Last fall we hosted a two-part webinar series on the latest innovations in designing cladding connections for structural buildings. The first webinar, covered some of the biggest challenges that fabricators, engineers, and contractors in the structural steel industry face when designing façade attachments to a building structure. We discussed new design methods and solutions, such as bolted connections that do not require any field-welding to help enclose buildings quickly and reduce overall project schedules and costs.
One solution these webinars highlighted was the Edge-Tie™ system, which is designed to replace field-welded bent plate pour stops with a high-strength, straight-edge, channeled steel beam that accepts bolted connections to facilitate easy cladding installations without the need for welding.
The Edge-Tie system replaces traditional bent plates with an extruded steel beam of higher strength that is more dimensionally reliable while enabling a bolted cladding connection. JEI Structural Engineering President Stewart Jeske is the inventor of this structural steel solution. In advance of our first webinar, he provides background on why this solution was necessary.
For a cladding engineer, one of the most important, but most complicated connection designs is the attachment of façade systems, such as curtain walls, to the building structure. This is because the connection has many load cases that come with many challenges associated with stand-off distance from the building, construction tolerances, building structural movement, and adjustability for field installation.
Ten years ago, we asked our clients a simple question, “If you could change one thing about your job in the field when constructing curtain walls, what would it be?” Responses were virtually unanimous with “Eliminate all edge-of-slab field welding.” It is industry standard for a curtain wall or other type of cladding connection to be field welded to the bent plate pour stop. Yet we received many responses regarding the limitations of this design.
I began to ask myself, “Is there a way to make this connection different?” then it hit me. What if we redesigned the bent-plate pour stop to include a built-in, adjustable, anchor system for bolted connections? I sketched many different concepts and reviewed each one for efficacy. Early in our design efforts, we created detailed models and conducted finite element analysis to justify and improve our concepts until the Edge-Tie™ system (ETS) was conceived.
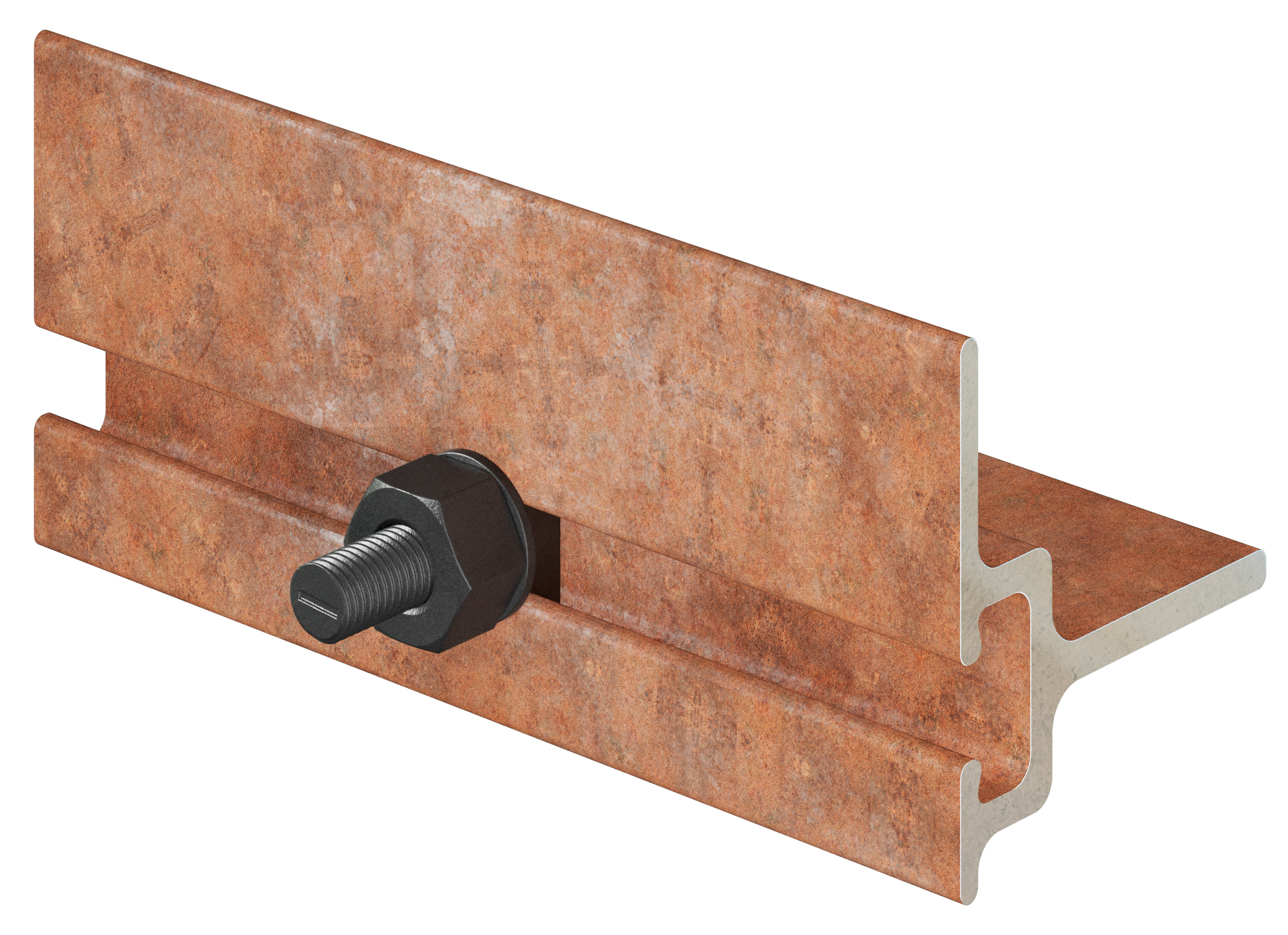
This new solution allows for simplified façade connections, while also providing the ability to create easy-to-install and reusable safety railings that can remain in place while the cladding is installed. The Edge-Tie system guardrail can decrease the cladding installation time, reducing tie-off occurrences while still providing fall protection.
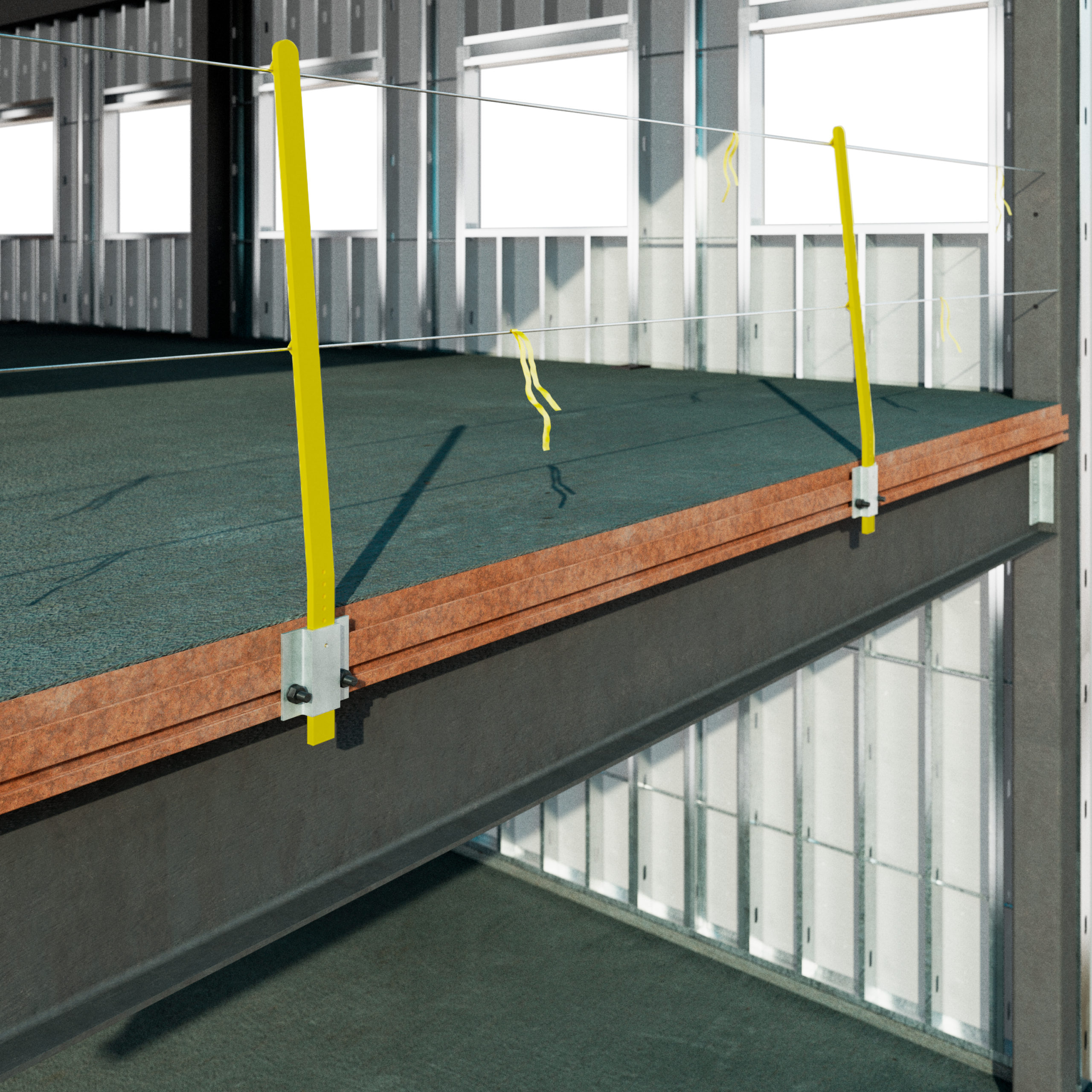
I remember the first project that specified the Edge-Tie system. We needed to demonstrate to the Engineer of Record that the Edge-Tie system was a better structural solution than the standard bent-plate pour stop that was detailed in the contract drawings. We put together a comprehensive set of calculations validating that the ETS had greater capacity than the pour stop that had been used in their standards for years. Our analysis showed that traditional pour stops could even become overstressed under the code design cladding loads. This can often be overlooked when idealizing these concentrated loads as uniformly distributed along the edge of slab. The Edge-Tie system proved stronger due to its higher-strength steel and more direct load path. The structural engineer thoroughly reviewed our analysis model and calculations, and they have since changed their standard details to include the Edge-Tie™ system.
Edge-Tie™ anchors for cladding are a stronger solution and are much easier for the contractors to use in the field. To learn more about how the Edge-Tie™ system brings adjustable, bolted cladding connections to steel construction, visit go.strongtie.com/edgetiesystem or call (800) 999-5099.