We structural engineers here at Simpson Strong-Tie have a love/hate relationship with anchorage to concrete. Ever since the introduction of the strength design provisions in the 2000 IBC and ACI 318 Appendix D, anchorage to concrete has been a challenge for designers, building officials and manufacturers. SEAONC’s recent testing and the resulting code changes offer some relief to wood-frame designers for sill-plate anchor design at the edge of concrete, but many challenges remain.
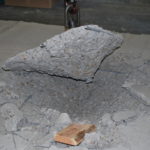
With the increasing demand for high-density housing and urban infill projects, designers are now faced with anchoring multi-story wood-framed shear walls to relatively thin elevated concrete slabs (typically referred to as podium slabs). Overturning tension anchorage forces at the ends of shear walls in these projects can routinely be in the 40 kip range and even get as high as 60 kips or more.
A 1” diameter high-strength anchor in the middle of a 12” thick, 5,000 psi uncracked concrete slab will achieve roughly 35 kips in tension at allowable stress design (ASD) levels for wind and low seismic loading; much less than that at the edge of slab. In higher seismic risk areas, the code requires an additional 0.75 reduction in design strength. Appendix D also has ductility requirements that can be met in a few different ways. [For more details, see ductility discussion below for different code requirements.]
The anchor capacity in the previous example would be reduced to approximately 25 kips at ASD level for seismic, but it may not be suitable for use in Seismic Design Category C or higher because the steel strength exceeds the brittle concrete breakout strength.
So what are designers doing and what are building departments accepting? Well, lots of things. Some designs include large-plate washers, added reinforcement, or punching shear calculations used for columns. While some of these options may increase the capacity of the anchor, they don’t necessarily fit within the design provisions of ACI 318 Appendix D. This is a challenge we want to continue to address in the blog. But in the meantime, I’d love to hear about your issues with anchorage to concrete podium slabs.
What are you doing to address the challenge? Let me know by posting a comment.
– Paul
SIDEBAR: Ductility Discussion
ACI 318 Appendix D Section D3.3 has seismic ductility requirements that require the designer to protect against a brittle concrete failure in moderate to high seismic areas. Reducing brittle failures and promoting ductile failures, such as steel yielding is fundamental to seismic design. However, the code language of ACI 318 can be confusing.
ACI 318-08 vs. ACI 318-11
ACI 318-08 Section D.3.3.4 requires that “anchors shall be designed to be governed by the steel strength of a ductile steel element.” Designers often question what steel and concrete strengths to compare when evaluating D3.3.4 – nominal strength, design strength, design strength with additional seismic reduction factors?
In lieu of meeting the ductile anchor requirement of D3.3.4, ACI318-08 has other options. Section D3.3.5 allows the design force to be limited by a ductile yielding attachment. Alternately, section D3.3.6 allows for a brittle anchor design provided you take a large reduction in design strength of the anchor.
ACI 318-11 has revised the ductility requirements to clarify that you compare the nominal strength of the concrete and anchor.
ACI 318-11 Section D.3.3.4.3 also considers four options for determining the required anchor or attachment strength to protect against brittle concrete failure. The first option requires the nominal concrete-governed strength to be 20% greater than the nominal steel strength, or: 1.2 x Nsa < Ncb. The second and third options require the anchor to be designed for the maximum load that can be delivered to the anchor. The fourth option is to design the anchor for E x Ω0 design loads. (It should be noted that the 2012 IBC modifies ACI 318-11 to delete these revisions and essentially reverts back to ACI 318-08.)
What are your thoughts? Visit the blog and leave a comment!
Before the adoption of ACI 318-08, we used through bolt with plate washer to address the high uplift demand of ATS. Since ACI 318-08 explicitly allows using reinforcement developed on 4 sides of the concrete breakout frustum as the design strength instead of determiniing the concrete breakout strength per Appendix D, we use stirrups, anchored to 4 additional longitudinal bars in both directions of the ATS rods to absorb the heavy uplift. For pulluot plate washer is designed to address the uplift. For side-face blowout the anchor is located at a minimum of 0.4 hef from any concrete edge. We haven’t revised our design per ACI 318-11 because it is not officially adopted yet.
Using stirrups creates some challenges in the heavily reinforced area of a podium slab; the spacing and locations of the stirrups may need to be adjusted to allow for slab top and bottom reinforcement installation.
We have been thinking of using a combination of threaded rod with coupler to threaded hooked rebars for anchorage since rebars does not need to comform to Appendix D and still be able to develop some significant strength within the limiting depth of podium slab.
Thanks for your feedback Freeman. Reinforcing the breakout can be an effective method of increasing the breakout capacity for situations where deeper embedment is not possible. Shear ties can also be difficult to install in congested areas, as I’m sure the ironworkers won’t be shy about telling us.
Threaded rebar for anchorage is not covered in Appendix D or ACI 318, so a solution utilizing threaded or coupling onto rebar for anchorage should be evaluated to an approved design standard, or tested to an approved criteria such as ICC-ES AC399 – “Acceptance Criteria For Cast-In-Place Proprietary Bolts In Concrete For Light-Frame Construction.” In our testing experience, we’ve found that once you eliminate failures like pullout and side face blowout, you get a breakout cone that more or less resembles the cone you calculate per Appendix D.
The threaded rebar that I mentioned is only threaded at the top to engage the coupler from the threaded rod. The coupler can be just a standard coupler, and the portion embedded inside the concrete is basically a regular rebar with a standard hook developed per Chapter 12 of ACI. I don’t think rebar with a standard hook still needed to be tested, correctly me if I am wrong.
A hooked rebar with development length per Chapter 12 would still need to consider a concrete breakout calculation similar to an anchor bolt or threaded rod with plate washer. Since Chapter 12 and Appendix D do not address how to determine h(effective) for doing a breakout calculation with deformed rebar as the anchor, testing should be used to evaluate this type of configuration.
Failure of hooked bars are the splitting of the concrete cover in the plane of the hook rather than concrete breakout of the cone. The primary cause of failure and splitting originates at the inside of the hook. Testing of hooked bars had been done in the 70s and documented in ACI. As long as there is enough cover and enough development length, then hooked bar can develop its strength per ACI Chapter 12. The behavior of embedded anchors addressed by ACI App D is different from the behavior that of reinforcement per Chapter 12 of ACI.
Has anyone else experienced this problem…? I have a piece of mechanical equipment that I am anchoring to concrete. I designed it to the ACI 318-08, but due to other reasons it was not submitted in time. I now have to re-do the calc to the ACI 318-11. The tension forces I have to design for are about twice as large, however now the anchor that I had originally selected is way over stressed. Why do I need to double my embedment depth to meet this new code? I am using the overstrength factor because like all 99% of equipment, there is not nearly enough information to figure out the yield force of the attachment. I have pieces of equipment that no anchor will work based on the hole size in the equipment.
I agree. Not only are the forces going up but the ductile requirement is back. I used to rely on an exemption in the 2010 CBC for the ductile mode required for structural situations. That exemption appears to be missing from the 2013 CBC. I guess I’ll just have to anchor 500 lb transformers with 1″ diameter bolts with 15 inches of embedment.
2010 CBC allowed for a 1.3 increase in the anchorage force to not have to use the 0.4 reduction for non-ductile failure modes in ACI11-08 section D3.3.6. The 2013 CBC code no longer has this exemption and now, per ACI 318-11, the anchor seismic force has to be multiplied by an omega value from ASCE 7-10. The majority of the time omega = 2.5 so anchor forces have increased by 92% (2.5/1.3), You would think the omega forces for equipment anchorages would be have been more in line with the 1.3 factor from the 2010 exception.