Strengthening of shear walls and diaphragm-to-wall connections has started on Little Tokyo Towers (see photo 1) located in downtown Los Angeles, CA. This senior–living residential facility was built in 1975. Structural analysis by Tuan and Robinson Structural Engineers showed that some modest strengthening was required to improve the building’s lateral system performance in the event of an earthquake.
Structural Preservation Systems, the fiber-reinforced polymer (FRP) applicator for this project, was tasked to work closely with MFRG-ICON, a GC with a strong reputation for affordable housing renovations. The challenge of this project was coming up with a plan that would allow for work to be carried out while being mindful of the occupants of the building.
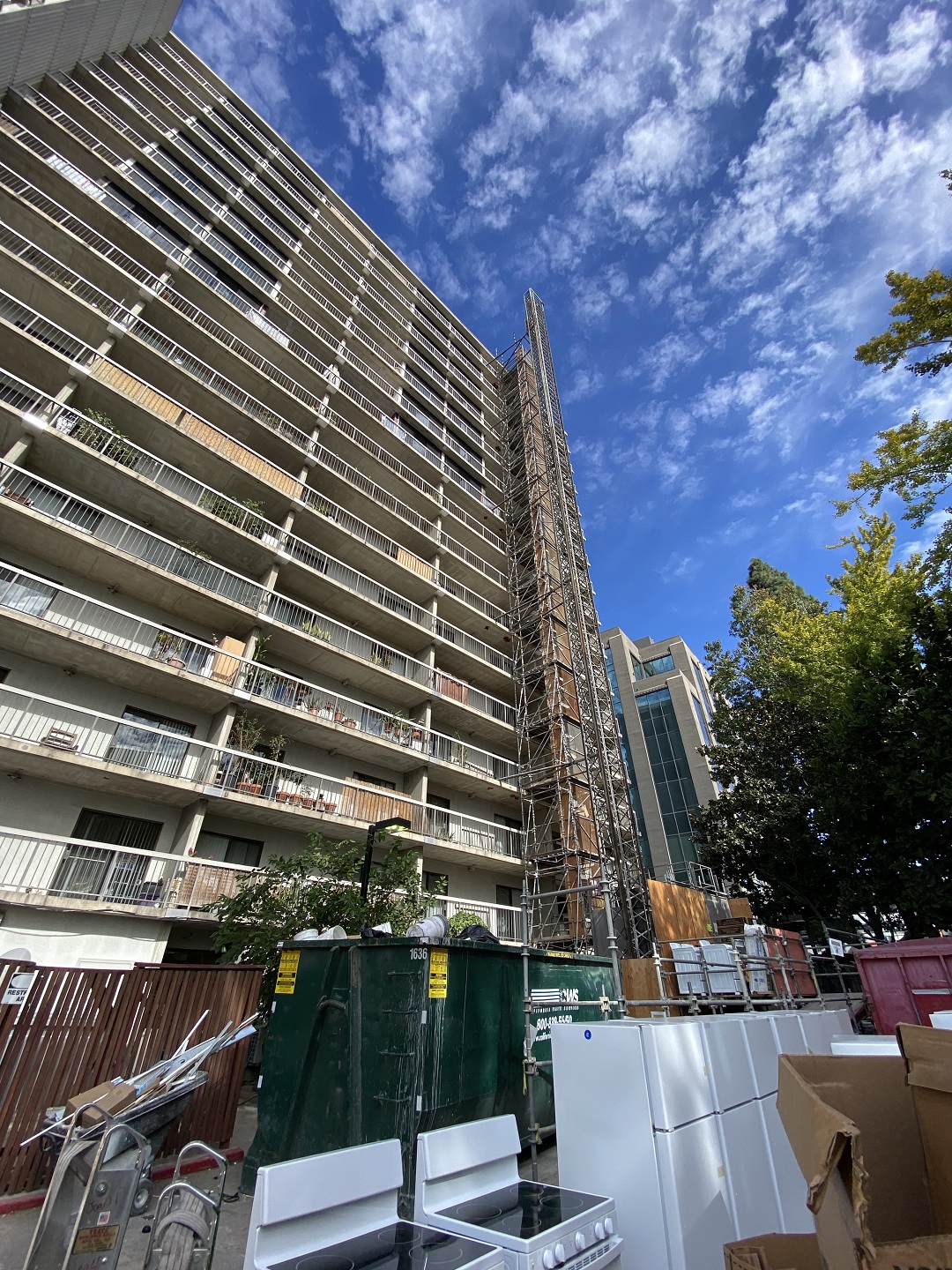
The first step to wall strengthening requires grinding of the surface to open up the pores of the concrete. As shown in photo 2, the next step is to saturate the concrete surface with epoxy resin. The pores allow the epoxy resin to soak in, similar to how a sponge absorbs water, and develop a very high bond strength. As shown in photo 3, the next step is to apply to the concrete surface fully saturated FRP using the same epoxy resin.
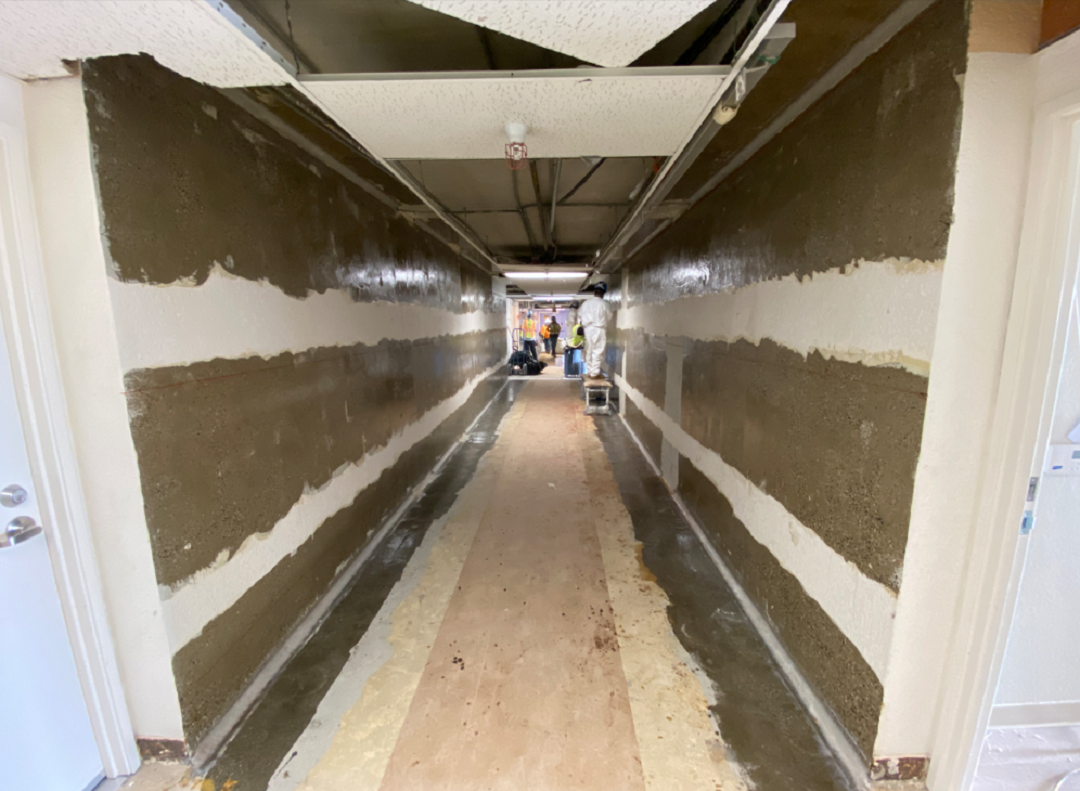
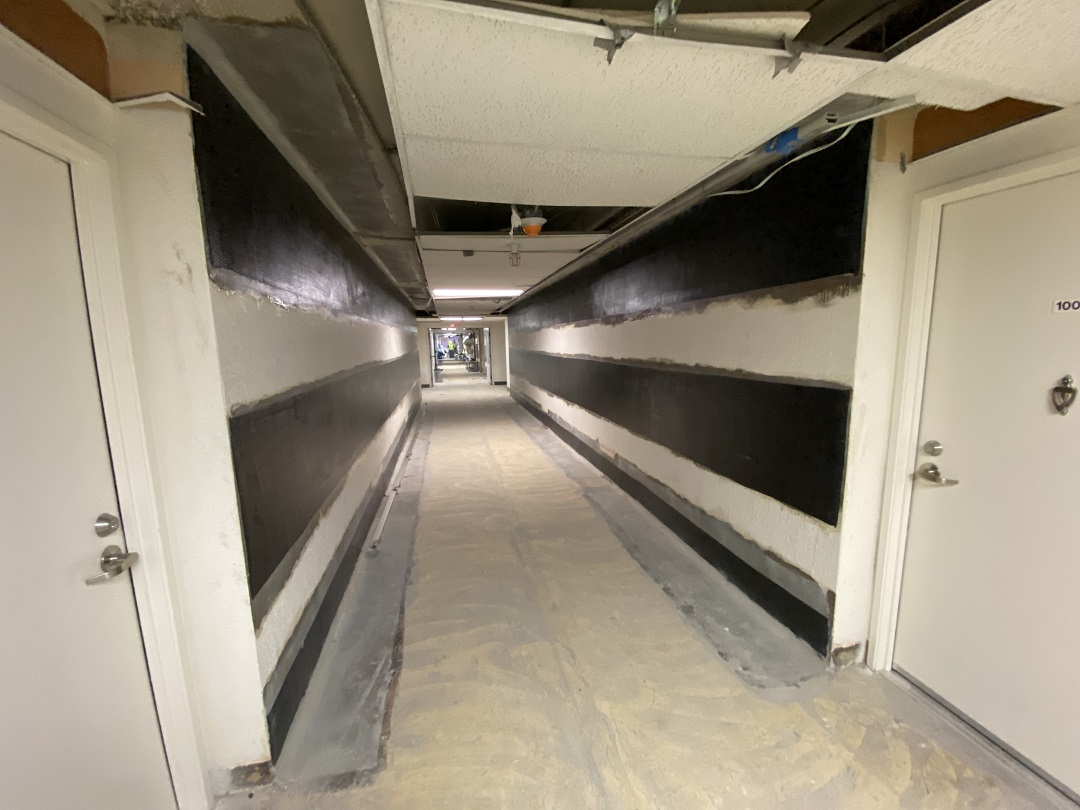
Photo 4 shows that bidirectional glass fabric was used to strengthen the diaphragm–to–wall connection. Notice the special detailing noted in the picture whereby thickened resin was used to create a 2″ radius at the junction of the wall and slab. This radius is required to reduce stresses in the FRP. Otherwise, leaving as a reentrant corner would result in a smaller shear strength increase. This solution results in a shear strength increase of about 10 kips per linear foot. Photo 5 shows installation of the glass FRP fabric. Photo 6 shows the same material installed overhead. Common on most, if not all, FRP projects is verifying that the bond strength between the FRP and concrete measures at least 200 psi. As shown in photo 7, field testing showed bond strengths to be on the order of 600 to 1,000 psi, far exceeding the 200 psi minimum required. Additionally, coupon tests are performed on the FRP material to verify that the material properties are adequate. Verifying the mechanical properties of the FRP and its bond to the concrete is a crucial part of the quality control process that helps to ensure that the FRP will function as designed.
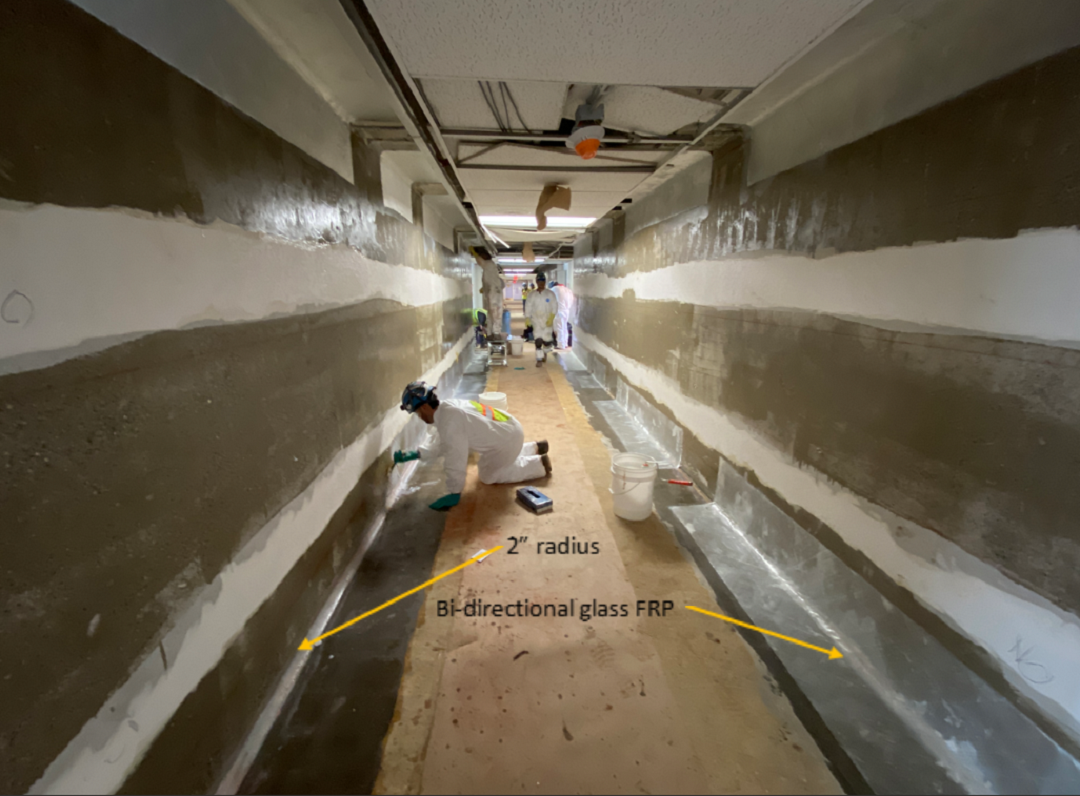
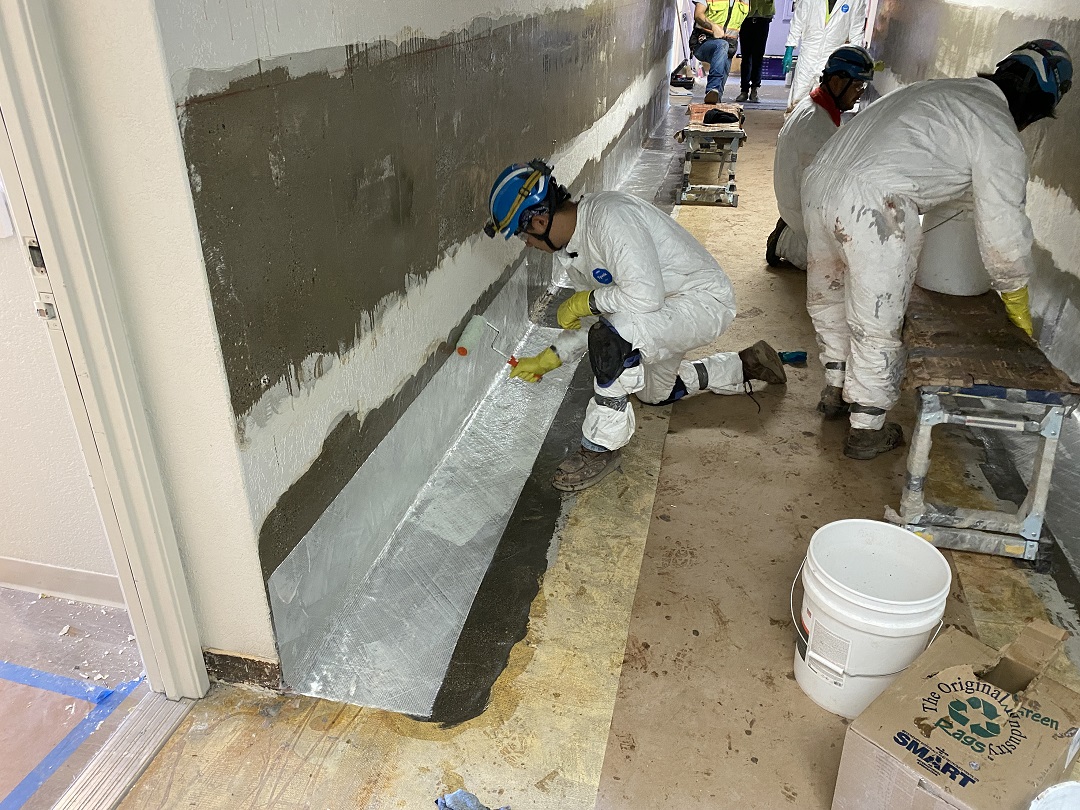
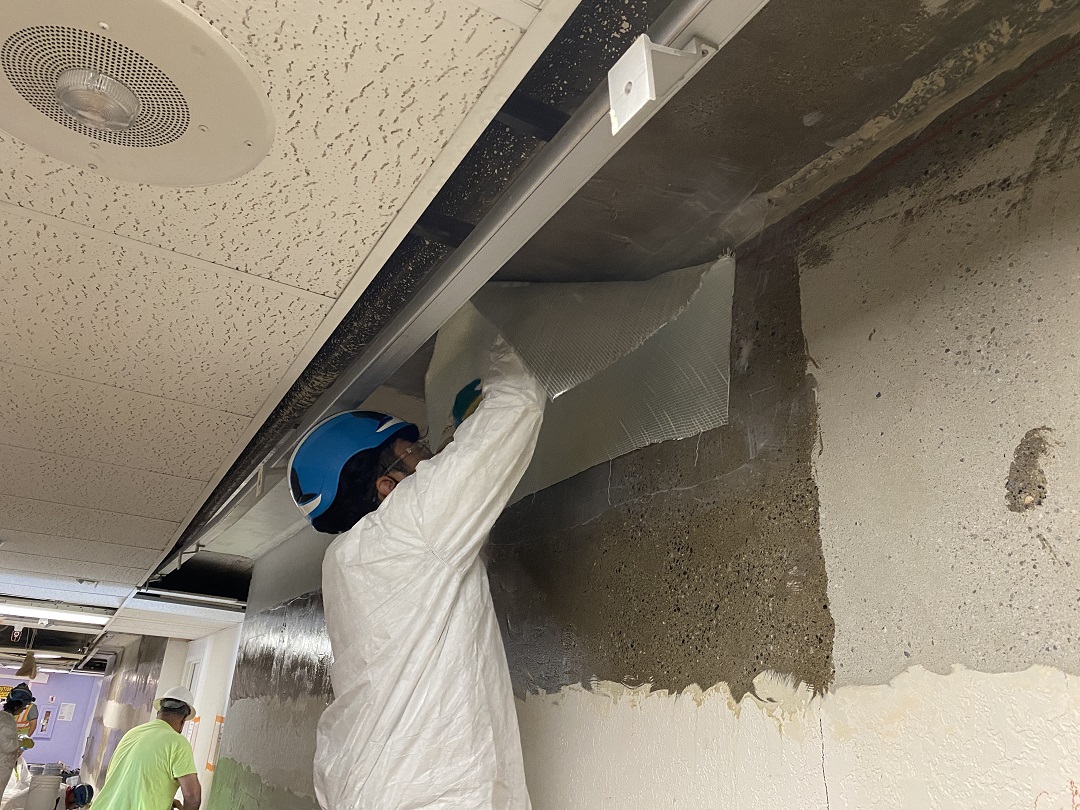
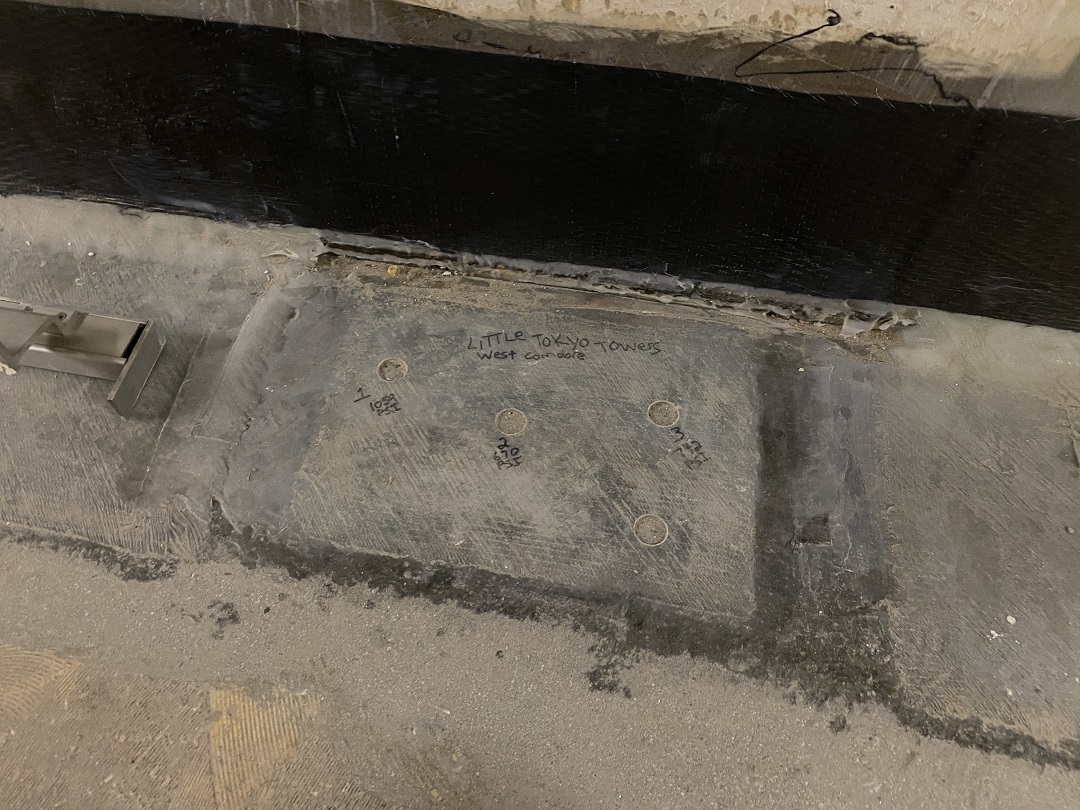
We look forward to sharing more FRP applications as this project continues well into the 2023 year!