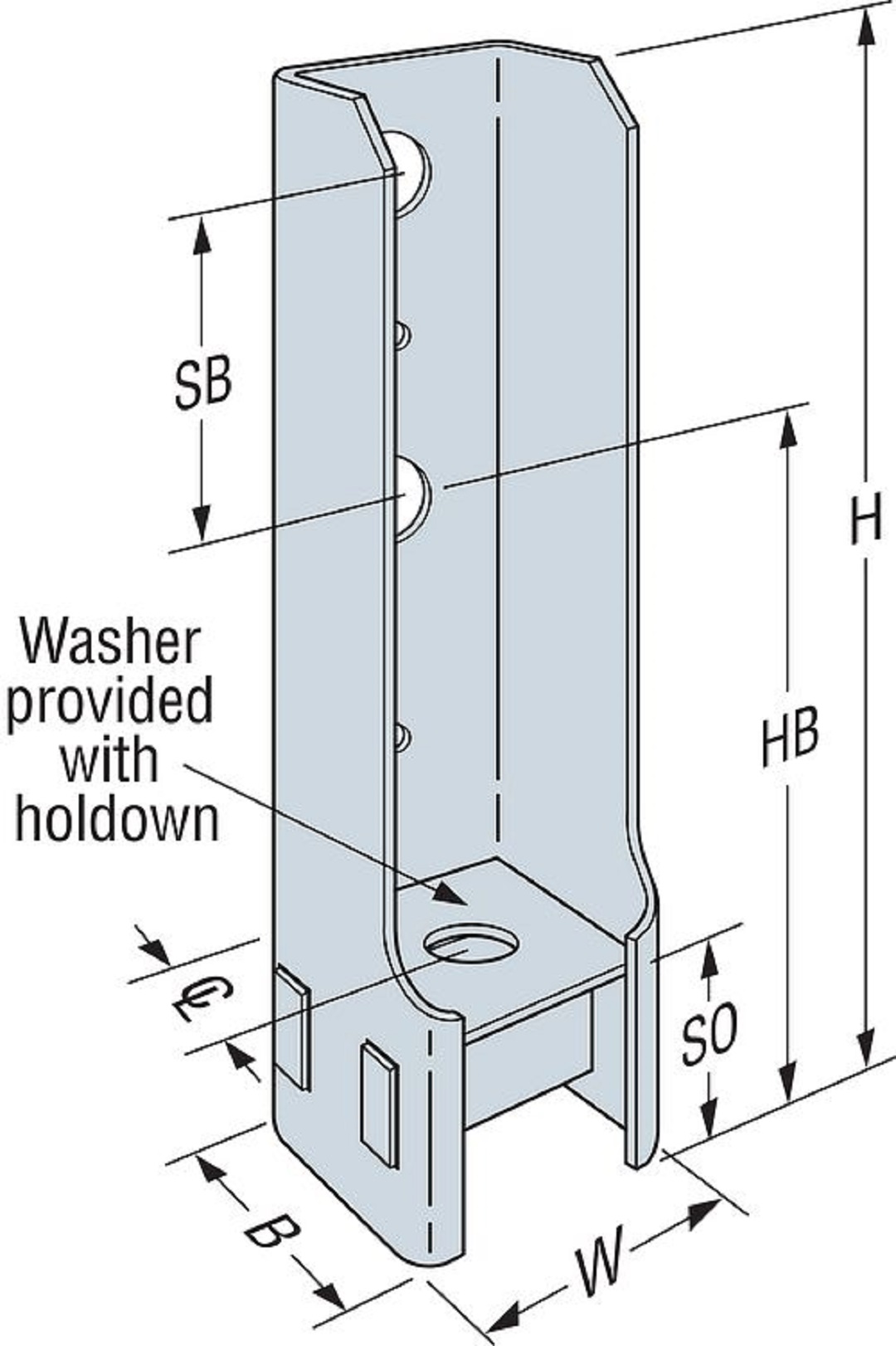
The HDB series of holdowns uses a pair of flat bars supporting a bearing plate for the anchor bolts to minimize deflection in the seat. We first developed this technology in the HDQ8 holdown, used in our prefabricated wood Strong-Wall® shearwalls.
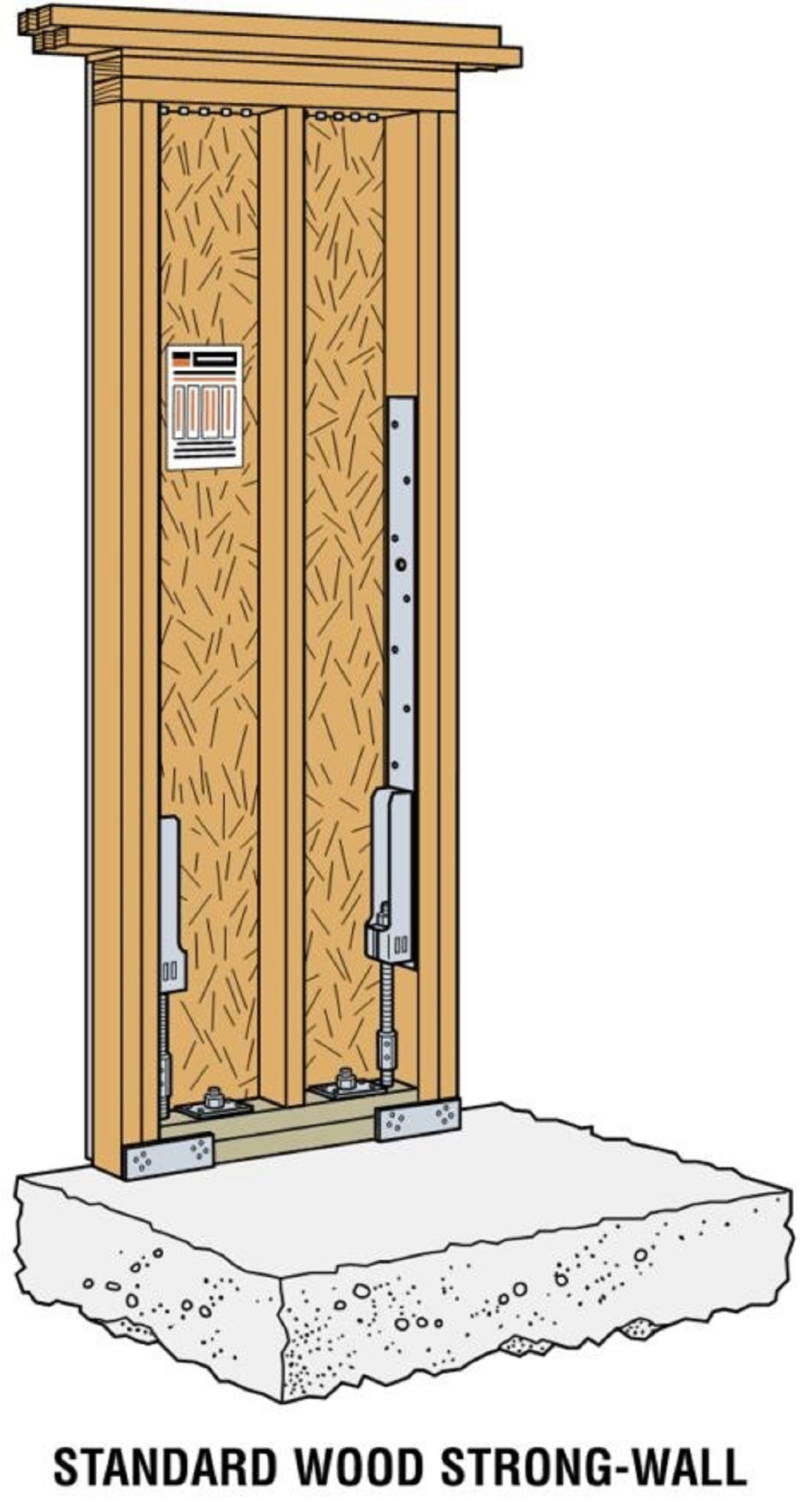
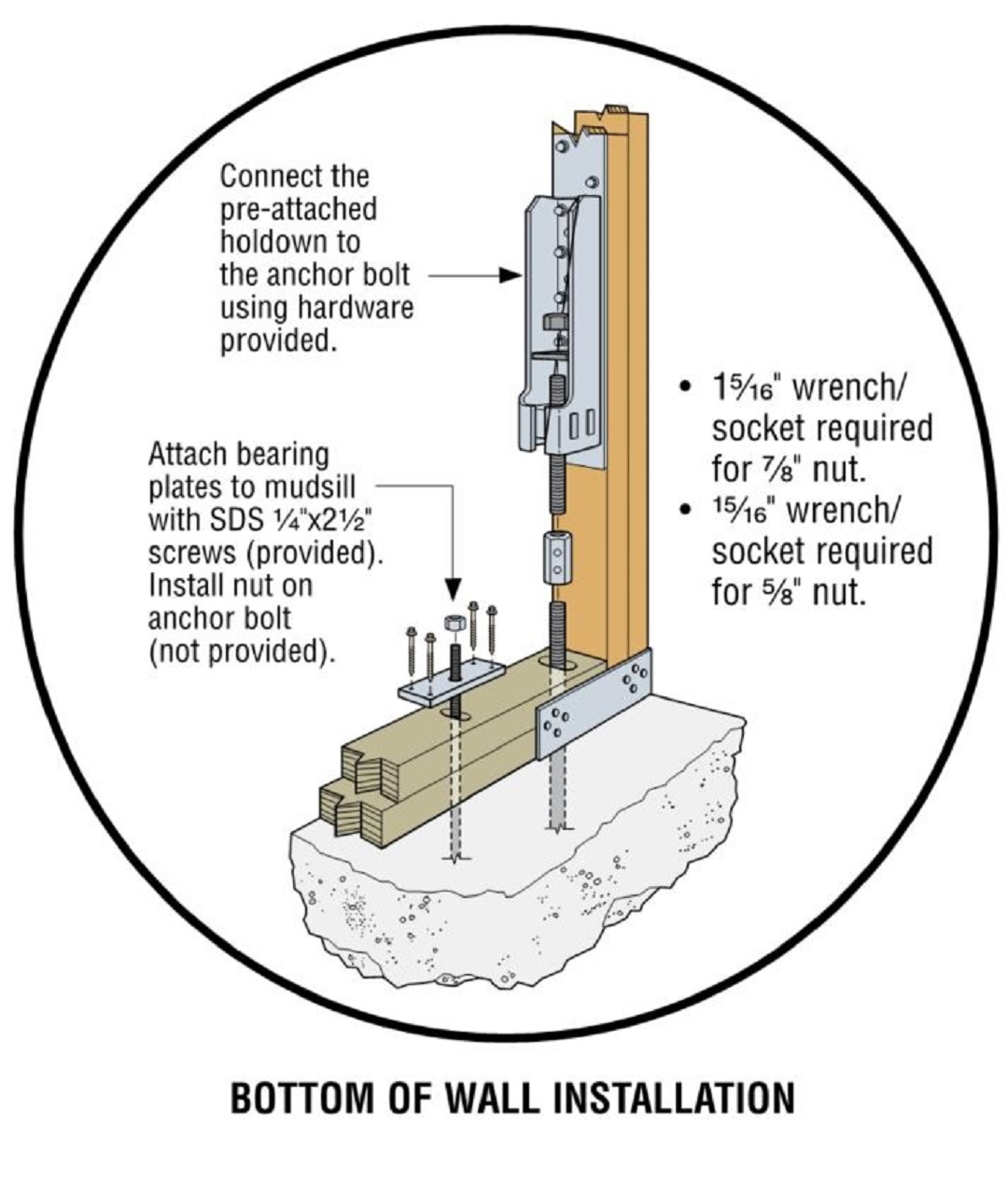
If you think the HDQ8 and HD9B holdowns look like siblings, you’re correct. Other than the fasteners, they are identical. Our tooling department removed the screw holes and replaced them with bolt holes.
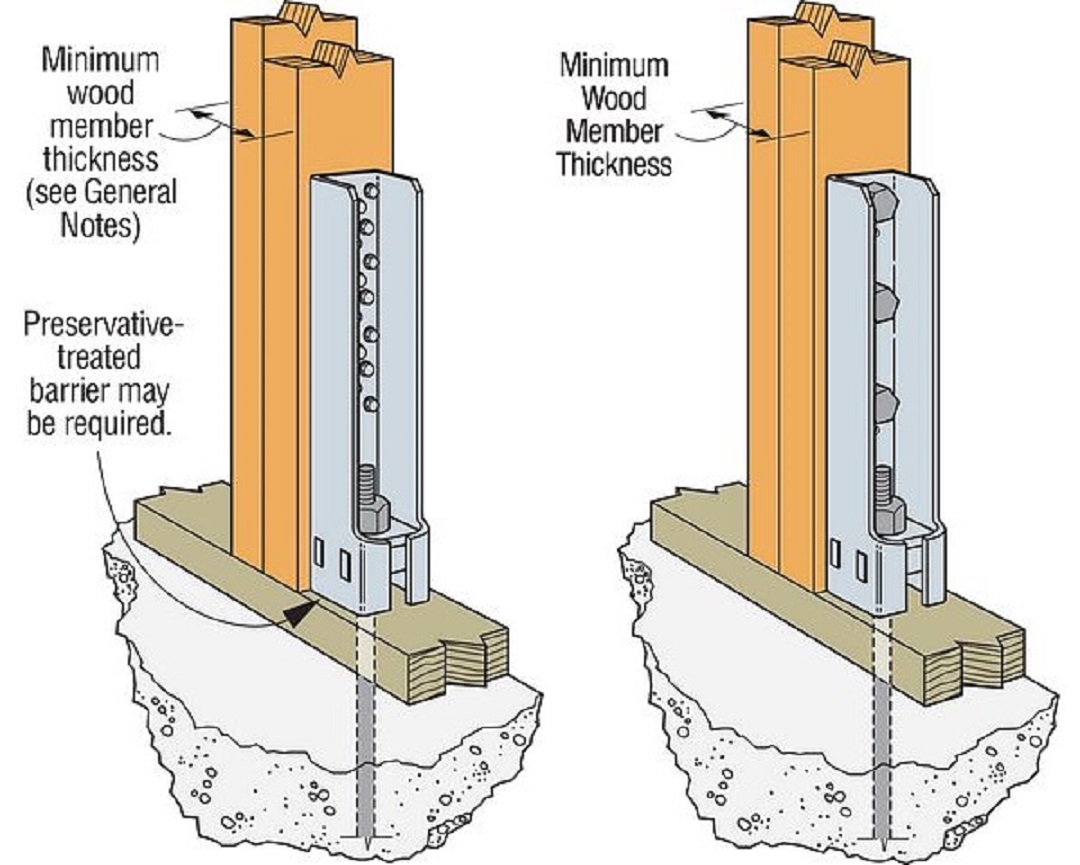
Of course, we tested them. An important aspect of AC155 is the requirement to test on a wood post assembly to evaluate deflection. We also just love testing.
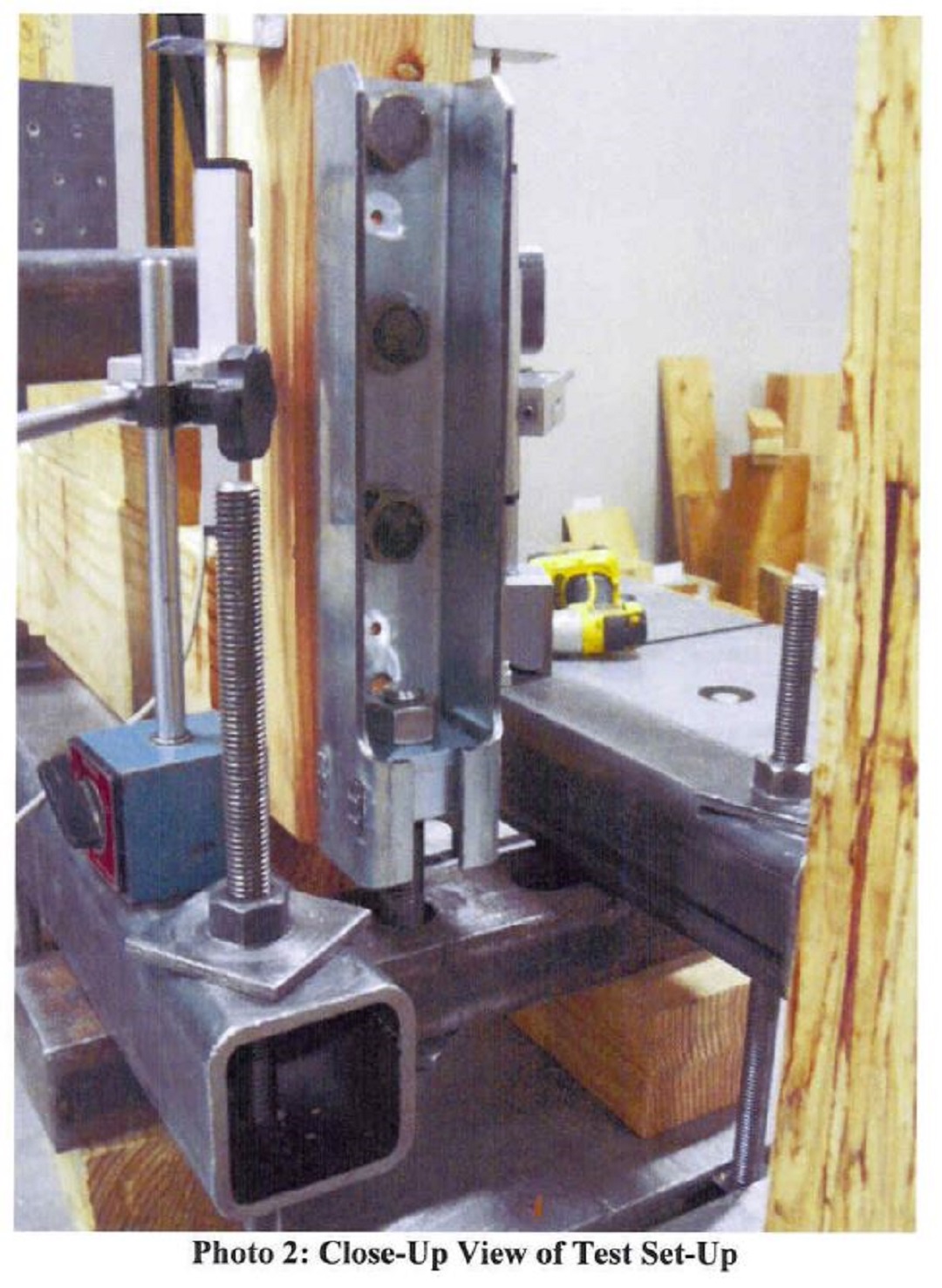