“One test result is worth one thousand expert opinions.”
– Wernher von Braun
While reviewing some of our first catalogs, I was curious about the testing we did on those iconic products that launched our company. I found a test report from December 20, 1957 on crinkled yellow paper with a short description: U-29 Download Test. The signature from the independent testing agency was a little faded, and the data was typed by hand in a table. But I was thrilled to discover that our 1957 customers received exactly the same thing as our modern-day customers – the confidence in knowing that our allowable loads are supported by physical testing.
There simply is no substitute for a physical test.
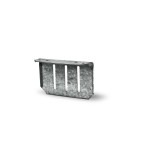
For example, when we recently developed our line of products for use with curtain-wall steel-stud framing, we started product development just as we did in 1957 – not with expert opinions, just a test.
The first few tests were basic bent pieces of metal to isolate critical design features and characteristic performance of the part.
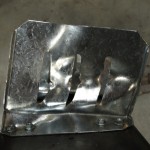
We then did dozens of iterations of physical testing plus scores of simulations using finite element analysis to refine the parts. We varied the rolled edges and embossments, tried different fasteners and adjusted fastener locations until we achieved the best load at the lowest installed cost. After all of that, we tested the final products one more time for the code report.
How important is product testing to you? Let us know by posting a comment.
– Paul
What are your thoughts? Visit the blog and leave a comment!
I love test data. The theoretical models are only as good as the input and deserve a reasonable factor of safety. Test data can be analyzed and demonstrate through actual use how an item should perform. This can generally allow a lower factor of safety since there is less risk than the theoretical model. The lower factor of safety results in less material used and potentially less cost. Both benefits to a client.
Good points on increased certainty. Some test standards that are utilized in product evaluations allow for a lower safety factor in the load rating if your run more tests and/or there is low variation in the test data. Other standards just have a default safety factor of 3 (or whatever).
Theoretical models have their place. We use them extensively to refine products in development, because it is quick and inexpensive to manipulate a part in a computer model. But the final load rating is always a physical test.
there is no substitute for test data. We all want to see how the product performs under real conditions.
Over the next few months I am planning a series of posts about the nuts and bolts of how we test in our labs. Your words “under real conditions” remind me that I should include a discussion of modeling proper boundary conditions in tests. Some tests are simple, but for others it can be challenging to match field conditions in the lab.
Yes, test data is very important and should always be done. Proper installation is the other side of the equation which is where structural observation and City inspections come in.
Good point. Test data isn’t that useful if the installation is incorrect.