We’ve created a new, annual Excellence in Engineering award to honor and recognize the outstanding contributions of individuals in our Engineering department.
Our inaugural Excellence in Engineering winners had to meet the following criteria:
- They must be individuals who have outstandingly exemplified the Engineering department mission of innovating, testing, and supporting solutions that help people design and build safer, stronger structures.
- They must have demonstrated outstanding impact on the department, impact on other departments and branches, impact on our industry and communities.
- They must be department leaders in exemplifying Barc’s Nine Principles in how they approach and accomplish their work to serve their team and customers.
Nominations were submitted by managers and directors, and winners were selected by our home office and branch Engineering leadership teams.
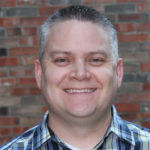
Russ Anderson — Sr. Project Manager, Engineer Technology (McKinney, TX)
Contribution: In 2021 Russ conceptualized, scoped, and facilitated the development of the Post-to-Beam Selector web application including a 3D visualization component that allows users to see connection geometry and custom part geometry. This application, with its visualization component, is the first of its kind and will significantly reduce the time it takes customers to receive a quote on their custom part and reduce the likelihood that the part ordered is incorrect with respect to the in-situ geometry. Visualization of connections and connection geometry is now being incorporated into all future applications, especially those that can or will handle “special” product geometries.
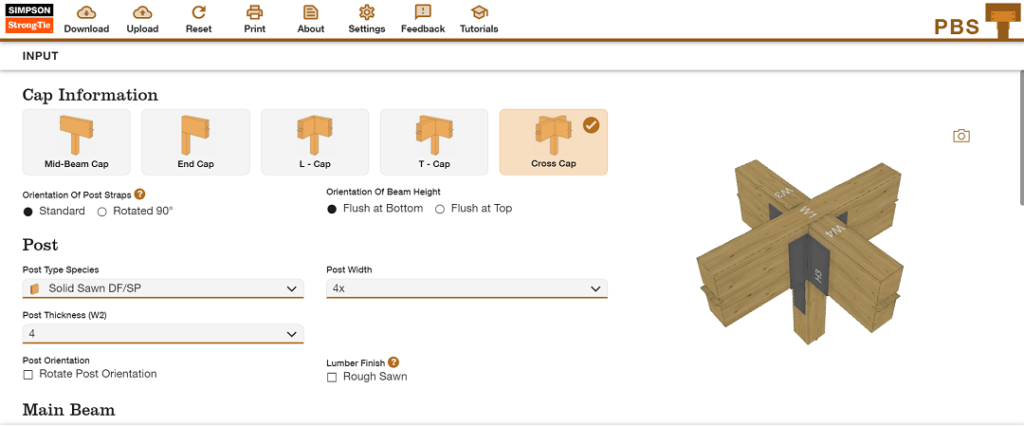
Summary: For developing key visualization capabilities to take our technology tools to the next level, a relentless focus on improving drawing content for our customers, and providing a resource to many throughout the company.
Demonstrating Barc’s Nine Principles:
Relentless Customer Focus: The turnaround time for customers to access drawing content has been reduced to less than 48 hours.
High-Quality Products: Post-to-Beam Selector and Adhesive Cartridge Estimator were very large work efforts that yielded two of our best web applications to date.
Enable Growth: Russ has taken a Project Engineer in Viet Nam under his wing and works with him daily to grow our visualization technologies.
Give Back: Russ regularly volunteers in Hurricane cleanup efforts, often spending his weekends helping clean flooded houses, etc.
Have Fun, Be Humble: We’d be hard pressed to find a single person who would describe Russ as having anything but a good/positive/can-do attitude.
From his nominator, Guy Anderson (no relation):
“Russ is not an engineer, but I submit that there is nobody in the Engineering department that holds a candle to Russ’s ability to visualize products and the construction process.
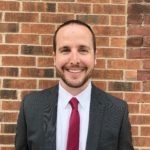
David Finkenbinder — Branch Engineer (Columbus, OH)
Contribution: In 2021, David delivered tools and assets to the industry at an outstanding breadth and scale that not only supported our sales growth goals, but also contributed to our mission of safer structures. These advances included the following:
- Structural fastener detail sheets: David led a team of branch engineers and Engineer Services in Viet Nam to release four new detail sheets to support the conversion to, and specification of, our structural fasteners. These included sheets for ledgers, built-up beams, built-up columns, and wood-to-steel. These sheets were the foundation of a salesforce.com dashboard that tracked a branch-wide sales initiative to convert generic lag screws and bolts and competitive structural fasteners to our solutions.
- Deck safety: David has long been our resident deck expert and this was on full display in 2021. His primary task was to develop a Simpson companion to the AWC DCA6 document that would provide a list of connectors, fasteners, and anchors that satisfy this design guide. The result was T-C-DCA6DECK21, a 12-page comprehensive bulletin that concludes with a worksheet that produces a material list of Simpson products that can be taken to any local Simpson dealer. To support this document, David worked with marketing on a Deck Code Compliance web page and partnered with AWC to hold a joint webinar on the document that had over 2,600 registrants. All this was done at the same time David was supporting our Deck Planner Software and recording tutorials to train all the company’s Branch Engineering Technicians on how to provide technical support to end users, to support the broader roll-out of this Outdoor Living software.
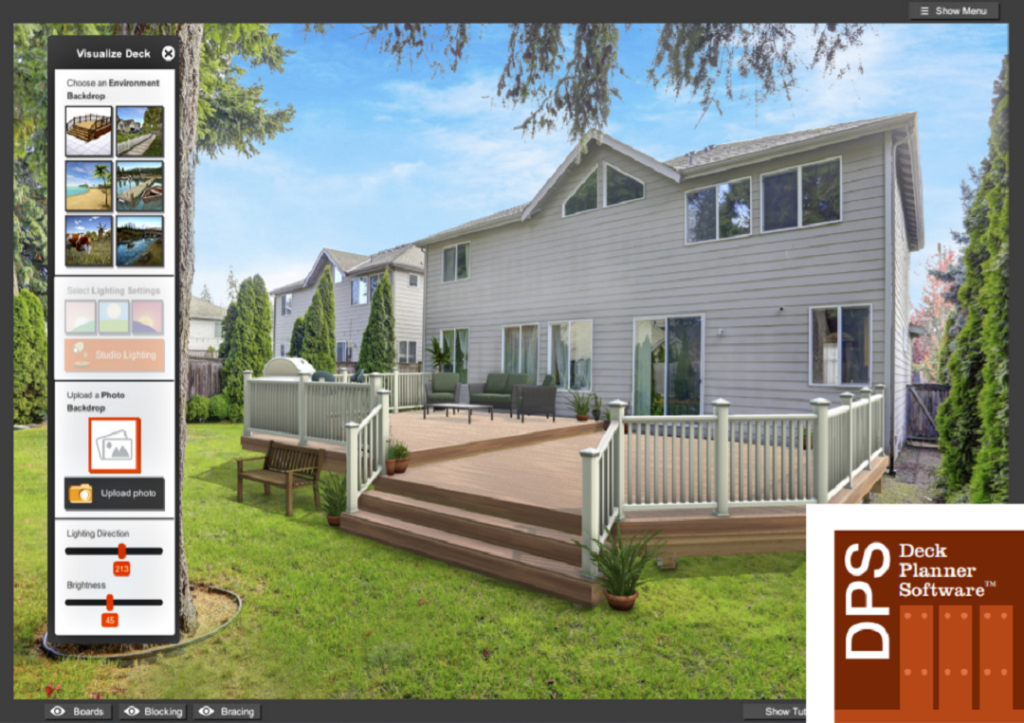
Summary: For being a leader at the branch by initiating a continuous improvement program for his team; being a leader at Simpson Strong-Tie by launching new design tools; and being a leader in our industry by developing a new code-compliant tech bulletin and web page that he shared in a hugely popular national webinar.
Demonstrating Barc’s Nine Principles:
Customer Focus: After spending much of 2020 responding to huge increases in home center customers submitting online questions, David took it upon himself to improve the knowledge of our Engineering Technicians to ensure we are providing the best customer service possible. After reading Atomic Habits by James Clear, David was inspired to set up 30-minute training sessions every week to help trainees improve “1%” with every session. The content has been very well received and undoubtedly helped all involved. And David leads by example. Through October this year, David has owned 350 tech questions sent in via email or website, which is over 100 more than any other engineers at our branch.
Be the Leader: David has long been the company leader in wood decks and has grown into an industry leader through his involvement in national organizations, authorship of published articles, and devotion of time and expertise to improving deck safety.
From his nominator, Shane Vilasineekul:
“Not only was David able to deliver these tools and assets to complete his own goals, but he also took the time to teach others how to use them to be more successful in their roles.”
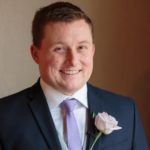
Joe Cullen — Chemist (West Chicago, IL)
Contribution: Shifting production from Baltimore and Addison to West Chicago was an enormous task. As many of our products are code listed and on several approval lists, a change in manufacturing location must be vetted to ensure product performance remains the same. In essence, every product manufactured at West Chicago required validation prior to filling orders. Performance testing of all chemical products was a huge undertaking, and Joe Cullen stepped up to be the liaison between Manufacturing and Engineering for chemical production in West Chicago.
When bringing SAP into West Chicago, it became apparent the existing new-product development process did not adequately address the new requirements for the software change. Joe worked with Manufacturing, Purchasing, Inventory Control, Product Management, EHS, and the SAP team to develop work instructions detailing the requirements for transitioning new products, and changes to existing products, from Research and Development to Manufacturing. Developing this process required identifying the issues and information needed at every step of the process; individual stakeholders at all levels were identified and provided input as to what they needed and what they provided to the process. Joe’s work laid the foundation for efficient and thorough data transfer required for new product launches and changes to existing products.
Summary: For his risk-taking innovations exploring formulations, enabling us to keep products on the shelf during major supply chain issues, being a continual leader of process improvements, and a reputation for getting the job done from development to production.
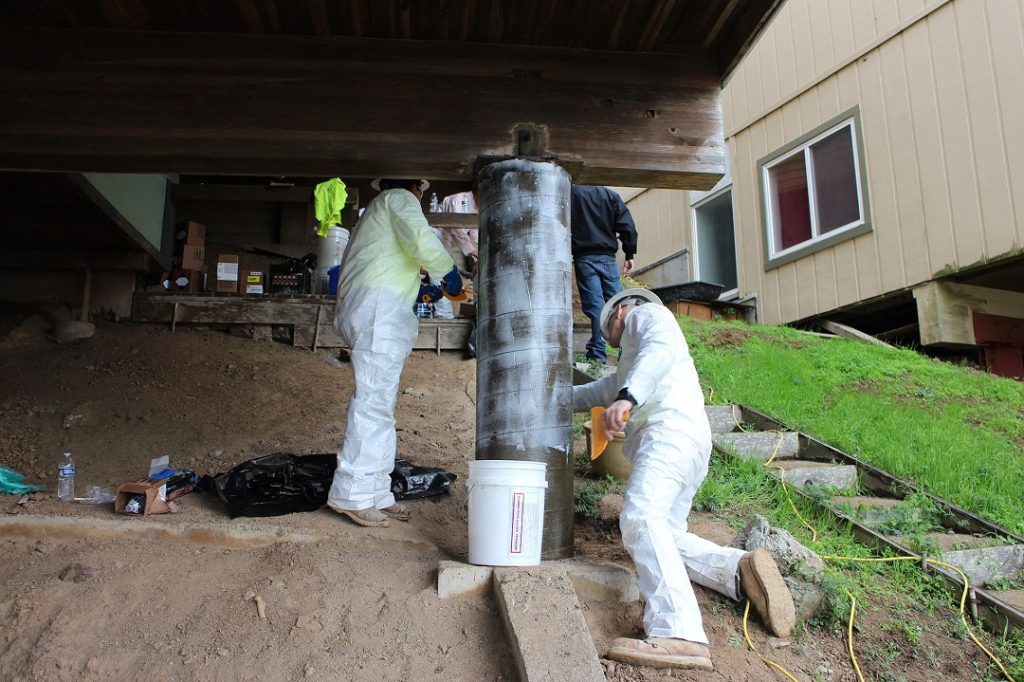
Demonstrating Barc’s Nine Principles:
Risk-Taking Innovation: The development of CSS-ES and CSS-EP demonstrate the commitment to High-Quality Products and Risk-Taking Innovation.
Relentless Customer Focus: Stepping up to ensure Spinergy had product to keep operating demonstrates Joe’s customer focus.
Be the Leader: Joe chose to Be The Leader, ensuring compatibility with SAP and our new product development process.
Enable Growth: In West Chicago the phrase “Joe’s on it” means a lot. People here know that his scientific ability and determination will ensure success.
From his nominator Quentin Hibben:
“Joe’s expertise in our products was earned over the past nine years by making each product and learning what each ingredient does to provide the performance we need. This expertise was critical during the force majeure limitations on chemical raw materials over the past year. Joe was able to quickly revise three key products to ensure we continued to meet customer demands: SET-XP, FX-70-6MP, and FX-3120HT.”
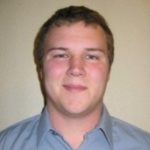
Alex Daddow — Field Engineer (Stockton, CA)
Contribution: Alex Daddow, while still new-ish to Simpson Strong-Tie, has gone above and beyond to find ways to innovate, collaborate, and both reach and service Engineering customers, specifically during the heart of the pandemic, which has hit the Pacific Northwest harder than most locations. Alex was able to determine that engineers were not even working in their offices and so as a CSS Field Engineer who spends a lot of time at many jobsites, Alex determined that the best way to meet engineers (many for the first time) was to invite them to join him at the site while he was doing site observations for their projects. This not only allowed him to meet engineers, but also gave those same engineers the ability to see right away that he was a “value-add”. From a solutions standpoint, he worked on one specific project in Alaska that proved he could come up with innovative solutions. Alex helped to determine a solution incorporating FRP + carbon anchors to be used with the FRCM system to help create a better bond to the substrate with the existing FRCM in place.
Summary: For being a huge value-add to our customers and continually finding ways to go above and beyond to innovate and collaborate and deliver relentless customer service by finding design solutions to grow our business.
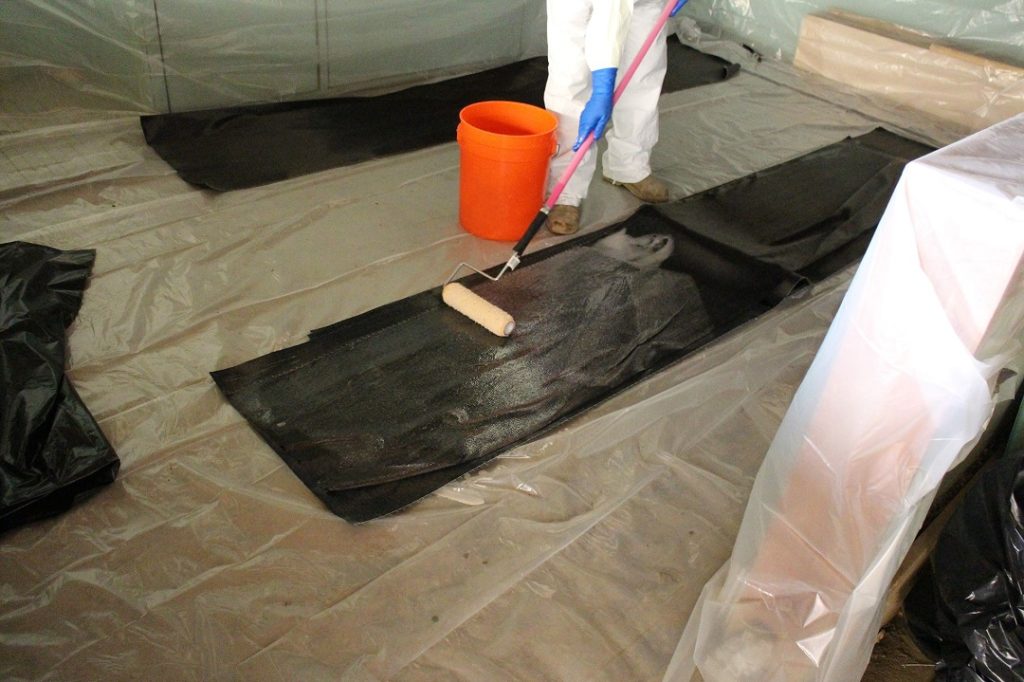
Demonstrating Barc’s Nine Principles:
Relentless Customer Focus: Alex drove for several hours specifically to turn in a bid that had to be hand delivered to Seattle Public Schools.
Long-Range View: Alex is always planting seeds for the next job, not sacrificing long-term relationships for short-term gains. While FRP wasn’t specified for the McNary Dam job, Alex has worked further with USACE on many projects since then.
Have Fun, Be Humble: Alex does both so well gaining the respect and admiration of everyone he works with. All of the sales team loves working with him. I see on a daily basis how he shows respect to every person regardless of their professional status. Additionally, he is a fun person to be around. He has a yearly Super Bowl sausage party (really) in which hundreds of sausages are made from fresh meat which he selflessly shares with his teammates.
From his Nominators: Wendy Allen and Louay Shamroukh
“Alex Daddow is the go-to guy for anything you need done.”
“Alex Daddow embodies Simpson Strong-Tie. I am proud to have him on my team!”
Congratulations to these standout folks for their incredible contributions to the Engineering department and our company!