In response to the increasing demand for mass timber construction, Simpson Strong-Tie has created mass timber solutions for these builds. These product addition, include our Heavy Seated Knife Plate (HSKP), ACBH concealed beam hanger, and CBH concealed beam hanger. Gain insights into the design, testing, and efficiency of the HSKP in achieving high loads with fewer fasteners. The blog underscores the structural mechanics and the ongoing process of pushing connector limits in mass timber construction.
More than 10 years ago, I wrote Do 50 Kip Wood Construction Connectors Exist, which discussed how we’d designed and tested some rather large glulam connections.
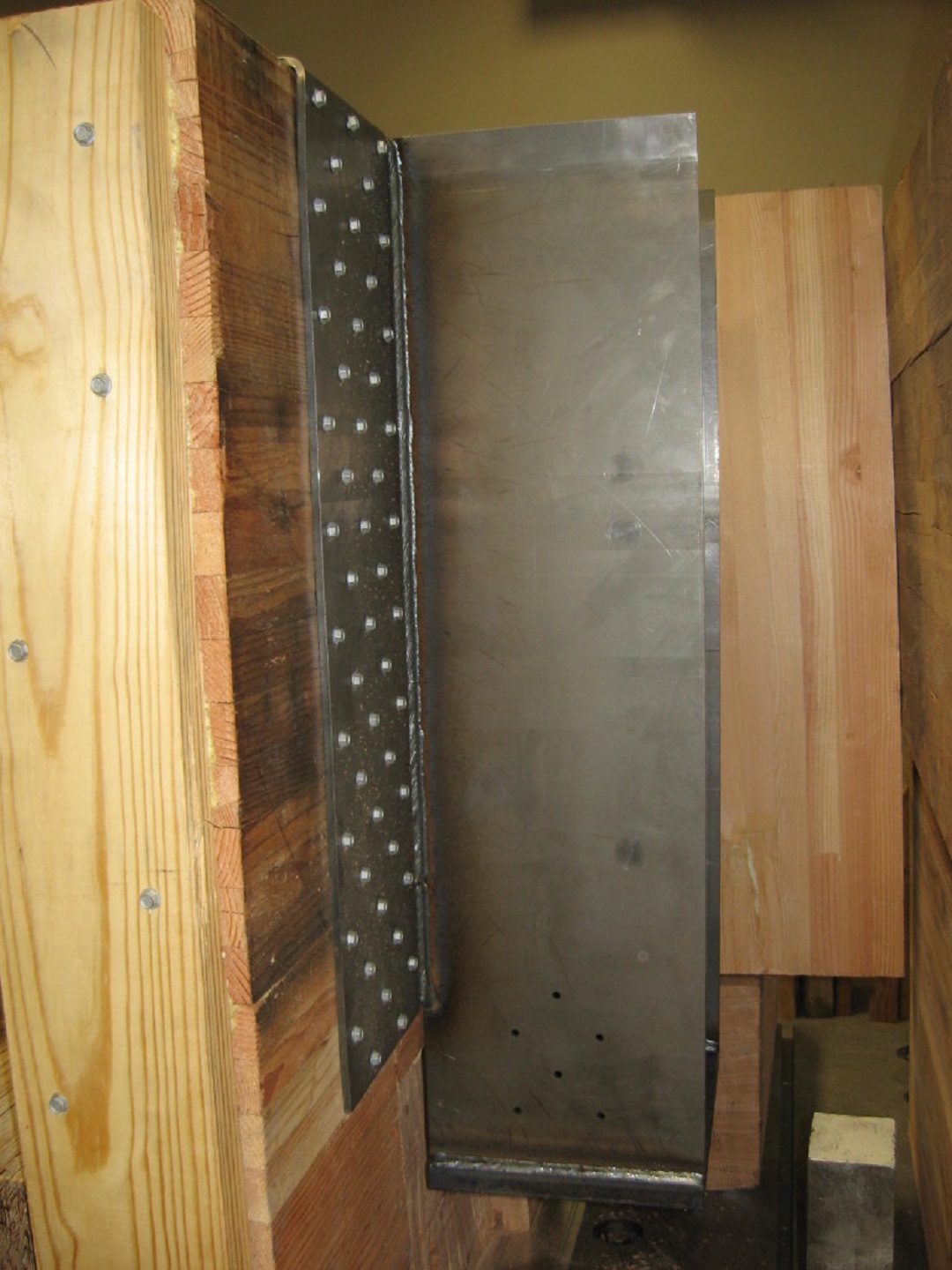

These were custom hangers that we developed and fabricated for some specific projects. The expansion of mass timber construction has increased the demand for high-capacity connections, with the additional need to conceal these connections for fire protection. The heavy seated knife plate (HSKP) is a convergence of several innovations to achieve high allowable loads with fewer fasteners than our CBH and ACBH™ concealed beam hangers. I’d like to take some time in this blog post to discuss the technologies employed in this exciting new hanger.
First up, angled fasteners.
I discussed the benefits of angled fasteners in this blog post about high-capacity straps for mass timber diaphragms. Using an angled fastener with a high withdrawal capacity results in a stronger, stiffer connection than perpendicular fasteners alone can achieve. We use angled Strong-Drive® SDCF Timber-CF screws in our ACBH concealed beam hanger to achieve higher loads than our CBH concealed beam hanger, which uses a similar number of perpendicular Strong-Drive SDS screws. In the comparison table below, our ACBH3x15.37 uses (48) SDCF fasteners and achieves roughly double the load of our CBH2.37×9.75 with a similar number (46) of SDS screws. Further down in the table, our smallest HSKP5.75/14.5 with (22) SDCF screws achieves an even higher load than the ACBH.
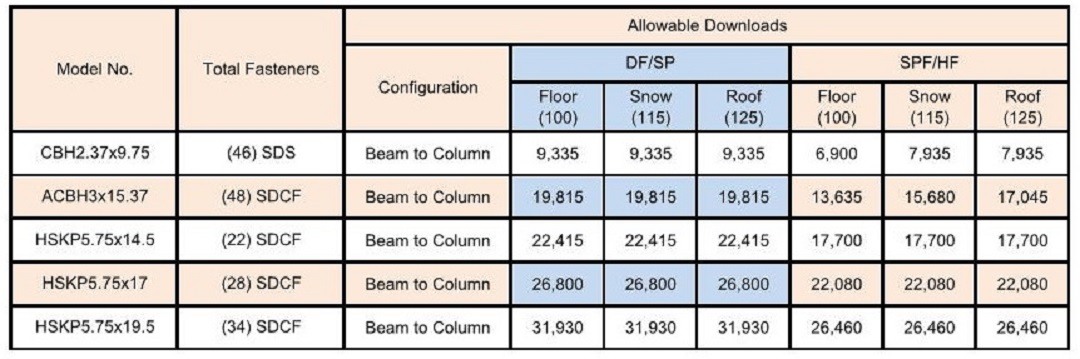
Both HSKP and ACBH are using angled fasteners, so why is the HSKP using less than half as many screws? The difference is the HSKP transfers vertical load from the beam to the hanger through bearing on the hanger seat, which eliminates most of the screws into the beam.
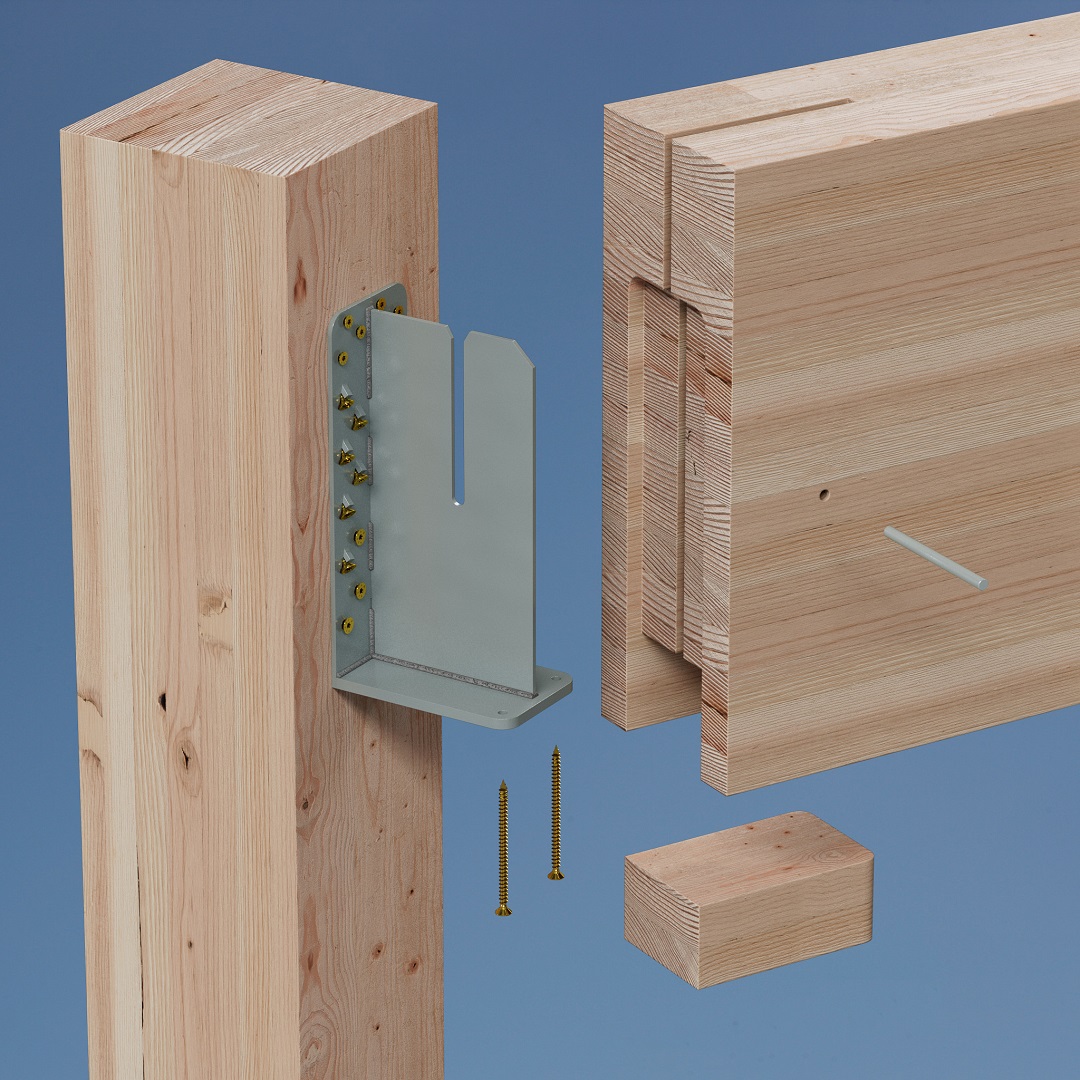
In addition to testing (How We Test) the HSKP, the building code also requires that we calculate that bearing stress in the hanger seat. To provide enough bearing strength without making the seat too large, we needed to increase the compression capacity of the wood. This brings up a second technology incorporated in the HSKP design —compression reinforcement.
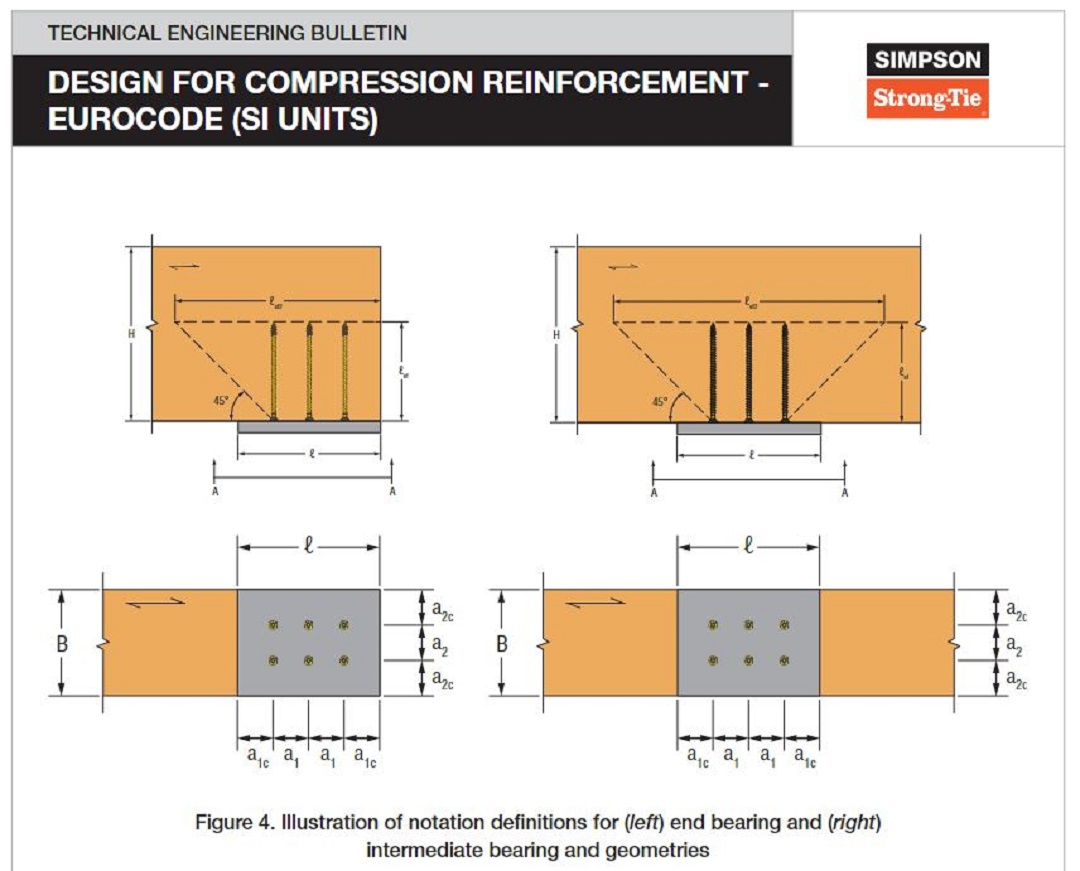
Our Technical Engineering Bulletin (TEB), SDCF Timber-CF as Compression Reinforcement, details a procedure for using SDCF screws to increase the perpendicular-to-grain bearing capacity of glue-laminated timber (glulam), cross-laminated timber (CLT) and heavy timbers. The design procedure presented in the TEB produces solutions that are consistent with NDS allowable stress perpendicular-to-grain requirements. The reference values used in the calculations are compression strength perpendicular (Fcp) from the NDS supplement and SDCF withdrawal values published in ESR-3046.
Designing compression reinforcement with SDCF screws models the screws as beam-columns on an elastic foundation. Compression forces transfer by bearing on the screws and the wood. The first two limit states involve compression strength of the wood plus the minimum of either screw buckling or screw embedment. The third limit state is compression resistance based on the effective bearing area formed at the points of the screws. A more detailed discussion of these limit states and the basis of the analysis is contained in the TEB.
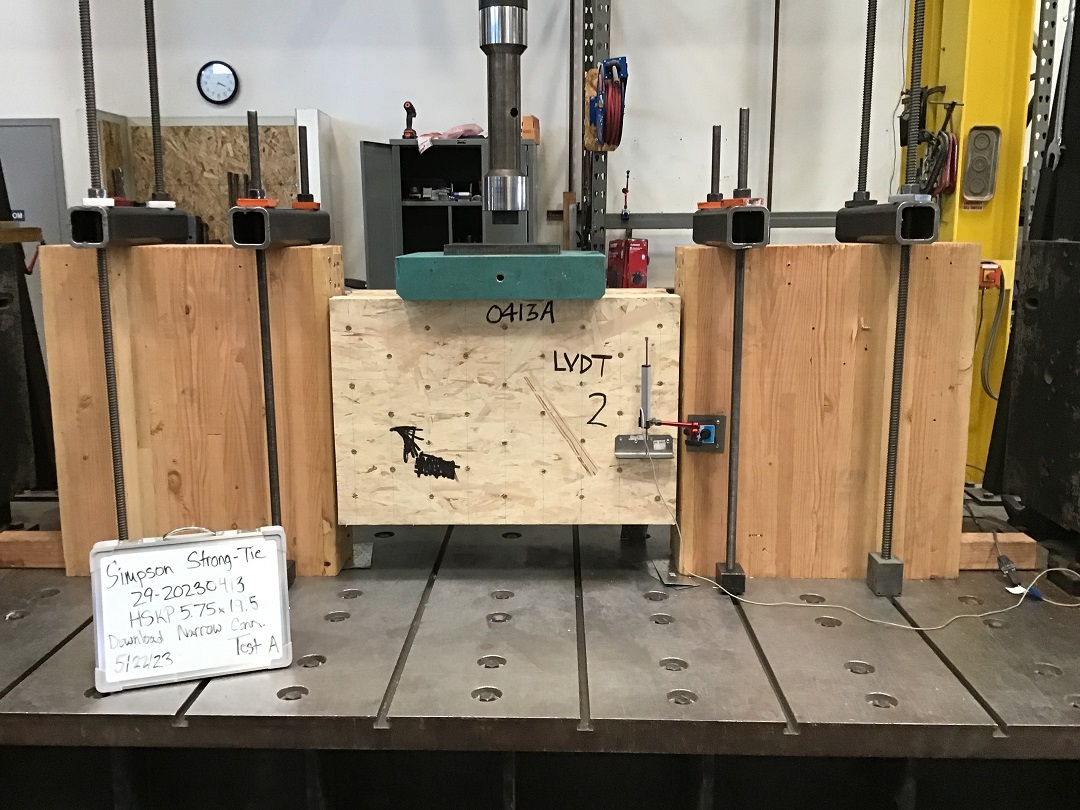
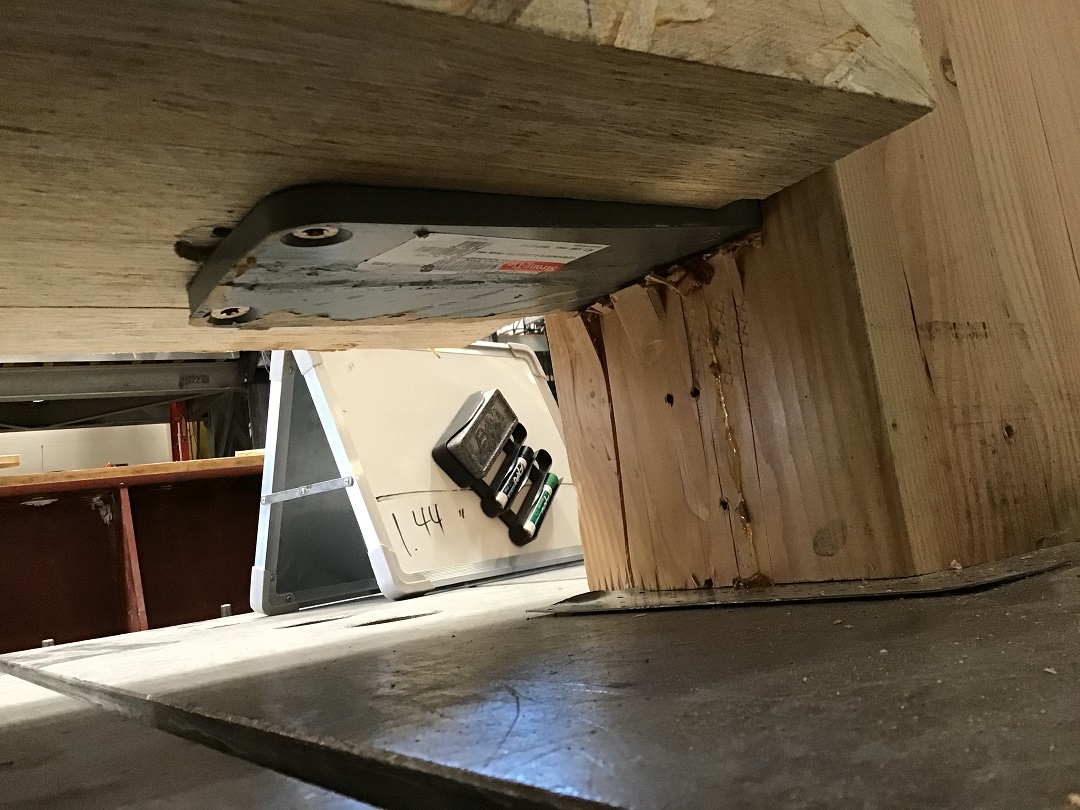
I’m excited about the HSKP as an innovative solution that creates a high-capacity connection for mass timber. The only thing I don’t like about this connector is that it is concealed, which makes the testing photos look like a bunch of wood. Testing these hangers is exciting, though. We don’t regularly see ultimate loads above 200 kips on a connector test setup.