I write a lot about testing on this blog, from my first post about testing to the series I did on how we test different products (hangers, holdowns, fasteners). This week I’d like to highlight some unique testing we’ve been doing to support one of our new product lines. Simpson Strong-Tie® recently introduced our Repair, Protection and Strengthening Systems for Concrete and Masonry. The new product line is the result of our acquisition of Fox Industries, Inc. in 2011.
In the past, I’ve shared some of the more fun tests we’ve run, like the bowling ball test or 40 kip hangers. This week we’ll take a sneak peek at testing of the FX-70® Structural Repair and Protection System. FX-70 uses high-strength fiberglass jackets and high-strength water-insensitive grouting materials to repair and protect wood, steel, and concrete structural members. The system is primarily used on piles in marine environments.
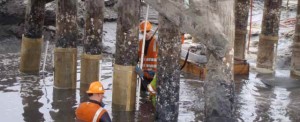
The system has been used successfully for more than 40 years with the first installations in 1971 still in service today. Our testing challenge was to evaluate the performance of the system under seismic loading. First we had to define what that means for this type of system and the types of structures it is used on. We settled on testing the cyclic bending capacity of damaged and repaired piles in a cantilever column condition. Timber pile systems are subject to a variety of types of damage. Marine borer attack at the waterline is a common occurrence, so we focused on that type of repair.
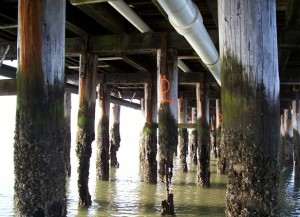
Timber pile systems are typically braced by batter piles or X-bracing. The connections of the bracing system generally do not have enough capacity when the structure is subject to large earthquake displacements, so the piles are analyzed as a forest of cantilever columns. The test protocol we used is the cyclic CUREE protocol found in ASTM E2126.
Once we sourced the large diameter timber piles (harder than one might think), we wanted to simulate marine installation conditions as closely as possible. So we created a marine environment at the Tye Gilb test lab. The salt water conditioning tanks extend into the basement through two large access panels in the floor.
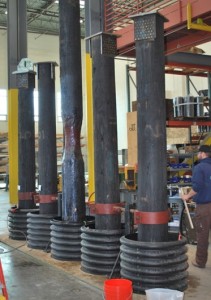
This enabled us to soak the piles before the repair, install the repair materials under water and condition the repair in salt water. Since the repairs are typically at the waterline, half the repair is under water.
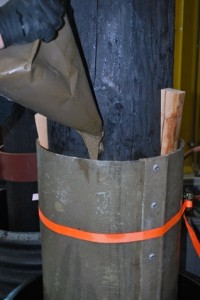
The testing was performed on 16-inch diameter, 18-foot tall creosote-treated Douglas-fir timber piles. We chose creosote-treated piles to evaluate the influence of the treatment on the bond of the FX-70-6MP Marine Epoxy Grout to the wood pile. Creosote was the common treatment when these structures were built and is an oily liquid. Adhesion tests on treated and untreated piles showed no negative effects on the bond due to the creosote chemicals.
Once the repair has cured, the specimen is craned into place and clamped at the base to create a fixed base condition. The percentages you’ll hear called out in the video are related to the lateral displacement of the top of the pile. The 100% cycle is 5.4 inches in each direction and we’ll push it all the way out to more than 17 inches at failure.
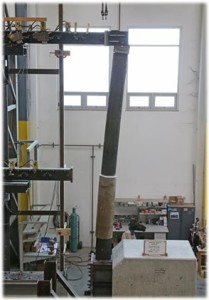
The testing video is of a 25% cross section loss specimen repaired with a 5 ½ foot long jacket that extends 18 inches beyond the damaged area. There is a ½ inch annulus (space between the jacket and the pile) that is filled with the FX-70-6MP Marine Epoxy Grout. Enjoy the show!
Have you had the opportunity to work on a marine structure repair? Tell us about it by posting a comment.
– Paul
FX-70® Structural Piling Repair and Protection System
For complete information regarding specific products suitable to your unique situation or condition, please visit strongtie.com/products/rps/fx70 or call your local Simpson Strong-Tie RPS specialist at 800-999-5099.
These repair/retro-fit “documentaries” are fascinating, even if some aren’t applicable to us far-from-beach-front types. May I suggest another subject in the same r&r line, the seismic up-grade of typical 19th c. churches with un-reinforced brick sidewalls for a sanctuary the equivalent of two stories in height. I have, in the past and unsuccessfully, suggested steel columns, dressed off as traditional pilasters on the interior , between the windows and secured with moment-resisting connections to the main floor frame below and the heavy-timber roof trusses above, and I’m about to approach a local church building committee with something similar. This time, an article from you on this subject would give my presentation more credibility.
Martin Harris
Jonesborough, TN.