Lumber size is often given in “nominal” measurements. This can often lead to confusion when someone is shopping for wood and wood connectors. Paul McEntee, Simpson Strong-Tie Manager of Engineering R&D, addressed lumber sizes and how our company takes them into consideration during product development and testing.
Your wood fastening products seem to be built for yesteryear wood sizes. 2x’s are no longer larger than 1½”. Why can’t you manufacture these products with a little closer tolerance?
I received this question from a customer a few days ago via Ask Simpson, a web page where you can submit technical questions to our Engineering Department and we respond by e-mail. We have received similar variations of this question countless times over the years, so I thought it could use some discussion.
The National Design Specification for Wood Construction (NDS) Supplement Table 1A “Nominal and Minimum Dressed Sizes of Sawn Lumber” gives the minimum dry and green dimensions for sawn lumber. This specifies a nominal 2x, for example, as being 1½” dry and 1 9/16” green. NDS Supplement Section 3.1.1 defines dry lumber being seasoned to a moisture content of 19% or less, whereas green lumber is higher than 19%.
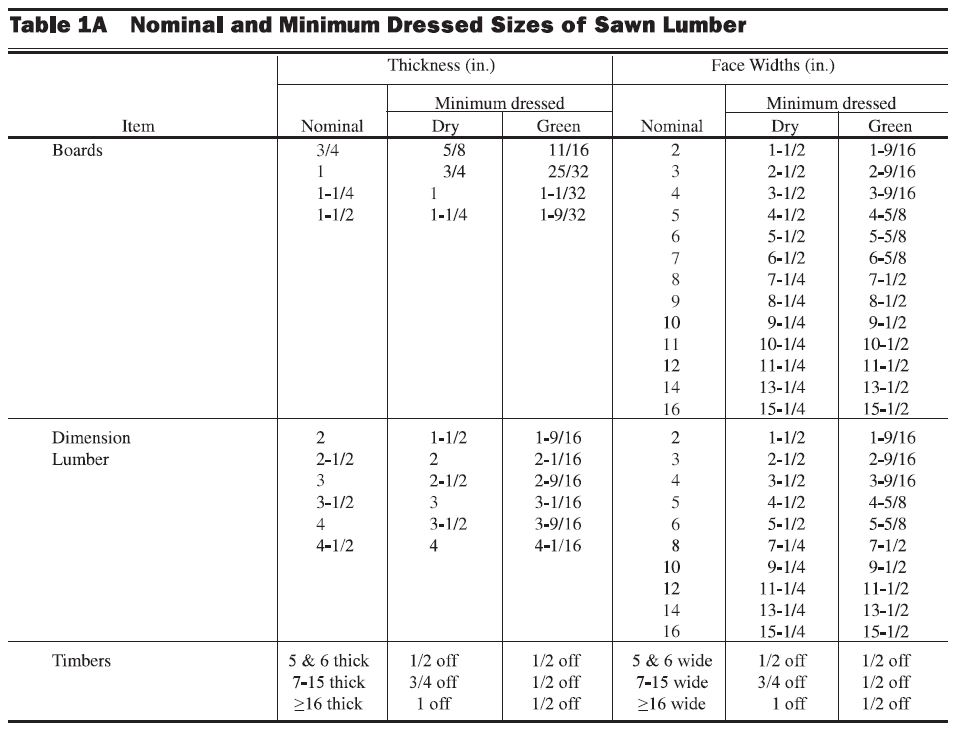
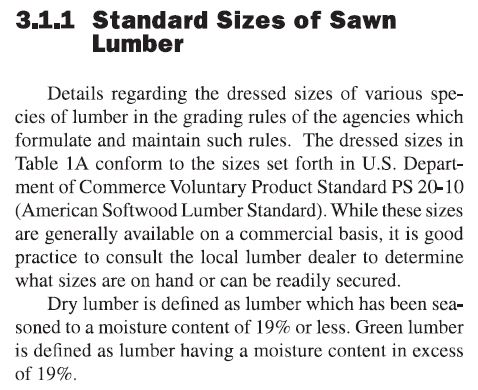
So what size do you make the connector?
This is a real challenge as lumber dimensions vary based on moisture content, which has both regional and seasonal variations. For standard connectors, we target our widths to be 1/16” larger than the NDS dry dimensions. This means that 2x connectors are typically targeting a 1 9/16” width – green lumber will be a real tight fit, and dry lumber will be 1/16” thinner than the connector, so it slides in easy. Much like construction, manufacturing needs tolerances, so the hanger could also be up to 1/16” wider than our target width, resulting in a 1/8” difference. This does not result in a reduced load capacity for the hanger and should not be cause for concern.
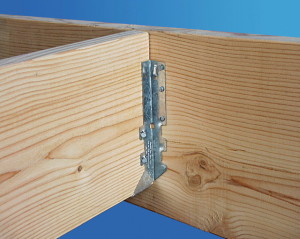
Dry lumber can get much lower than 19% moisture content, resulting in a 2x being less than even 1½” thick. Rather than look up a research paper on the subject, I walked through the test lab today measuring 2x’s with calipers to see what kind of range I would see. In addition to getting some confused looks from the lab techs, I learned that the wood in our conditioning room was almost exactly 1½”. This makes sense since we control the humidity and temperature in that room, so the wood cannot dry. A few other 2x4s that had been outside on the lab floor for at least a year were dry (and warped!) and, not surprisingly, a little thinner than 1½”.
Engineered wood products, such as laminated veneer lumber (LVL) or I-joists are less susceptible to dimensional variations due to drying and shrinkage. There will still be dimensional variations in engineered wood. While measuring my 2x’s, I also checked out two brands of 1¾” LVL we had on the shelves. One manufacturer’s was 1.70” thick, and the other was 1.80” – and no, I didn’t look to see what the brands were.
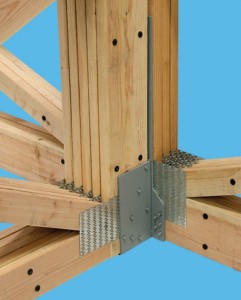
Connector widths for most single-ply sawn lumber follow the same guideline of being 1/16” wider than the NDS dry width. Selecting a width for built-up members is more challenging. The variations in wood thickness accumulate over the multiple plies for solid sawn or engineered wood. Plated trusses also have truss plates, which add to the thickness of the finished assembly. For these we have to draw on many years of experience and feedback from our customers.
– Paul
What are your thoughts? Visit the blog and leave a comment!
If you’ve been dismayed, over the years, by the steady shrinkage in actual (but not nominal) conventional (Federally graded) dimension lumber sizes, and if you work in (the more rural) parts of the country where full-dimension rough-sawn –hemlock or poplar– is still available, you might re-considering not using it. To keep this comment short I won’t go into the legal-fiscal difficulties, but they can be overcome if you are so determined.
Thank you for providing such wonderful value with your amazing blog!