Simpson Strong-Tie and Structural Technologies formed a strategic alliance for Composite Strengthening Systems™ (CSS) products in 2021. CSS products include fiber-reinforced polymer (FRP) and fabric-reinforced cementitious matrix (FRCM) strengthening systems. Additionally, where CSS products are not a viable solution, the alliance can also offer recommendations and design for other non-CSS or conventional strengthening solutions. This alliance allows each firm to specialize in their areas of expertise:
- Simpson Strong-Tie engineers and manufactures structural products, conducts rigorous lab testing, and provides technical support through our extensive field engineer network
- Structural Technologies provides design support, technical services, and a network of licensed installers
The result is both firms working together to provide high-quality solutions to our customers. Together, we’re able to respond quickly with a level of service unmatched in the industry. A recent example of this occurred when a project required FRP strengthening of lightweight concrete (LWC) slabs.
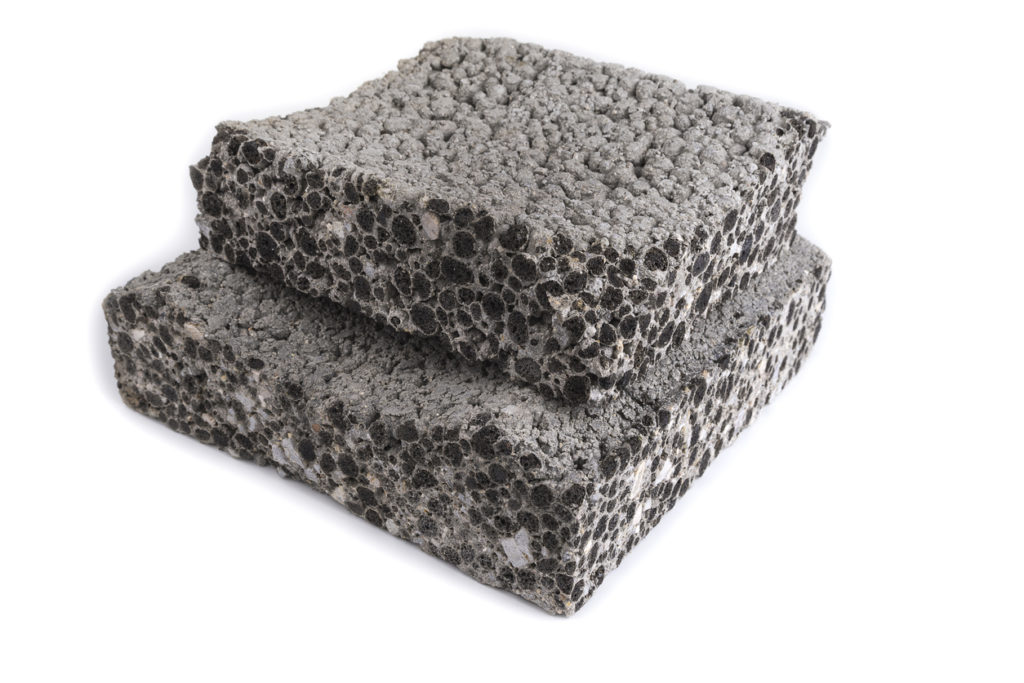
ACI 440.2R Section 1.2-Scope states that “The design equations given in this document are the result of research primarily conducted on … members fabricated of normal-weight concrete.” Because most research of FRP strengthened members has been on normal-weight concrete (NWC), “Caution should be given to applications involving strengthening of … lightweight concrete members.”
LWC is commonly used for elevated slabs to decrease the dead load of multilevel structures. Many of these slabs act as diaphragms to resist seismic forces in seismically active regions. LWC diaphragms in older structures are frequently deficient in shear and/or flexure. We have been asked about LWC FRP strengthening, including the application of FRP fabric and FRP anchors, frequently over the years.
As a result of our customers’ questions, we developed an in-house test program at our Tye Gilb Research Lab in Stockton, CA. The lab is accredited by IAS for ICC-ES AC125 and IAPMO EC038 FRP testing. Since 2020, Simpson Strong-Tie has been conducting multiple large test programs on concrete diaphragms strengthened with FRP composite systems.
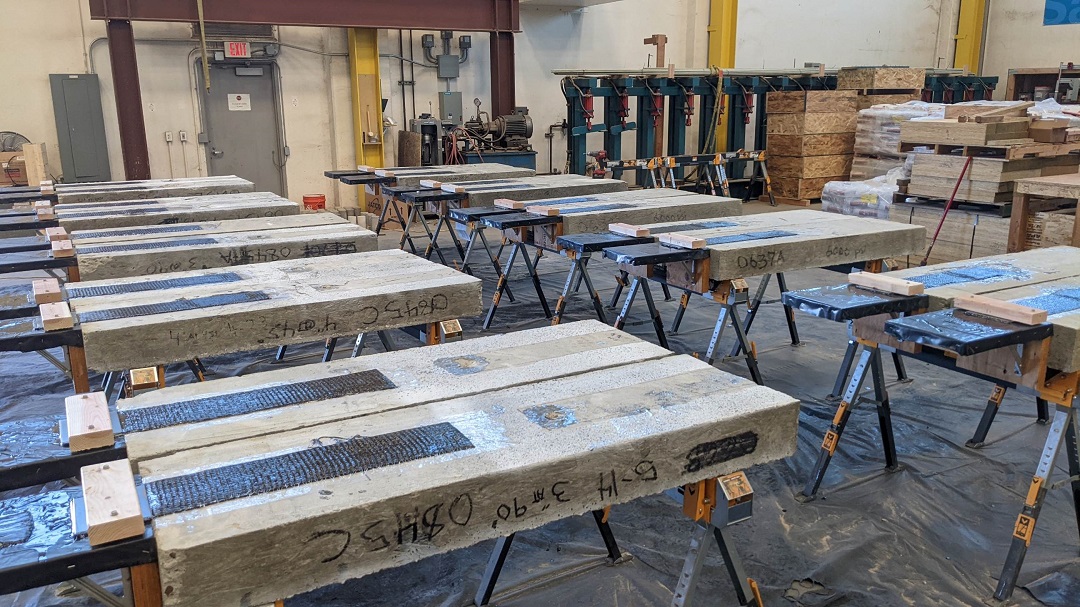
We’ve tested more than 200 diaphragm specimens to determine the effect of concrete strength, fiber stiffness and thickness, anchoring schemes, and other parameters. For this test program, we conducted single lap shear tests on FRP-strengthened LWC blocks to evaluate the bond of anchored and unanchored FRP fabrics to the LWC.
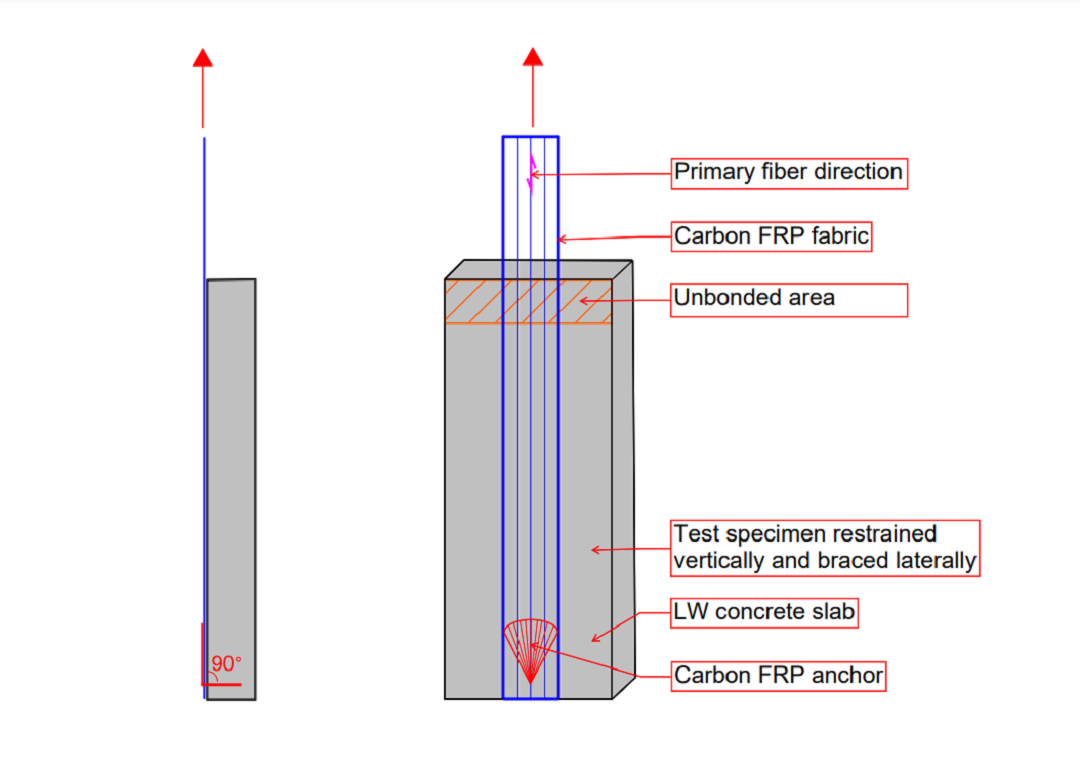
Some specimens were detailed with an FRP fabric strip only, while others included FRP anchors. FRP fabric strips are saturated with epoxy saturant using a wet layup process, then bonded to the prepared LWC surface. The FRP anchor is bonded to the FRP strip and concrete slab using epoxy saturant. The embedded portion of the anchor is bonded to the hole in the concrete in much the same way as metallic adhesive anchors. The fibers of the anchor fan are spread and bonded to the FRP strip.
The FRP strips are loaded in tension, so the top of the bonded FRP simulates the a concrete crack in a diaphragm. As the load increases, the tension in the FRP is transferred through the epoxy saturant to the LWC substrate. At a certain point, the LWC bonded to the FRP strip will exhibit a cohesive shear bond failure, also known as a debonding failure. This is the most common failure mode for externally bonded FRP. The debonding strain for normal-weight concrete can be calculated using equations in ACI 440.2R.
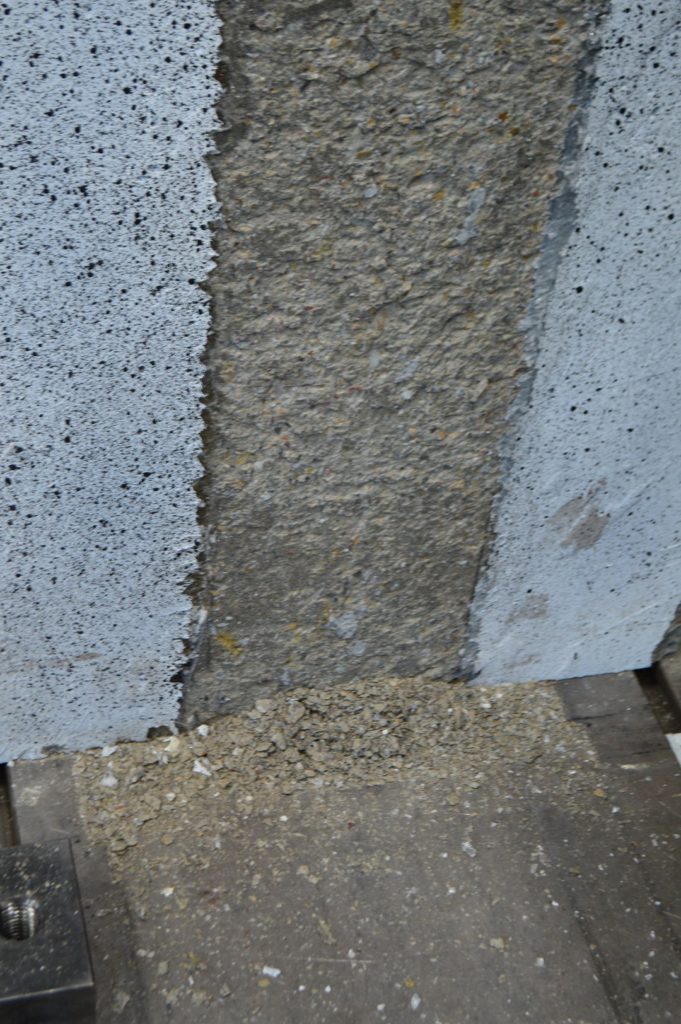
For an unanchored FRP strip, this is the end of the test. When FRP anchors are used, the FRP strip can continue to carry more load even after debonding from the surface of the concrete. The tension in the FRP strip is transferred to the FRP anchor, which is bonded to the LWC anchor hole. The load continues to increase until the FRP anchor fails. The FRP anchor can exhibit several different failure modes, including concrete breakout, concrete crushing adjacent to the anchor, and rupture of the FRP anchor.
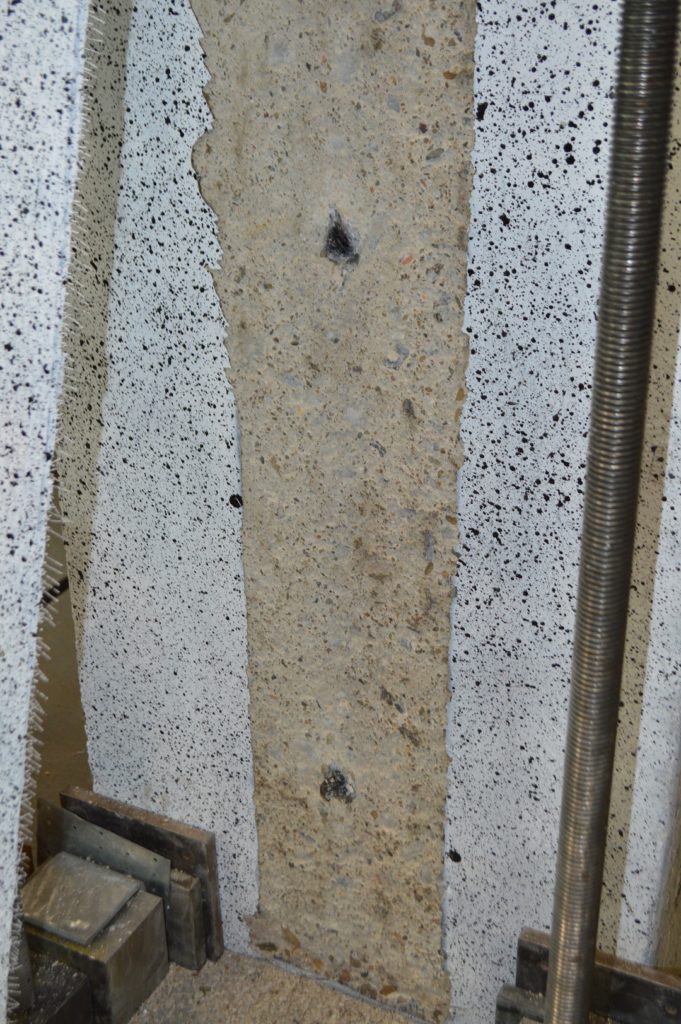
We are collaborating with the Structural Technologies design team so they can use the results of our testing to properly design LWC strengthening solutions for a project currently in the design phase. Structural Technologies has decades of experience in designing FRP strengthening solutions, including interpreting test data to support project design. Additionally, their close relationship to their installer network allows them to design solutions that are cost effective to install.
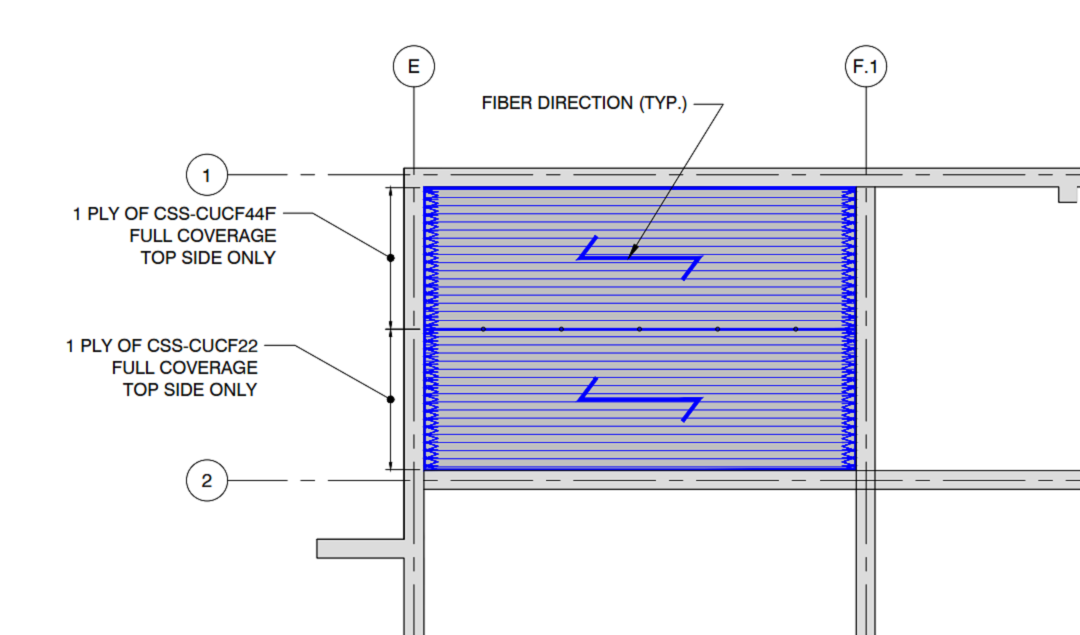
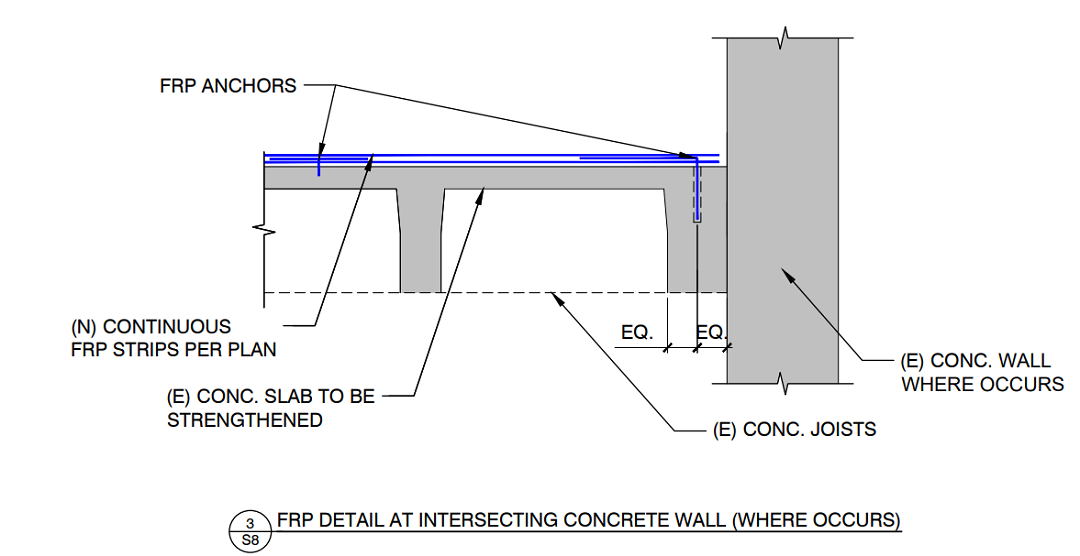
By working together, Structural Technologies and Simpson Strong-Tie teams are able to develop, test, design, support, and install FRP strengthening systems to better serve our customers.
References: