When you hear $452 billion, what comes to mind? Perhaps the annual state budgets of California, Texas, Florida or New York? Maybe the combined net worth of Bill Gates, Larry Ellison, or the Walton Family? While those would be good guesses, I bet you didn’t think of corrosion! According to a May 2012 Congressional Briefing hosted by NACE International and ASM International, corrosion-related costs are a staggering 3.1% of the U.S. GDP, which is more than the individual budgets of those states above, and the combined net worth of the top 15 people listed on the Forbes 400: The Richest People in America.
Corrosion of metallic surfaces is an electrochemical process typically involving an anode, electrolyte and a cathode. An anode is a metal zone which loses electrons when exposed to an electrolyte, an electrolyte is a non-metal electrical conductor, and a cathode is the zone where an oxidizing agent (e.g., oxygen) gains the electrons. While there are many different forms of corrosion (e.g., pitting, intergranular, wet storage stain, etc.), and various sources of causes (e.g., treated lumber, moisture level, temperature, atmosphere, air quality, etc.), other factors such as exposure related to time of wetness are equally important. In a study presented in Dr. X.G. Zhang’s book Corrosion and Electrochemistry of Zinc, time of wetness is 50% greater near the top of a structure compared to the bottom, leading to greater corrosion.
Building products such as metal connectors and fasteners may suffer reduced area and lose load-carrying capacity as a direct result of corrosion (See Photos 2 and 3 below). Thus, it is important that the design professional consider the end use of such products and their environment during specification as certain measures can be taken to mitigate the problem. The 2009 and 2012 IBC® recognizes various exposure conditions and sources of corrosion in Section 2304.9.5 (e.g., preservative-treated wood, fire-retardant-treated wood, etc.) and prescribes protective metal coatings for corrosion-resistant material, such as stainless steel, in certain instances. In some cases, the building code states to follow the manufacturer’s recommendations, such as for metal connector coatings. Greater thicknesses of zinc along with stainless steel are just some ways to help reduce corrosion depending on the application. Figures 1 and 2 below illustrate recommendations from Simpson Strong-Tie.
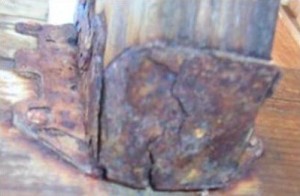
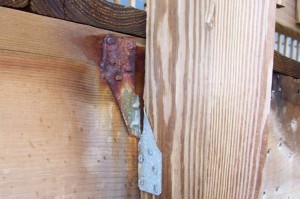
There are many other technical resources available on the topic such as the American Galvanizers Association, which has a series of articles titled Ask Dr. Galv, and the International Zinc Association. Simpson Strong-Tie also has numerous documents and research papers.
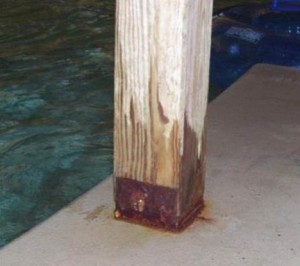
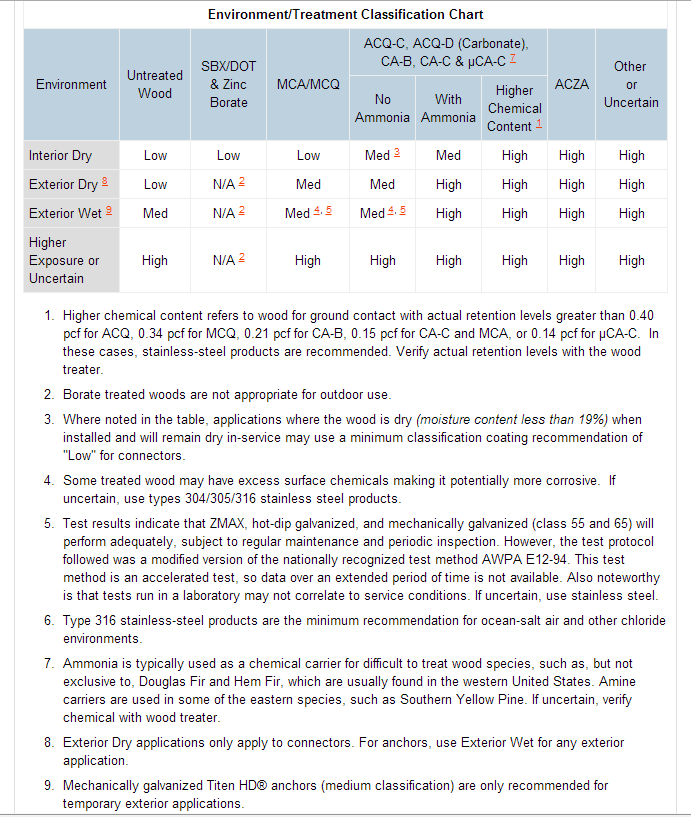

Is corrosion something a structural engineer should address in specifying materials for construction, or do you leave the selection of materials or coatings up to the architect, the contractor, or the end user? Let us know by posting a Comment.
– Paul
What are your thoughts? Visit the blog and leave a comment!
Thanks for this post! I have friend looking to resolve some building errors and browsing firms who do this type of engineering in Toronto. I know that we would like to see this link. How much time does an average home have before you have to start worrying about corrosion issues (homes built before 2001)