One of the first projects I worked on when I got out of school was the Mexican Heritage Plaza in San Jose, California. It was a 200,000 square-foot facility with a theater, classrooms, art gallery and gardens. It was my first time using ETABs and SAFE for the building frame and mat slab designs, and there was no graphical interface. Text file input – those were the days! I learned how to detail bolted and welded steel connections, and then I got to enjoy every junior engineer’s first right of passage – reviewing shop drawings. It was eye-opening to learn that a detailer needed to translate all the dimensions, size call-outs and typical details into exact measurements down to the sixteenth of an inch for every single member, bolt, and hole.
I am sure I spent too much time reviewing them and checking that all the numbers added up. Photocopying E-size drawings was more expensive than a junior engineer’s time back then, so before I hand copied my mark-ups over to five sets of drawings, I reviewed them with my manager. She circled the high-strength anchor rods for the special moment frames and wrote “Too short – recheck.” I pointed out that I had checked the grout pad, base plate and washer thickness to make sure the anchor rods extensions were long enough to fully thread the nuts on (they just worked). She told me that high-strength anchor lengths were always too short. It didn’t make sense to me at the time, but I marked up the drawings and sent them off. More on this later.
Common specifications for steel anchor rods used for concrete anchorage are ASTM A307, A449 and F1554 Grades 36, 55, 105. Some of these anchor rods have specifications appropriate for welding. According to AISC Design Guide 21 on Welded Connections, “unless the supplier of the anchor rod can provide assurance that the compositional limits of ASTM A36 have been achieved, weldability of F1554 Grade 36 should be investigated”. Both ASTM F1554 Grade 55 and ASTM A307 provide supplementary requirements for welding applications in Section S1. The S1 requirements limit the percentage of carbon equivalent permitted for the metal alloy. Where welding is required designers should specify F1554 Grade 36 with the compositional limits of ASTM A36 or F1554 Grade 55 ordered with supplementary requirement S1. ASTM A307 specified with supplementary requirement S1 can be ordered for anchor rods where welding is required.
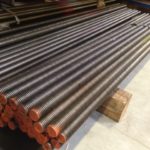
There is a blend of art and science in the manufacturing of high-strength steel anchor rods (ASTM F1554 Grade 105, A325 and A449). Like a pastry chef, creating a perfectly baked soufflé with the correct ingredients and temperature, modern day blacksmiths achieve a balance of strength and ductility characteristics for anchor rods through controlled quenching and tempering treatments. The rapid cooling of metal through quenching increases toughness and strength, but it often increases brittleness. Tempering is a controlled reheating and cooling of the metal which increases ductility after the quenching process. Precise control of time with the application of temperature during the tempering process is critical to achieve an anchor with well-balanced mechanical properties.
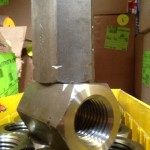
AISC does not recommend welding of high-strength anchor rods including, but not limited to, ASTM F1554 Grade 105, A325, and A449. The heat input from welding can alter the physical properties and other elements from the weld metal are introduced altering the metal alloy for high strength anchors. Similarly, quenched and tempered steel used to fabricate high strength nuts or couplers is also not suitable for welding.
Now let’s get back to my first steel project. We asked the steel detailer to recheck the anchor rod lengths, and they added 1” of extension above the top of concrete and shipped the assemblies with 16-gage steel templates attached with double nuts. Several templates were damaged in shipping so the contractor fabricated new ones. Somewhere in the process of swapping out templates and reattaching them with double nuts, the anchor rods were set 1” too low. Since the detailer added 1”, everything fit perfectly. And I understood why high-strength anchor rods could never be too long.
Have you ever had to detail a repair for a short anchor rod on a project? Visit the blog and leave a comment!
Too long rods are not always a good thing.
I was doing a safety inspection at a local HS stadium.
The anchor rods for the stadium superstructure extended about 4″ above the nut on the bolts. Since some of the column base plates were in areas accessible to kids, I had them cut off all but about 1/2″ of the projection so no one horsing around could get accidentally impaled on one of the rods.
An engineers job doesn’t end when the contractor finishes his punchout list.