The 2009 IBC Section 1604.4 states, “Load effects on structural members and their connections shall be determined by methods of structural analysis that take into account equilibrium, general stability, geometric compatibility and both short and long-term material properties.” This requirement applies to a 200 pound handrail connection as well as a 50,000 pound glulam connection.
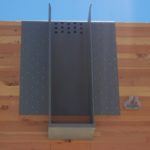
50 kips is not a typical beam reaction in wood framed construction, but we’ve received some recent requests to design higher capacity hangers for use in wood podium decks for mixed-use structures. Although post-tensioned concrete is most commonly used for this application, the use of heavy timber for podium decks is driven by the benefits of wood: sustainability, saving construction time and money, architecturally attractive, long-term energy savings, light construction material, and performance in earthquakes.
To respond to these requests for higher capacity connections, and to answer the question posed in the title of this post, Simpson Strong-Tie has designed hangers to accommodate this growing trend in construction. Wood podium framing may consist of glulam beam sizes up to 10 ¾” x 48” with service download and uplift reactions reaching up to 50 kips and 23 kips, respectively. This is due to large gravity loads and also seismic overturning loads on the shear walls.
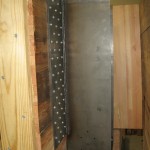
Hanger design included a three-step process: 1) engineering calculations, 2) finite element analysis and 3) lab testing. The design used 3 gauge steel for strength and 1-inch thick steel bottom plate to limit seat deflection. We used SDS screws for the face fasteners for ease of installation and high-load capacities. The face fastener quantity was chosen to carry the full service loads, neglecting the contribution of the top flange bearing capacity. The initial design did not utilize fasteners in the top flange, as SDS screw heads would interfere with floor sheathing.
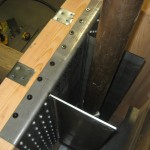
Finite element analysis (FEA) confirmed the hanger design performance and predicted high-stress areas, ultimate load and deflection. The analysis below shows a 78.7 kip allowable down load.
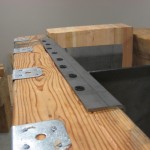
As good as calculations and FEA models can be, if you read this blog post, you know how much I love physical testing. No exception here, so these hangers were tested per ICC-ES AC13, Acceptance Criteria for Joist Hangers and Similar Devices. Physical testing helped us determine that hanger rotation at ultimate load created tension forces in the face fasteners, which reduced the vertical load capacity of the assembly. Turns out the top flange needed a good connection to the header to resist these rotation forces, so we added SDW screws since their low profile heads would not interfere with floor sheathing installation. With that modification, we retested the assembly and were able to hit the target loads.
What’s your take on this? Post a comment and let me know.
– Paul
What are your thoughts? Visit the blog and leave a comment!
give us a link to a video of the testing!
With as much strain energy is in the setup with a 150 kip actuator load on it, you would think stuff would really go flying at failure. This happens when we break steel, but if this case we had wood splitting failure, which tends to not be that catastrophic. For this test, even at failure the connection was still supporting over 80 kips of load. We’ll have to think up a more exciting test for video, though – that could be fun to see.
From the photos, I could not tell how many SDS screws were resisting the 23 kips of uplift. Also, assuming the bearing dimension of 6″ how were you able to prevent cushing of the GLB on the steel plate?
Good question on the bearing dimension. When load rating a hanger per AC13/ASTM D7147 we are required to do both a test limit (ultimate load with safety factor of 3, or 1/8″ deflection) and calculations (fastener shear, bearing, etc). For testing, ASTM D7147 allows testing of a different width bearing seat as long as we also do the bearing calculation as well. In this case, we tested on a narrower seat width (8 3/4″) for the test limit.
For the 50 kip download reaction, the bearing length was 8″ and the glulam width was 10 3/4″. With a perp-to-grain capacity of 650 psi, this gives us just over 55 kips bearing capacity.
For the cases with 23 kips uplift, we switched to a bolted connection.