The future of full-scale structures testing and product development is here – and it is BIG. Our Tyrell Gilb Research Laboratory built a brand-new Million Pound Rig to help in the testing of our new Yield-Link® brace connection (YLBC), along with our many other products. Hear from Mike Wesson, Engineering Manager, Tyrell Gilb Research Laboratory, about this latest addition to the research lab.
The need for larger force capacity became apparent as Simpson Strong-Tie began entering the structural steel market. We had stretched the limits of the existing equipment when we had to figure out how to use two of the 55 kip (55,000 lb) actuators together to push and pull on a Yield-Link® Moment Frame with a 36”-deep beam. To go even bigger for subsequent test programs with larger capacities, we needed to contract with university labs. Now, with the added capabilities of our Million Pound Rig, we’ll be able to support our growing market areas in structural steel, mass timber, and concrete strengthening.
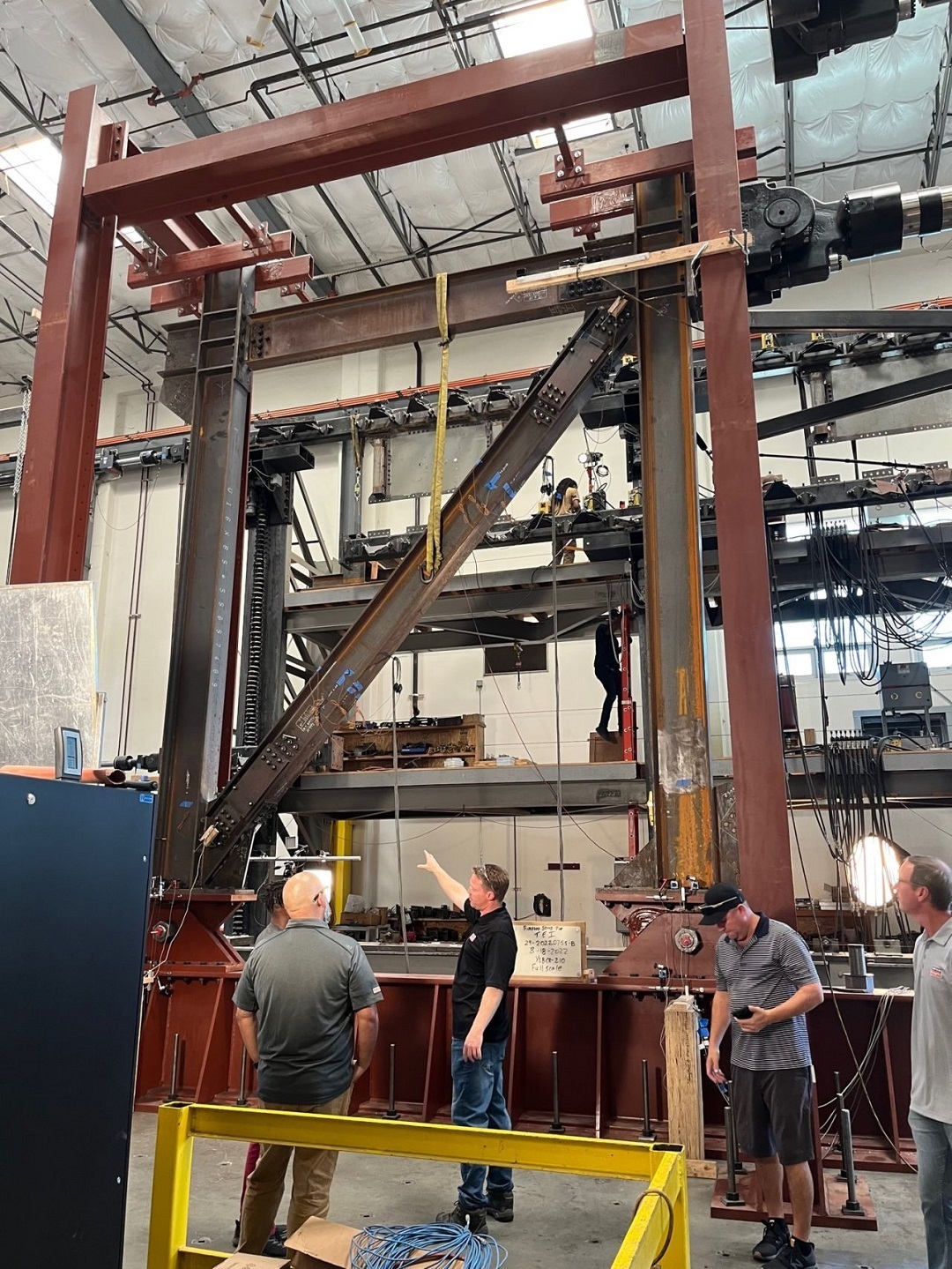
The new rig has already been put to use to test full-scale steel-braced frames for the Yield-Link® brace connection (YLBC), product development testing for mass timber, and concrete shearwall strengthening with FRP (fiber reinforced polymers). Future testing plans include additional rounds of concrete shearwall strengthening, more mass timber product development, and additional structural steel product development.
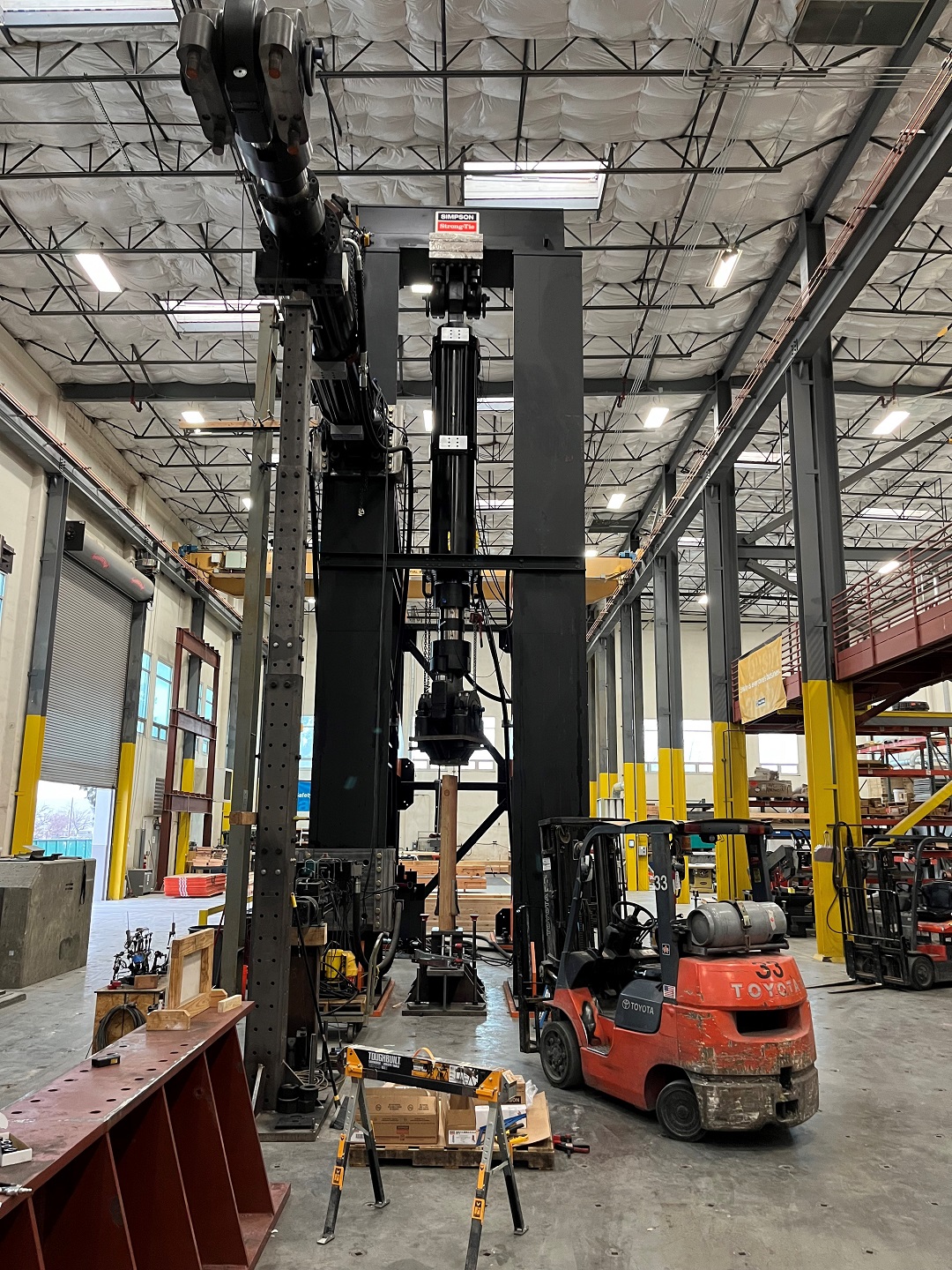
This rig consists of a three-story tall reaction frame, two 24-foot-long, 23,000 lb actuators (think a big hydraulic arm that pushes and pulls on the test specimens) each capable of exerting 550 kips (550,000 lbs) of force, with a total stroke of 48 inches (+/- 24 inches). As part of the planning and design for the structural steel reaction frame that the actuators push and pull against, we analyzed the existing strong floor and the reaction frame using 3D finite element analysis (FEA) simulations to make sure we weren’t going to damage the three-foot-thick, heavily reinforced strong floor that the frame is anchored to, in addition to the frame itself, when we reach the capacity of the actuators. This newly installed test rig is capable of applying 1.1 million pounds of force in both push and pull directions. Installed next to the huge reaction frame in the photos is one of the full-scale test frames from the YLBC test program. Below are some of the key rig statistics.
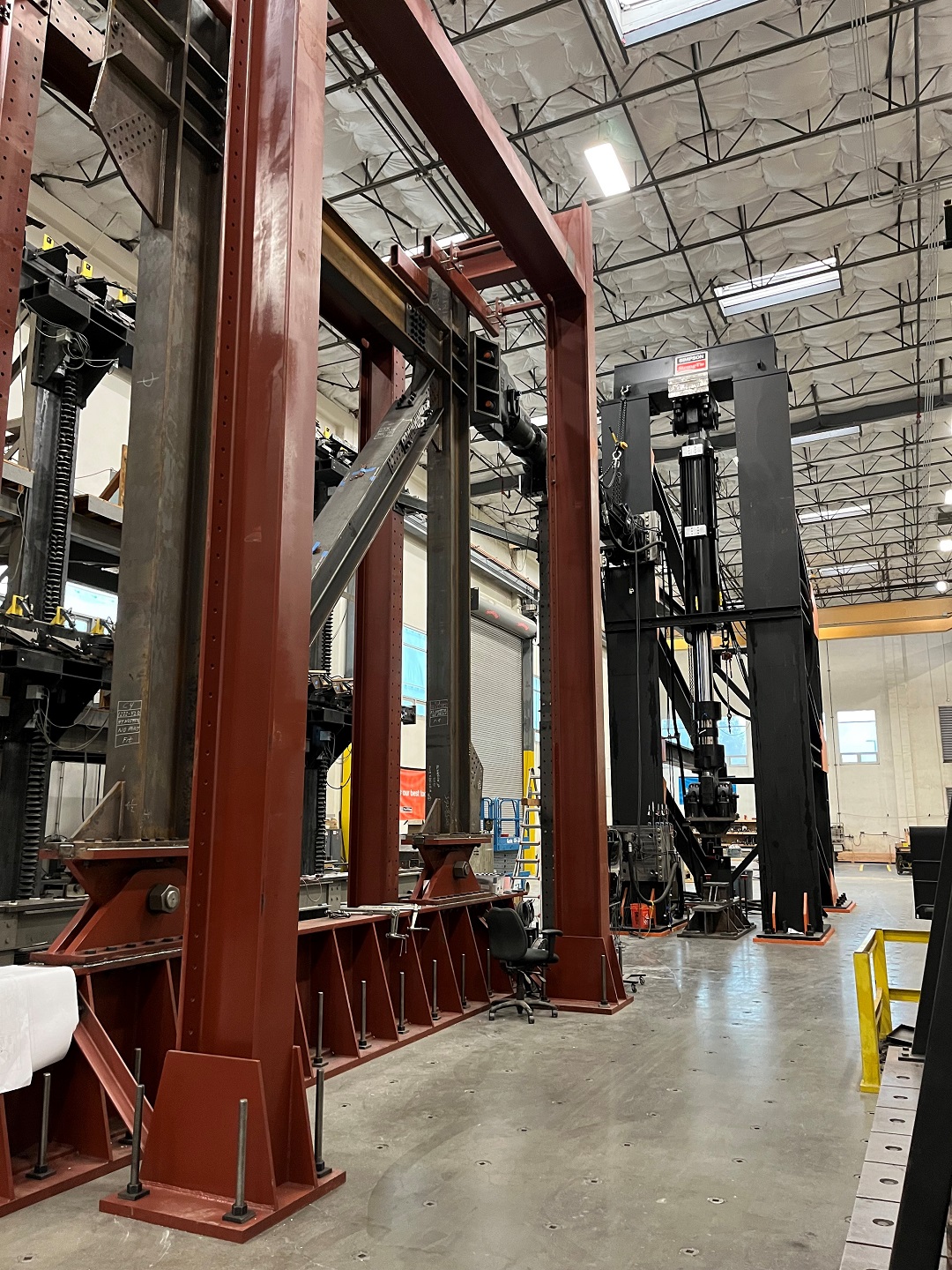
- Five loading configurations
- 1 story / 1 actuator, lateral (+/- 550-kip capacity)
- 2 stories / 2 actuators, lateral (+/- 550 kip-capacity each)
- 1 story / 2 actuators in parallel, lateral (+/- 1100-kip capacity total)
- 1 actuator, vertical (+/- 550-kip capacity)
- 2 actuators in parallel, vertical (+/- 1100-kip capacity total)
- Actuators can be placed anywhere from 4′ to 30′ from the strong floor for lateral loading
- Capable of testing structures up to 30′ tall and 100′ long for lateral loading
- Each actuator has a +/- 550-kip capacity and a +/- 24″ stroke (48″ total stroke) which allows loads up to 1.1 million pounds when coupled together in parallel
- Reaction frame weighs approximately 120,000 lbs
- Each of the four reaction frame columns is anchored with (8) 2-1/2″ A354 BD rods and each tensioned to 450 kips which is 3.6 million pounds per column and 14.4 million pounds total
MPR View of Reaction Frame with Braced Frame Specimen Beyond
Over the first three test programs we’ve already recorded maximum loads of approximately 500 kips of force on single actuator configurations (on both lateral and vertical actuator orientations), and we’ve already required the use of both actuators in parallel for lateral loading of concrete shear walls strengthened with FRP (reaching up to approximately 870 kips). To put the 1.1-million-pound capacity in perspective, that is equivalent to the weight of approximately 230 Ford F-150 trucks or a little more than the weight of four adult blue whales.
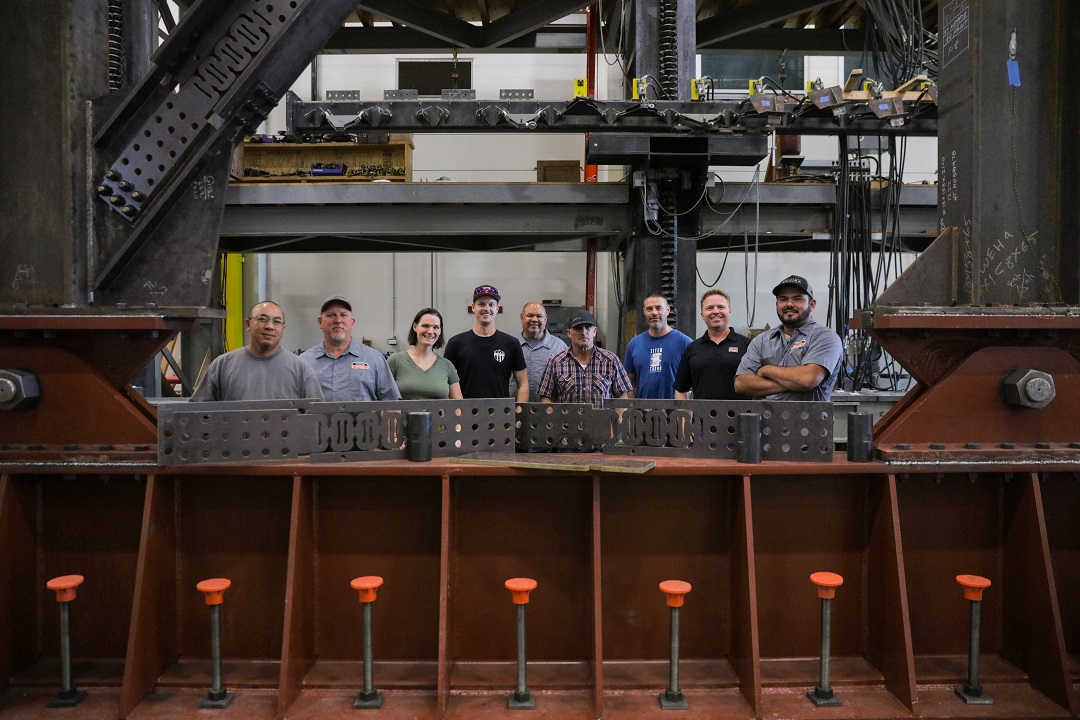
With this newest addition, we’re making sure that the Tyrell Gilb Research Lab has the best capabilities and the best team to help take the company to even greater heights.
You can learn more about the lab and take a virtual tour by watching our video below.