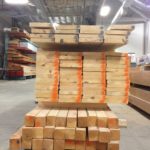
Like many people with desk jobs, I just have to get up and walk around every once in a while. Most of my walks are through our connector test lab at our home office in Pleasanton, California. The lab technicians install a lot of products for testing, so in addition to stretching my legs, I like to quiz them for ideas on things we can do to make installation faster and easier for our products.
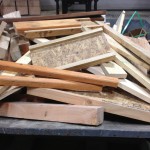
During one of my walks this week, a lab technician was finishing up a rather extensive test setup that consumed a large quantity of lumber, screws, and truss plates. I asked him how it was going and he commented, “Testing isn’t exactly environmentally friendly, is it?”
Before I could even respond, he added, “I guess that’s just part of the price of building safer buildings.” I like the way he thinks.
I know we produce a lot of wood waste every day in our connector test lab, but having this conversation made me curious to put some numbers to it. So I did a little research to roughly estimate how much lumber and what sizes we used in test setups for a year. 4×12 headers seem to be the size that works for so many joist hanger tests, so my hunch was that size would be the winner.
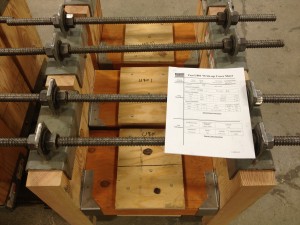
Lumber Usage:
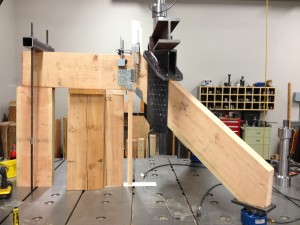
But my hunch was wrong! Close, but going by lineal feet, the humble 2×4 leads the pack. Board feet is more meaningful, since it captures the volume, so by that measure the 4×4 is the winner. While it is true that we use more 4×12 than any other size material for joist hanger tests, we use many 4×4’s as the main member in the testing of proprietary screws and nails, such as the Strong-Drive® SDS, SDW, SDWS and SDWH.
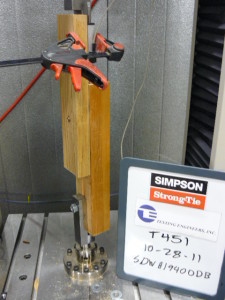
Adding everything up, we are consuming about 15,700 board-feet of lumber in our test setups. A small cost when weighed against the value of safe, strong structures!
– Paul
What are your thoughts? Visit the blog and leave a comment!
How much different is getting something approved by calculations vs. getting something approved by testing?
Most connectors require testing. IBC Section 1716.1 Test standards for joist hangers and connectors details out the requirements to run a minimum of three tests, a safety factor of 3, and the 1/8″ deflection limit, plus calculations. Straight straps are an exception that are calculated only.
There is not much difference in what we would submit for a product approval. For a calculated only product, we would submit calculations, production drawings, and quality control documentation. For a tested product, we would submit all of that plus test reports.
Maybe you should have a few company wiener roasts.