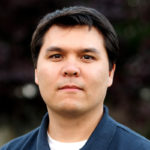
[Simpson Strong-Tie note: Shane Vilasineekul is the Simpson Strong-Tie Engineering Manager for the Northeast U.S. and one of our guest bloggers for the Structural Engineering Blog. For more on Shane, see his bio here.]
The end of this month will mark the one year anniversary of Superstorm Sandy hitting the coastlines of New Jersey, New York, and surrounding states. A lot of construction has taken place in the last 12 months, but most of the rebuilding will occur over the next few years. The boardwalks were a high priority because of their effect on tourism, which is so vital to the local economies, and most of them have been completed (see my previous post about rebuilding after Sandy here). Now the focus has shifted to repairing, raising, and rebuilding homes.
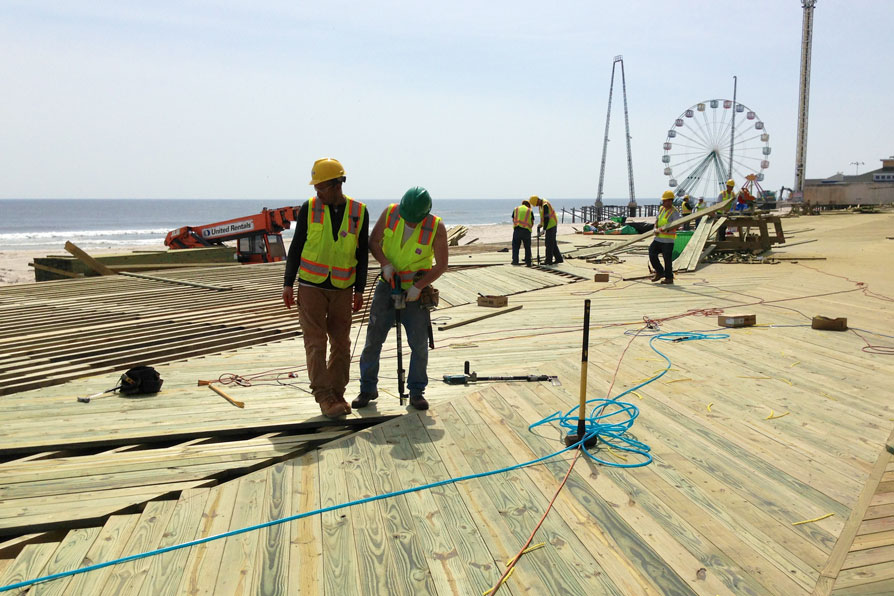
I am writing this while sitting in the Newark airport, headed home after presenting one of our workshops on high wind design. The workshop was held at a hotel in Manahawkin, New Jersey that happened to be used last year by residents displaced by the storm, including some of the architects and engineers in attendance this morning. After talking to a few of them at the breaks, it sounded like they are struggling with the current state of building provisions, which were quickly put in place to ensure rebuilt properties are more resilient, including new flood elevations and renewed focus on code compliance.
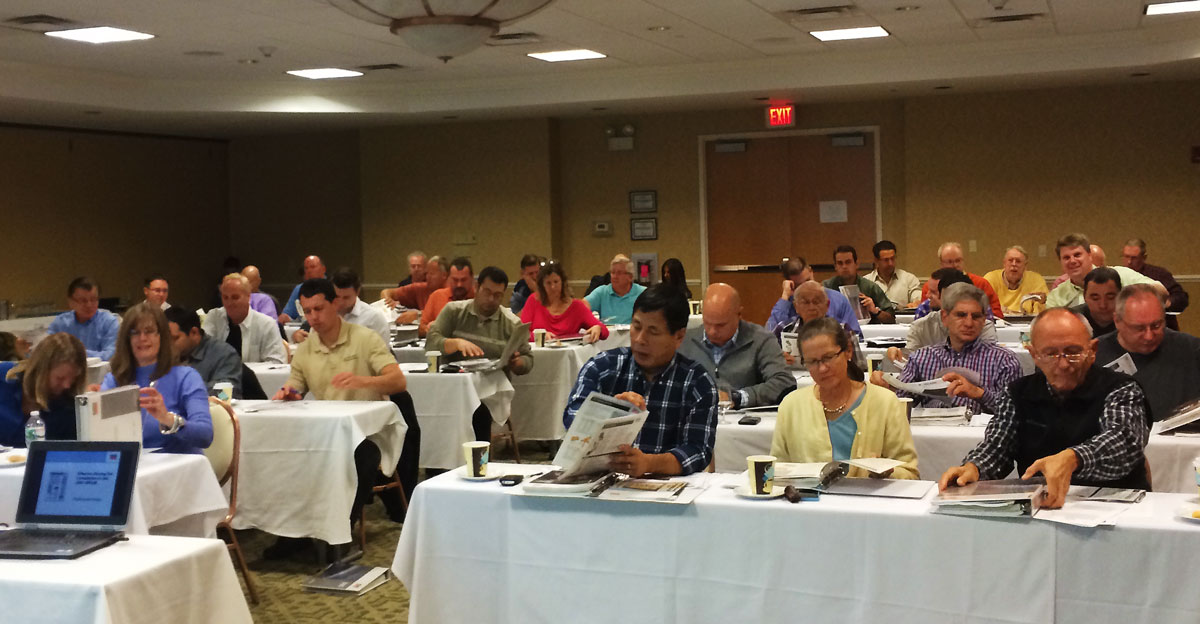
Almost all of the affected areas of New Jersey have design wind speeds between 100 and 120 mph, which triggers a wind design in the 2009 IRC. So homes previously constructed under codes that permitted prescriptive wall bracing are being rebuilt with designed shear walls and diaphragms. In the design example we ran in the workshop, we used worst case conditions of 120-mph and Exposure C on a typical 2-story home that you might see in a NJ beach community. Due to the long, narrow footprint common along the coast, open lower level, and limited full-height walls in the front elevation, the end result was pretty ugly: double-sided WSP shear walls and holdown forces at the lower level in excess of 15-kips.
These types of forces can be a challenge regardless of any other factors, but some unique conditions in New Jersey add to the complexity. First, many of these homes are built on wood pile foundations so connections to wood beams, which are often set back from the exterior walls, can be a detailing challenge. Second, factory-built structures are extremely popular in the area right now because of the promise to deliver a new home that can be ready for occupancy in a matter of weeks, but jobsite-access to the wall cavities in these homes is limited or nonexistent. Finally, there are often several designers involved in the project (designer of record, foundation engineer, & factory-built-home designer) which causes issues with coordination and detailing.
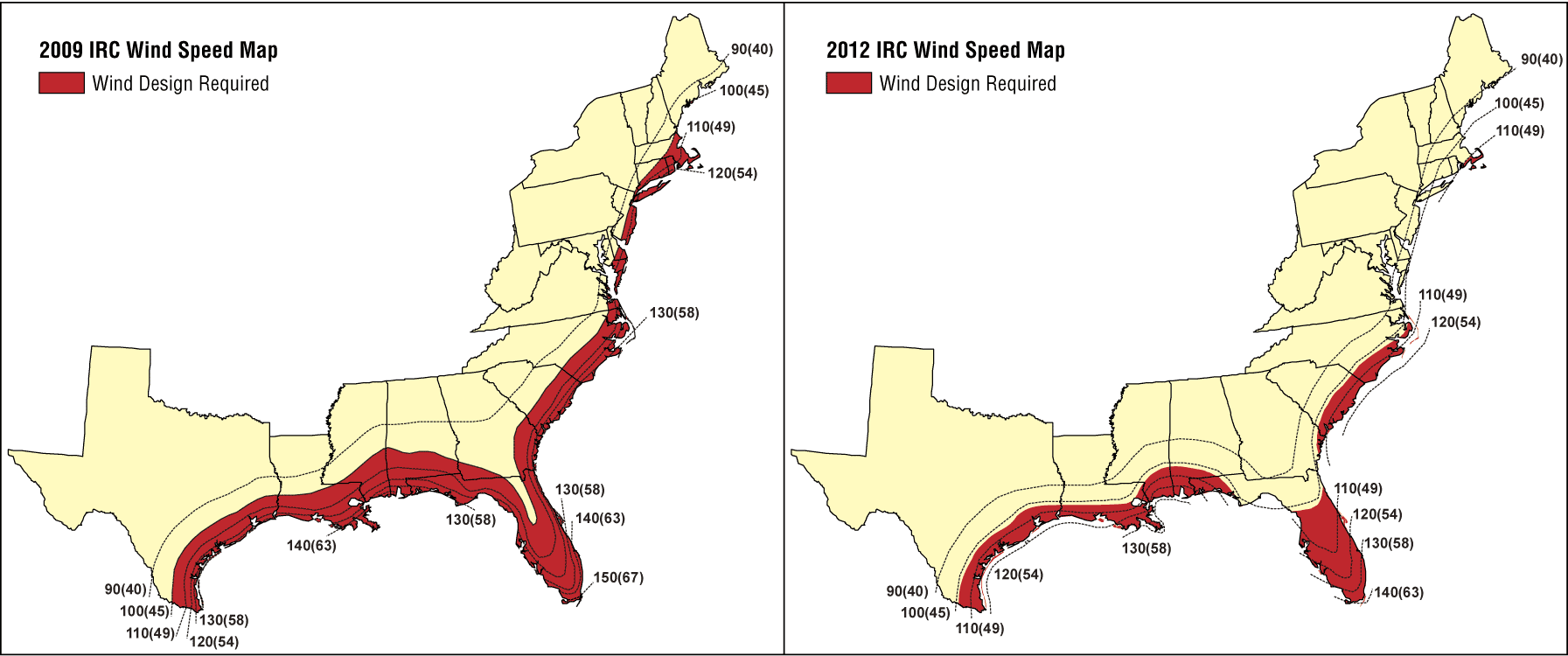
The building community in New Jersey is up to the challenge, but I thought it was amusing that when I mentioned that the new wind maps in the 2012 IRC® (currently on the Governor’s desk) eliminate New Jersey from wind design requirements, I practically had to stop the presentation to answer all of the questions from designers eager to avoid all of the design headaches. Every so often someone would raise their hand during the presentation and say, “So we won’t have to do this when the new code is adopted, right?”
FEMA is planning to release the Mitigation Assessment Team’s storm report in time for the anniversary (although the government shutdown might delay it). The latest draft contains 59 conclusions and recommendations that touch on a range of issues including climate change, retrofitting existing structures, and foundation design (Paul did a blog post in August touching on the rebuilding strategy). The detailed report should provide a wealth of valuable information for designers and planners in the region, as well as other coastal communities.
– Shane
What are your thoughts? Visit the blog and leave a comment!