Last week marked the 30th anniversary of the Florida landfall of Hurricane Andrew, one of the most damaging, and influential, hurricanes ever to hit the United States. Hurricane Andrew hit South Florida with Category 5 winds early on the morning of August 24, 1992. Andrew caused damages of $25 billion in Florida, and another billion dollars’ worth when it struck Louisiana as a Category 3 hurricane two days later. This image, from NASA Earth Observatory, shows Andrew on August 23, 24, and 25.
Engineers tend to learn something about wind resistance from every major hurricane, and Andrew was certainly no exception. In this writer’s opinion, the main lessons of Hurricane Andrew were fourfold: (1) proper roof deck nailing, (2) testing of roof coverings for wind resistance, (3) protection of openings from wind-borne debris, and (4) proper construction of gable ends.
Roof Deck Nailing
Prior to Hurricane Andrew, contractors, inspectors, and designers tended to pay more attention to the fastening at the edges of the roof decking panels, because those fasteners are the ones that determine the shear resistance of the roof diaphragm. However, in a windstorm it’s the fasteners in the interior of the panel that are the more highly stressed in withdrawal, because they’re spaced farther apart. Research conducted by APA, the Engineered Wood Association, in Andrew’s wake showed that the installation of these interior fasteners was more important than previously considered, and that if even one of these is missing or misplaced, it can affect the performance of the entire panel.
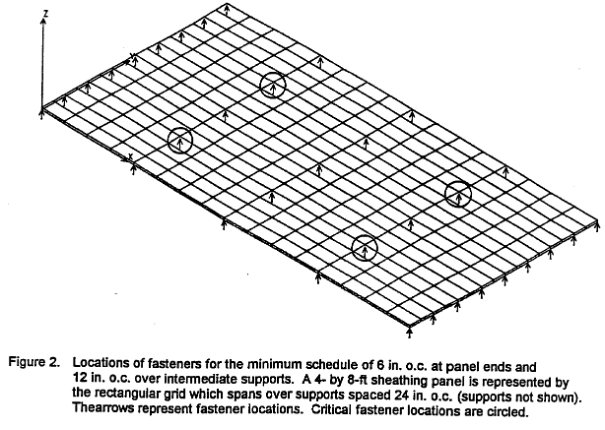
Some reports after Andrew observed that the use of staples was inadequate to attach roof decks. Generally nails have been the required method, since Andrew, for fastening roof decking in high-wind regions.
Furthermore, the locations of roof sheathing damage strongly reinforced the importance of using Components and Cladding (C&C) loads to design roof sheathing fastening. After Andrew, prescriptive codes and standards began showing increased nailing requirements, even reducing nail spacing to 4″ on center, for nails in panels at roof end zones due to high C&C loads. Most recently, due to even higher C&C roof loads in ASCE 7-16, the wood and fastener industries have collaborated to develop a new type of nail, the roof sheathing ring-shank (RSRS) nail, for use in fastening roof decks. The RSRS nail has rings on the shank to aid in withdrawal resistance, and a larger head to add resistance to nail head pullover.
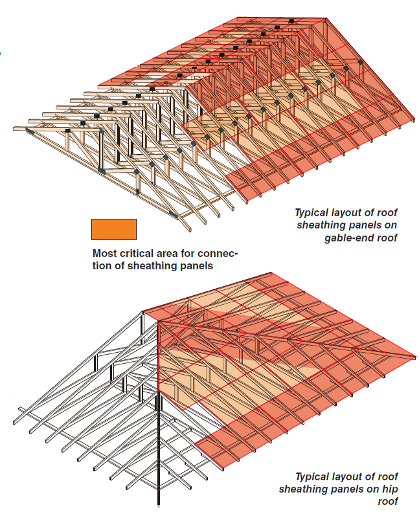
Testing of Roof Coverings for Wind Resistance
The FEMA report, Building Performance: Hurricane Andrew in Florida, states “Field observations concluded that the loss of roof cladding was the most pervasive type of damage to buildings in southern Dade County.” Prior to Andrew, test procedures existed for roof coverings, but testing for higher wind speeds was generally not required. For example, at that time, composition shingles were only tested to resist wind speeds of around 64 miles per hour (as this author recalls). Building code philosophy tended to focus on structural performance, not cladding. However, Andrew showed that if roof coverings are removed in a hurricane, the building could be severely damaged by water even if there are no structural failures. Further, roof coverings removed by the wind become windborne debris that can cause failure (or injuries) in surrounding buildings.
After Hurricane Andrew, Miami-Dade County became the first jurisdiction to require testing of all roof coverings to higher wind speeds, over the objections of some materials’ manufacturers. Once the requirement was in place in South Florida, manufacturers made tested products available, and the national building codes adopted similar requirements in the following years.
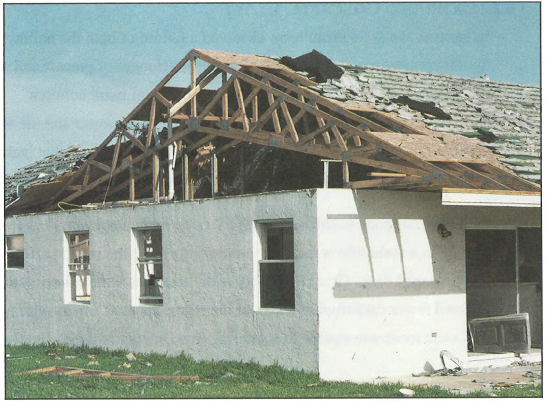
Protection of Openings from Wind-borne Debris
Dr. Joseph Minor, P.E., in his paper “Lessons Learned from Failures of the Building Envelope in Windstorms,”1 states, “As early as 1972, investigators at Texas Tech University observed that wind-borne debris plays a major role in damaging the building envelope.” Major failures were seen from roof gravel blowing off and damaging nearby buildings in downtown Houston in Hurricane Alicia in 1983.
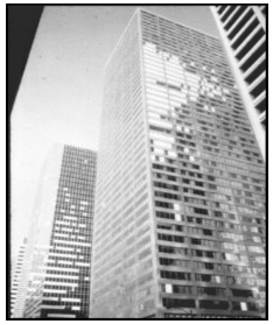
Codes and standards contained requirements that buildings with openings had to be designed for higher internal pressure. But it was left up to the designer’s judgment to decide what should be considered an “opening”.
However, after Hurricane Andrew it became such an obvious issue that it could no longer be ignored. Two major issues were observed. First, if a window or other opening is broken by debris in a hurricane, it allows wind and water into the building, ruining everything inside, even if there is no structural damage. Second, the opening in the envelope allows the wind to penetrate inside the building, causing a large increase in internal pressure, which can cause structural damage.
As a result, Miami-Dade County was the first to add a requirement into their code that openings in the building envelope must be protected from wind-borne debris either by installing tested windows and doors or by adding tested impact protection, such as shutters.
ASCE 7 took more of an incremental approach in their treatment of wind-borne debris. In ASCE 7-93, there were only two conditions for internal pressure: Condition I and Condition II. Condition II is what came to be defined as Partially Enclosed, and required a design to a higher internal pressure where openings in one wall exceeded the openings in the remaining walls. ASCE 7-95 was the first edition to contain wind-borne debris protection requirements. It introduced the definitions of enclosed, open, and partially enclosed buildings that essentially remain today. Table 6-4 contained four cases for internal pressure coefficients: open buildings, partially enclosed buildings, buildings not meeting the other three cases, and buildings meeting a fourth case. This fourth case was defined as buildings sited in hurricane-prone regions, with a windspeed greater than or equal to 110 mph, with glazed openings in the lower 60 feet that were neither designed to resist wind-borne debris nor specifically protected from wind-borne debris impact. Buildings meeting this fourth case had to be designed using the same internal pressures as a partially enclosed building. This was slightly clarified in ASCE 7-98 when the internal pressure coefficients table was reduced back to just open, partially enclosed, and enclosed classifications, and a new section in the text was added stating “Glazing in the lower 60 ft. of Category II, III, or IV buildings sited in wind-borne debris regions shall be impact-resistant glazing or protected with an impact-resistant covering, or such glazing that receives positive external pressure shall be assumed to be openings.” While this addressed the issue of increased internal pressure from damage to openings, it still did not address the issue of having a building loss due to entrance of wind and water through openings. ASCE 7-02 took the final step to where we are today, requiring that openings in buildings located in wind-borne debris regions be protected. It stated, “Glazing in buildings classified as Category II, III or IV (Note 1) located in wind-borne debris regions shall be protected with an impact-resistant covering or be impact-resistant glazing according to the requirements (Note 2) specified in Ref 6-1 and Ref 6-2 referenced herein or other approved test methods and performance criteria.” References 6-1 and 6-2 were ASTM E1886 and ASTM E1996, respectively.
Proper Construction of Gable Ends
The final major lesson learned from Hurricane Andrew was that gable ends deserved more attention than they had previously been given.
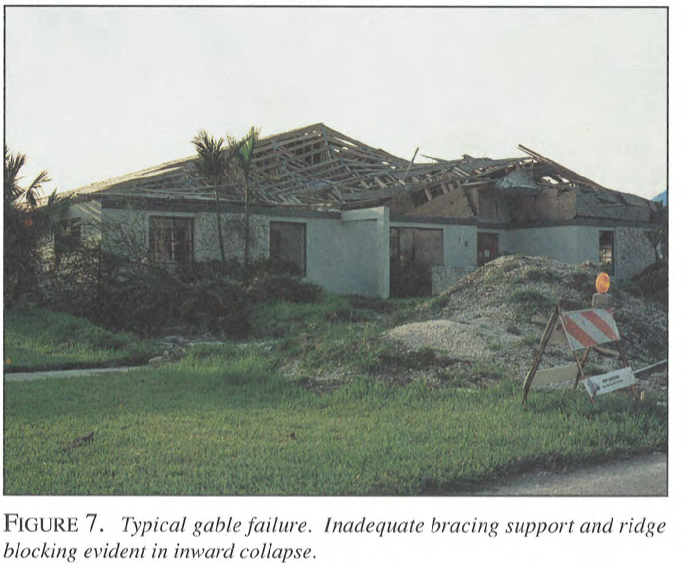
On masonry buildings, the walls may still be standing, but the trusses could still collapse due to loss of support from roof sheathing. On wood-frame buildings, entire gable walls may collapse.
After Andrew, new requirements were added to codes requiring that wood-frame gable ends have continuous framing from the floor to the roof (balloon framing). Fastening of roof decking to gable end trusses was increased in prescriptive documents and codes. The wood industry developed details for bracing of gable ends. The following two illustrations are taken from “Hurricane Andrew, Part 2, Wood Building Analysis and Recommendations,” from the National Forest Products Association, November 1992.
These details have now made their way into standards such as the American Wood Council Wood Frame Construction Manual for One- and Two-Family Dwellings (ANSI/AWC WFCM).
Methods were also developed to retrofit existing gable ends to better resist the out-of-plane wind loads from hurricanes. These can now be seen in such documents as Appendix C of the 2021 International Existing Building Code, Section 1704 of the 2020 Florida Building Code, Existing Building, and FEMA P804, Wind Retrofit Guide for Residential Buildings, as shown below.
These are the main areas where codes were improved as a response to Hurricane Andrew, in the opinion of this author. There were surely others. For another take on what was learned from Andrew, see this video of Tim Reinhold, a well-known wind engineer. Thanks to the Insurance Institute for Business and Home Safety for this.
Do you have any recollections or resources to share?
- Journal of Architectural Engineering, © ASCE / MARCH 2005