When I had more hair and less of it was gray, I worked on a project as an assistant engineer doing the calculations for a mixed-use building in San Jose, California. Final design consisted of four stories of wood framing over a concrete podium slab and another level of below-grade parking. At that time, my firm had designed many two- and three-story residential buildings, but common thinking was you switched to steel or concrete for taller structures because of perceived limitations in wood-framed construction.
Detailing the main lateral force-resisting system with plywood shearwalls was a challenge for this project, which was in a high seismic area. We had to develop new details for high-load shearwalls to deal with the loads in the lower levels of the structure, and we quickly realized traditional holdowns would not easily meet the high overturning demands. Uplift restraint was provided by an innovative new Anchor Tie-Down System using high-strength rods, bearing plates and shrinkage compensation devices.
While these construction details were novel concepts at the time, economic forces made them commonplace very rapidly. Intense demand for housing fueled a trend toward denser, mixed-use developments in downtown areas, and the economic benefits of wood meant these developments were often wood-framed.
In the United States, the International Building Code limits wood-frame residential construction to five stories. In Canada, however, the British Columbia Building Code was changed in 2009 to allow six-story wood-framed structures, which was an increase from four. We now see many taller structures being built in British Columbia with wood being the primary structural material.
Located in Richmond, British Columbia, The Remy Project* was the first six-story wood-framed structure to be built in Canada. The 258-unit condominium building was originally designed as a steel frame over a concrete parking garage. However, the building was redesigned with wood, resulting in a savings of 12%, or 4.8 million (CAD).
Another great example is The Skyline, located in Victoria, British Columbia. This 58-unit condominium structure was originally intended to be four stories, but was modified to six stories after the building code modification.
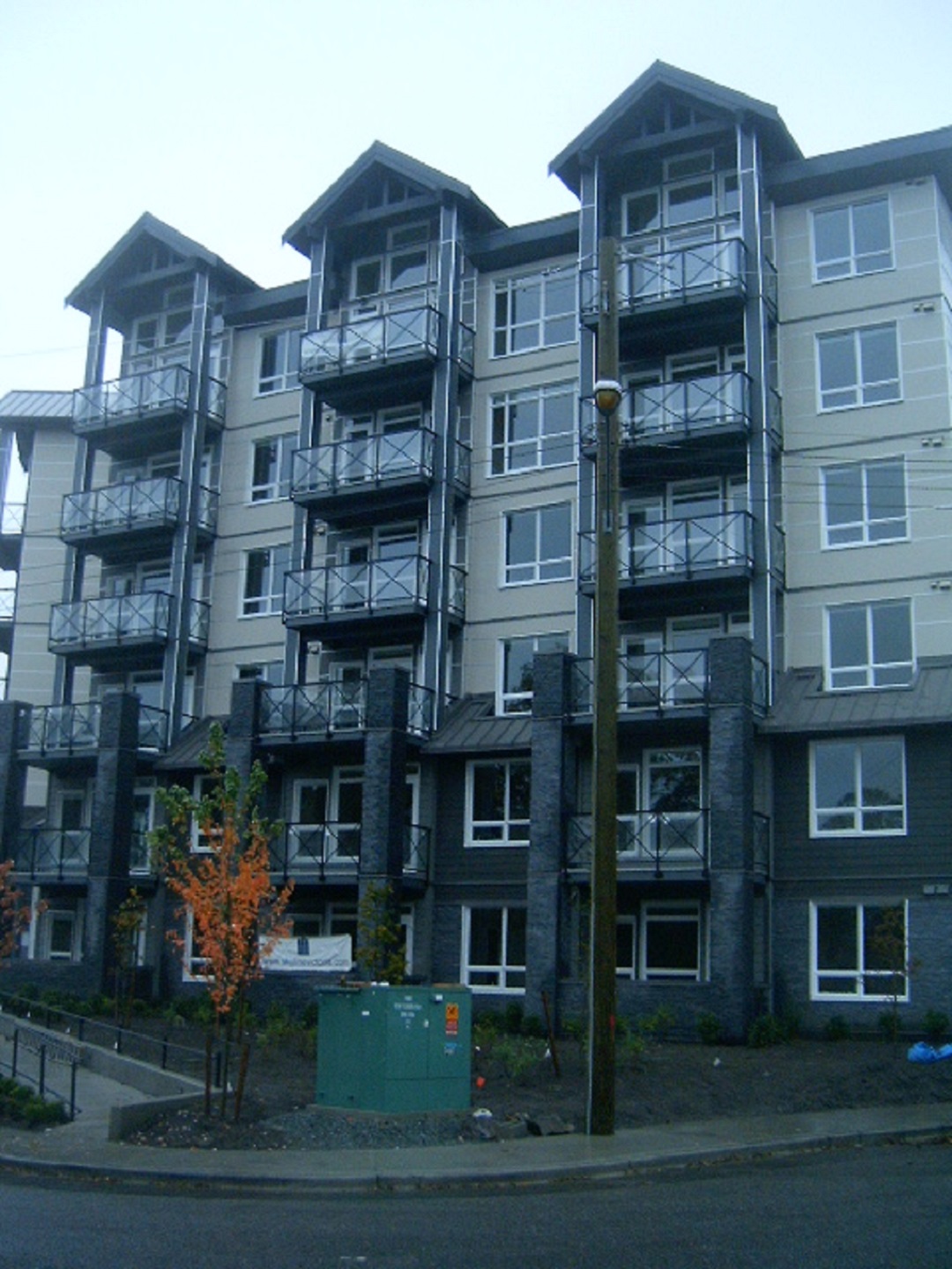
Due to the number of stories and locations of the buildings in high seismic areas, the overturning forces on the shearwalls were very high. The cumulative tension demand loads at the foundation level were as much as 60,000 pounds. Most wood-framed structures can be restrained with conventional holdowns; however, to accommodate these high forces, the Simpson Strong-Tie® Anchor Tiedown System (ATS) was utilized for the shearwall overturning restraints. This continuous tiedown system consists of a series of rods connected from the roof to foundation, providing every level with a point of restraint, including bearing plates, shrinkage compensation devices, and nuts.
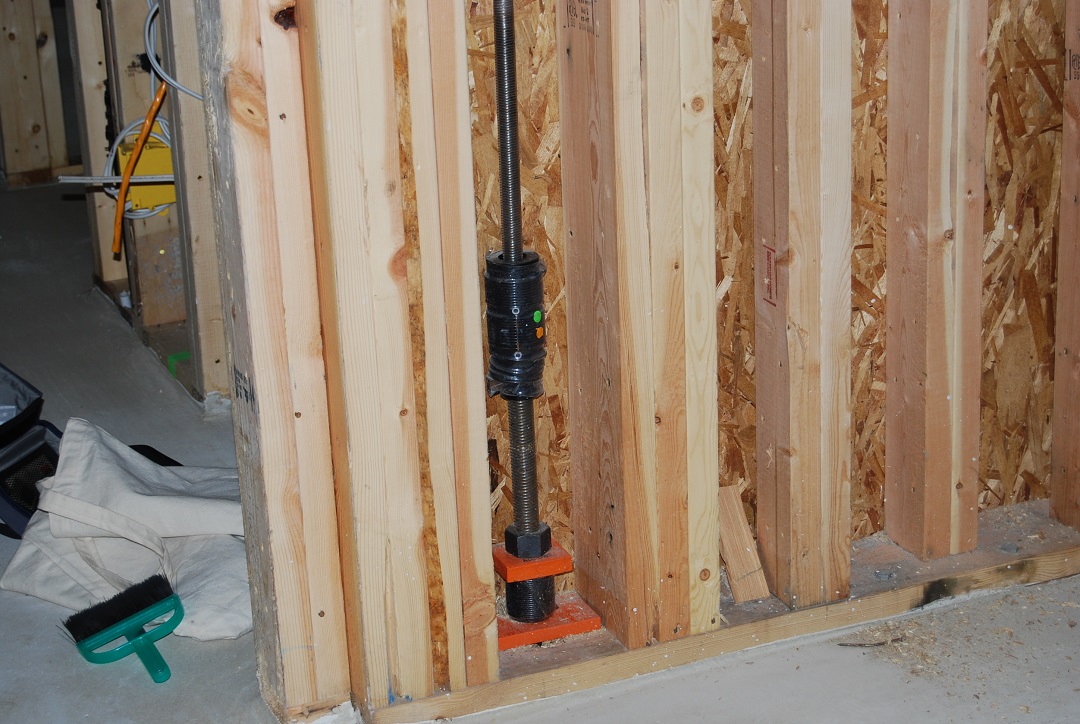
For both of these structures, drift posed limitations on the majority of the shearwall designs. The shrinkage that occurs can be significant in a six- story wood-framed building. As the wood dries, gaps occur between the nuts and the bearing plates, which should be added to the vertical deflection portion of the drift equation. To resolve this, shrinkage compensation devices were provided for every level in order to eliminate those gaps, which reduced the vertical deflection and improved the shearwall performance.
Increasing the height of wood-framed buildings helps reduce construction costs and also provides designers more flexibility, especially in areas trying to maintain urban growth. Constructing taller buildings allows for smaller building footprints with higher density, which reduces the environmental impact and creates more affordable spaces for end users. Remy and The Skyline will be models for future five- and six-story wood-framed buildings, and will provide engineers and contractors a great deal of knowledge in how to build safe, reliable structures.
*Before Remy was finished, a construction fire destroyed the building. Since that time, Remy has been rebuilt and the structural framing is complete.
What do you think about height limits for wood-framed construction? Let us know by leaving a comment.
– Paul
P.S. Don’t forget to vote in our “Creative Uses of Our Product” contest by December 20! See last week’s post for details.
What are your thoughts? Visit the blog and leave a comment!
Developing with wood also has its benefits because it is easy to work
with, shows symptoms over running and is a alternative source. Wood is a
good content for structures, Wood light-framing is a technique that has
a long record of achievements. As items and technological innovation
keep relocate, the property technique will also adjust.
http://www.cewqatar.com