Floors and roofs on mass timber buildings are constructed from large panels of engineered wood, such as cross-laminated timber (CLT) or mass plywood. Designers join these prefabricated panels together on site to create a structural horizontal diaphragm to transfer wind and seismic loads to the vertical elements of the lateral force resisting system. Shear forces between panels must be transferred through these panel-to-panel connections. Conventional wood structural panel sheathed diaphragms have shear capacities and fastener spacing tabulated in Special Design Provisions for Wind and Seismic (AWC SDPWS). Mass timber diaphragms, on the other hand, require some more design work by the designer.
Simpson Strong-Tie has provided designers with several diaphragm options to satisfy load requirements using four different connection types. Plywood splines are recessed into edge milling of the CLT panels and fastened with screws or nails. Steel splines can generally be installed on the surface of the CLT panels without edge milling, and are fastened with screws or nails. Butt joints are connected with fully threaded screws driven at an angle on alternating sides of the joint. Half-lap joints require edge milling so panels can overlap at the joint and the connection is made with screws driven perpendicular to the surface.
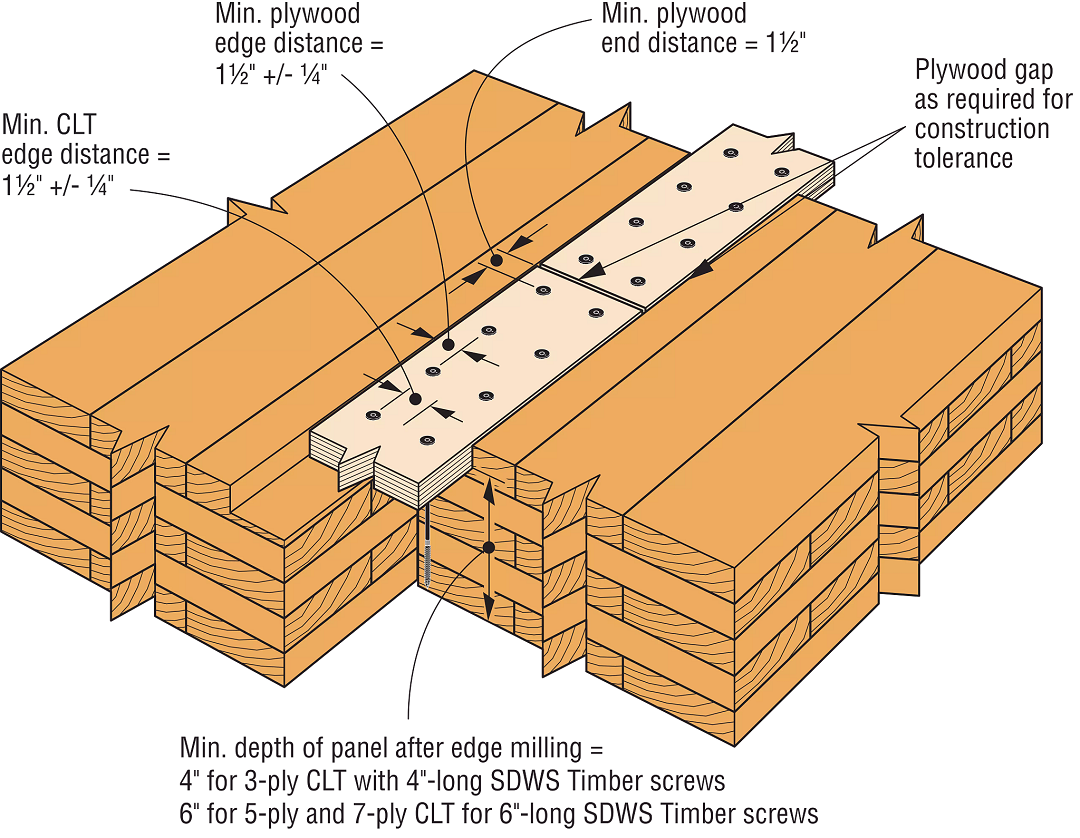
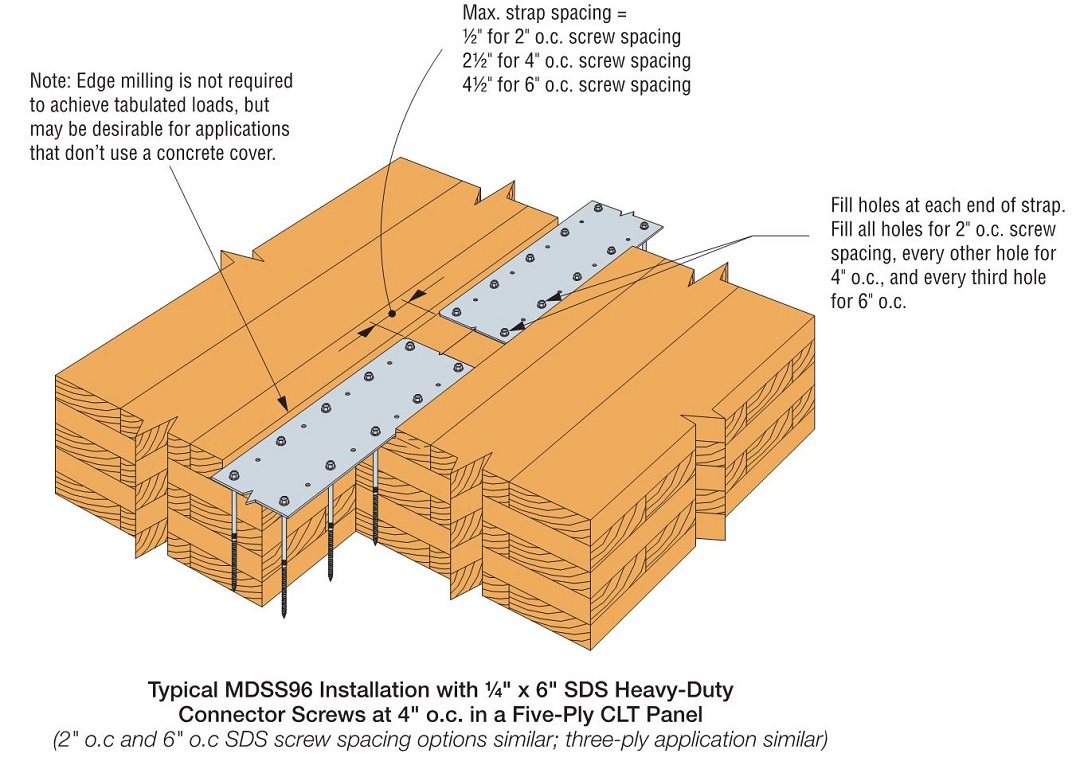
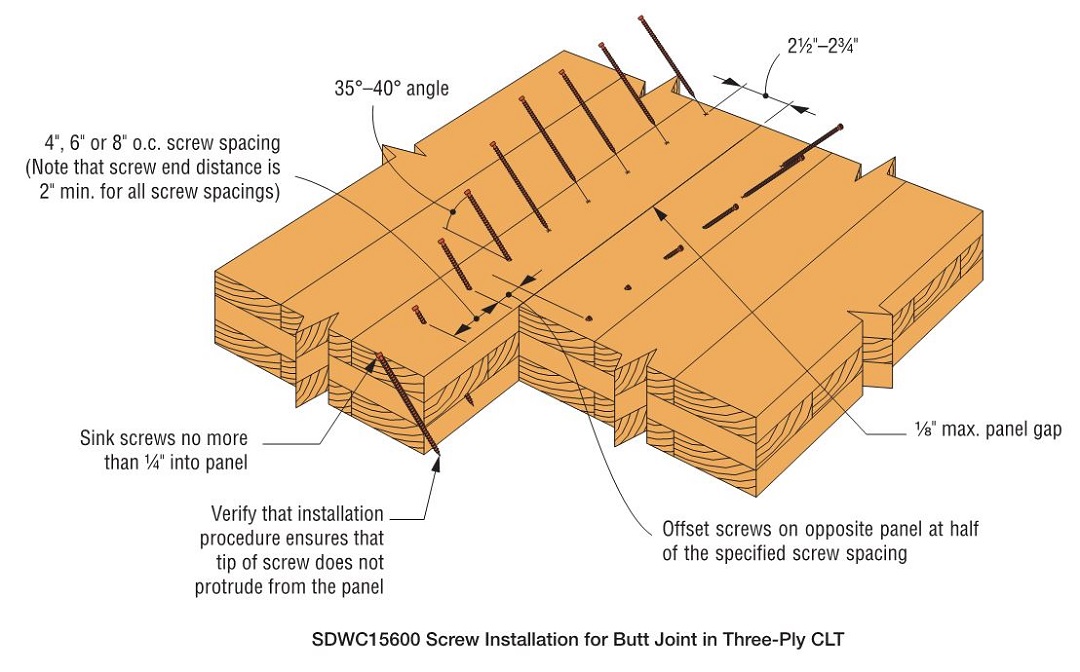
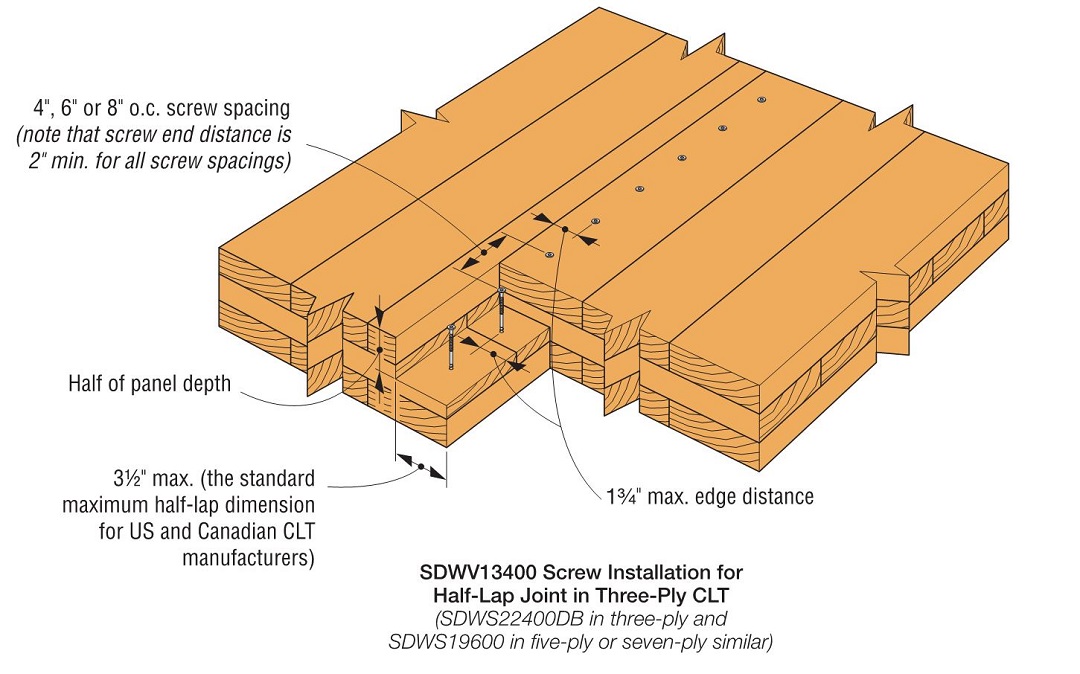
Steel splines are an economical solution, because they lower costs by reducing or eliminating manufacturing time for milling panel edges and are less susceptible to moisture damage during construction. Simpson Strong-Tie developed our MDSS Medium Diaphragm Spline Strap in 2020. The MDSS is a 14-gauge strap that uses our Strong-Drive® SDS Heavy-Duty Connector screws for the connection, spaced at 4″, 6″ or 8″ on center. And, of course, our load values are based on testing:
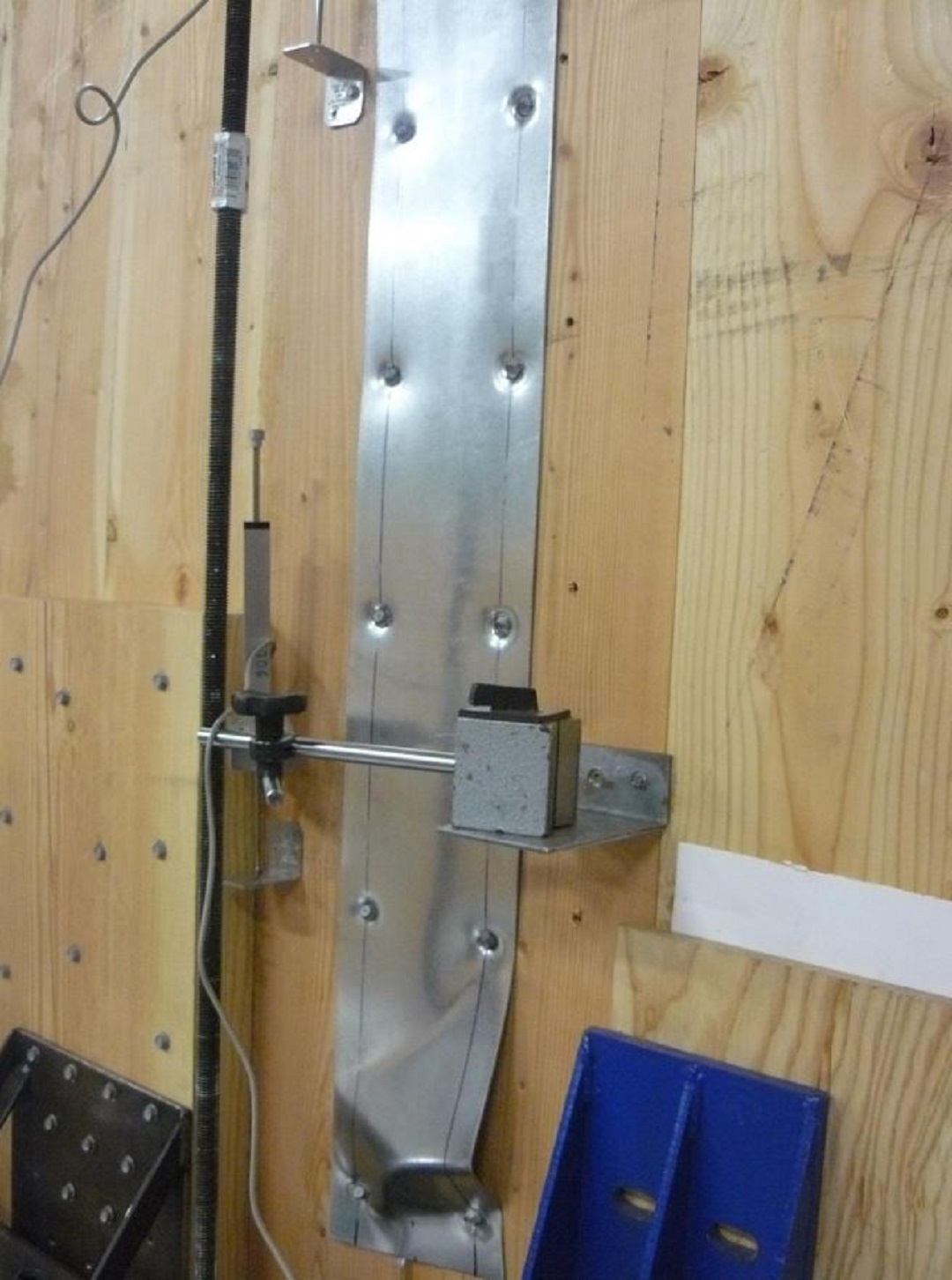
Our CMSTC16 (originally released in 2001, for you Simpson Strong-Tie history buffs) is a 16-gauge coil strap intended for tension applications. We tested the CMSTC16 as a spline connection to provide a lower-cost, nailed solution for mass timber splines. Feedback from engineers and installers was generally positive, but there were also requests for a lighter-gauge strap that was a little wider to accommodate construction tolerances.
The LDSS48 Light Diaphragm Spline Strap was created to address these requests from customers. The 18-gauge strap is 3/4″ wider than the CMSTC16 and the holes are spread wider, creating more edge distance for the fasteners. We originally developed an embossed hole for our CSHP High-Performance Coiled Strap that allows nails to be installed using a standard framing nailer. We incorporated this dome hole into the LDSS to make pneumatic nail installation easier.
As we explored other fastener options, we noticed that the head of a Strong-Drive® WSV Subfloor screw fits nicely in the dome. So we tested the WSV in the dome hole to determine the allowable loads for a steel-to-wood connection — and they were great. This led us to load-rate our spline connection with both nails and WSV Subfloor screws. More testing:
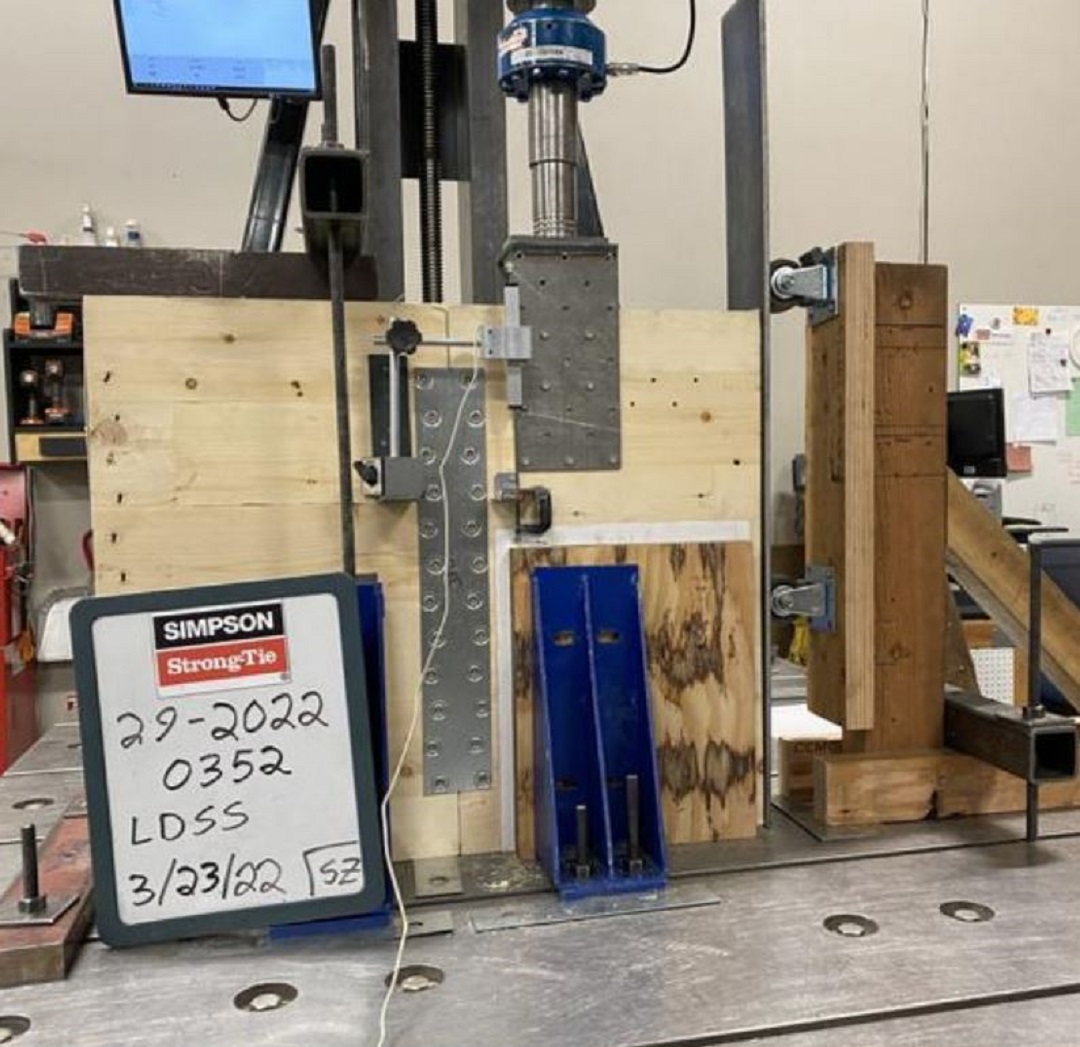
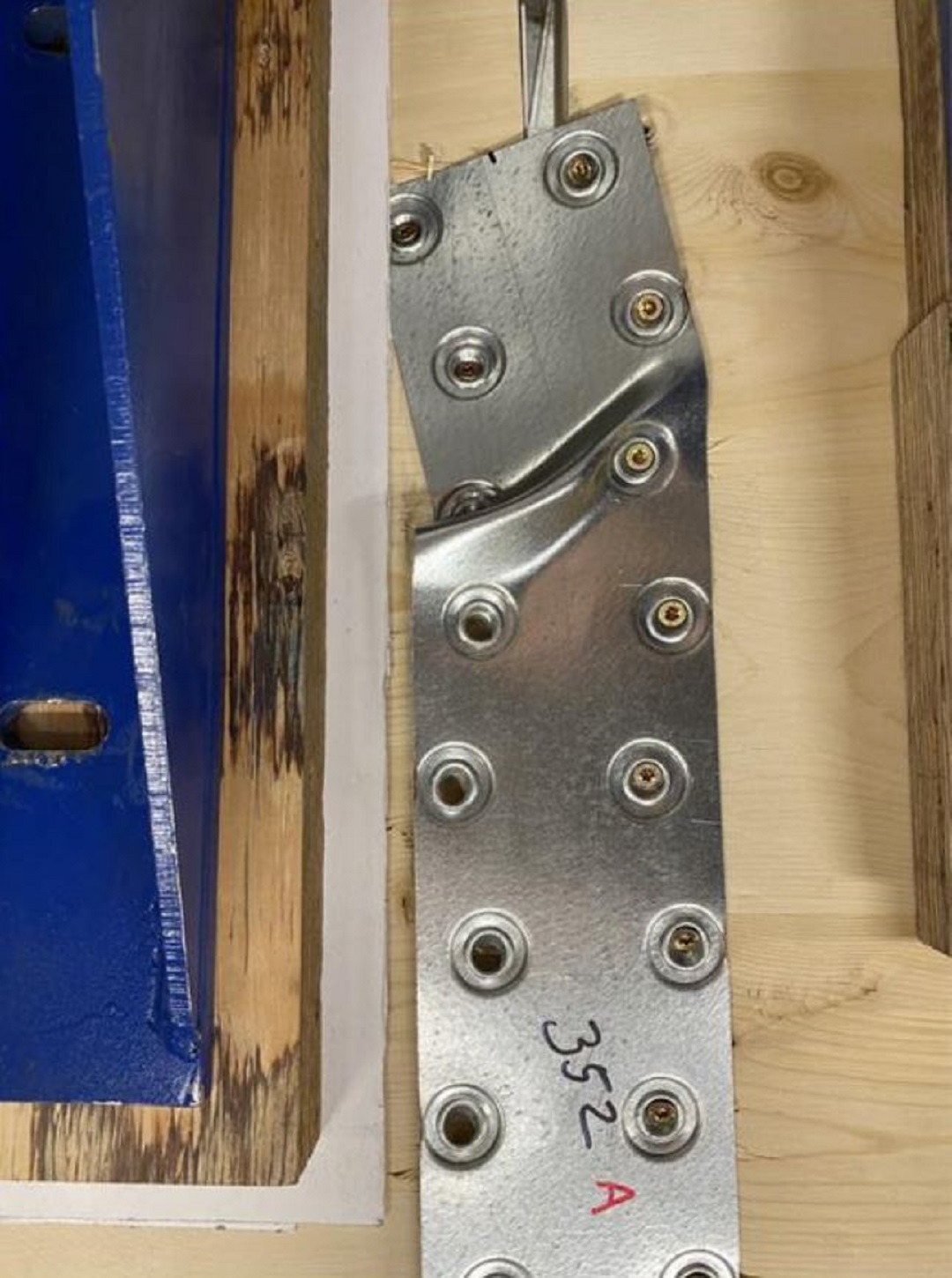
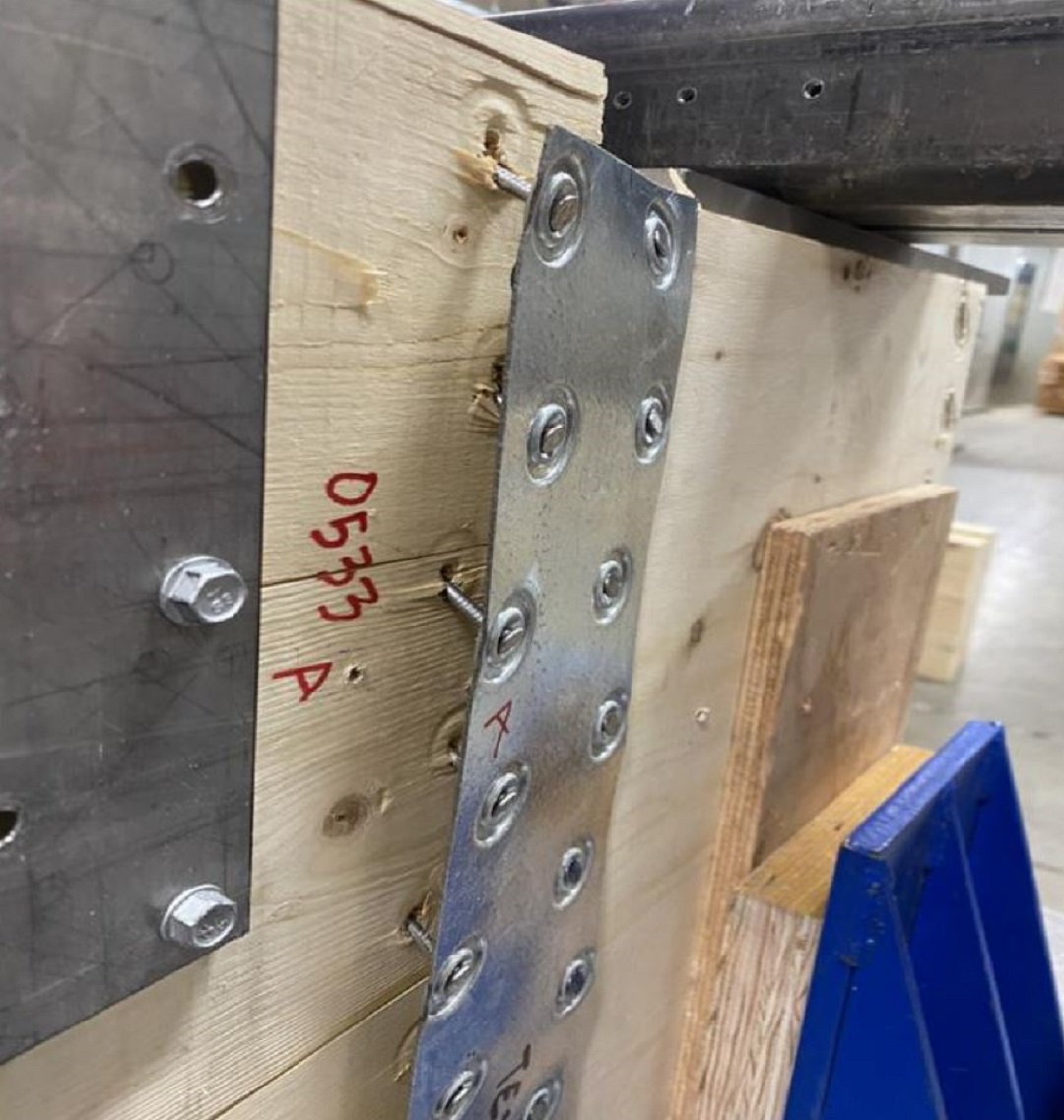
The WSV Subfloor screw is a collated screw designed to be installed using our Quik Drive® auto-feed screw driving system. Our fastener engineering team developed a noseclip (PNOSECLIP-LDSS) that allows the Quik Drive tool to work with the LDSS dome feature to locate the WSV screw in the hole.
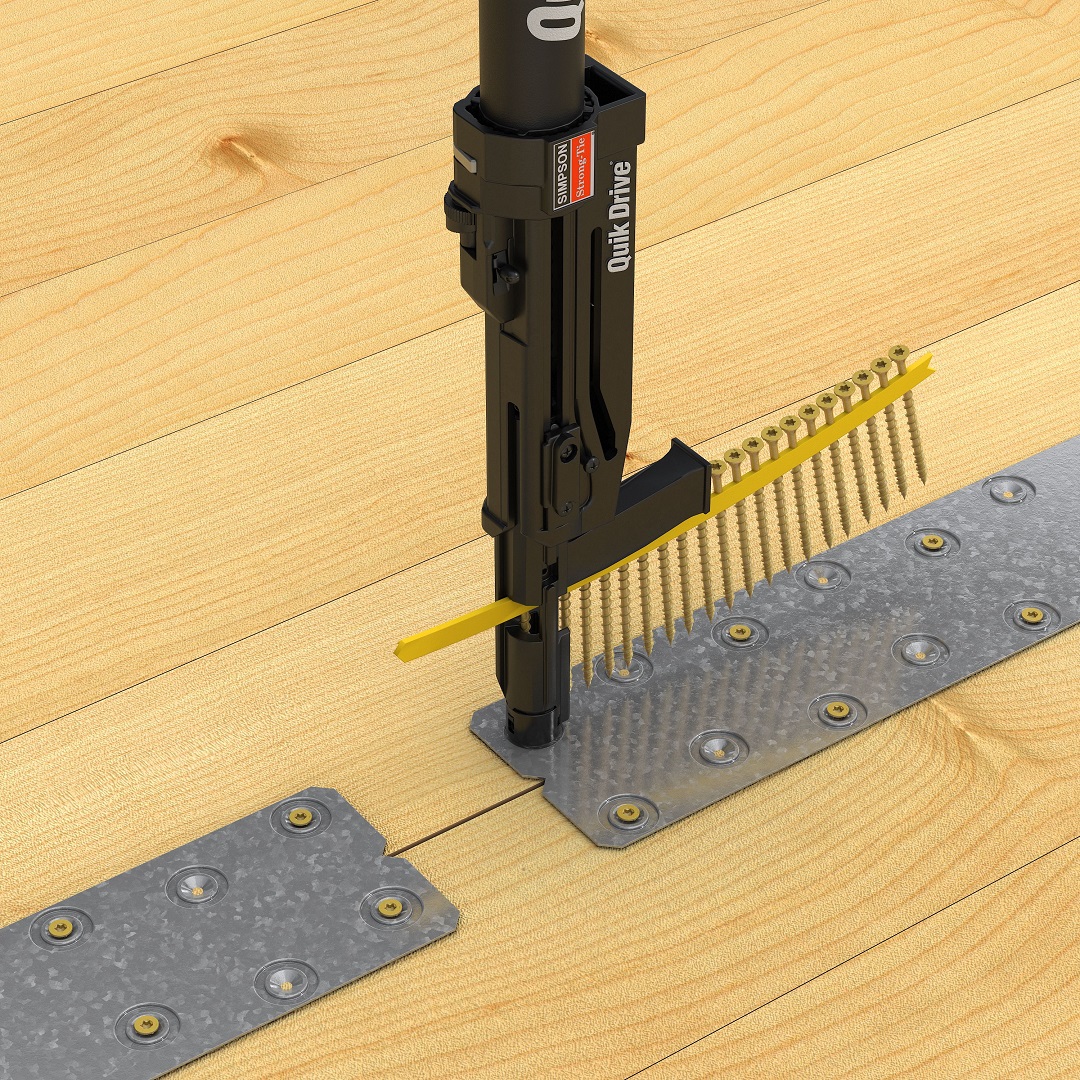
This product started with a request for a lighter strap that was a little wider, with loads similar to those of plywood splines. There was a lot of collaboration between Manufacturing and the Connector and Fastener teams to assemble all the pieces. It was rewarding to see the LDSS48 evolve through research and development into a high-capacity solution that could be installed from a standing position using a collated Quik Drive screw.
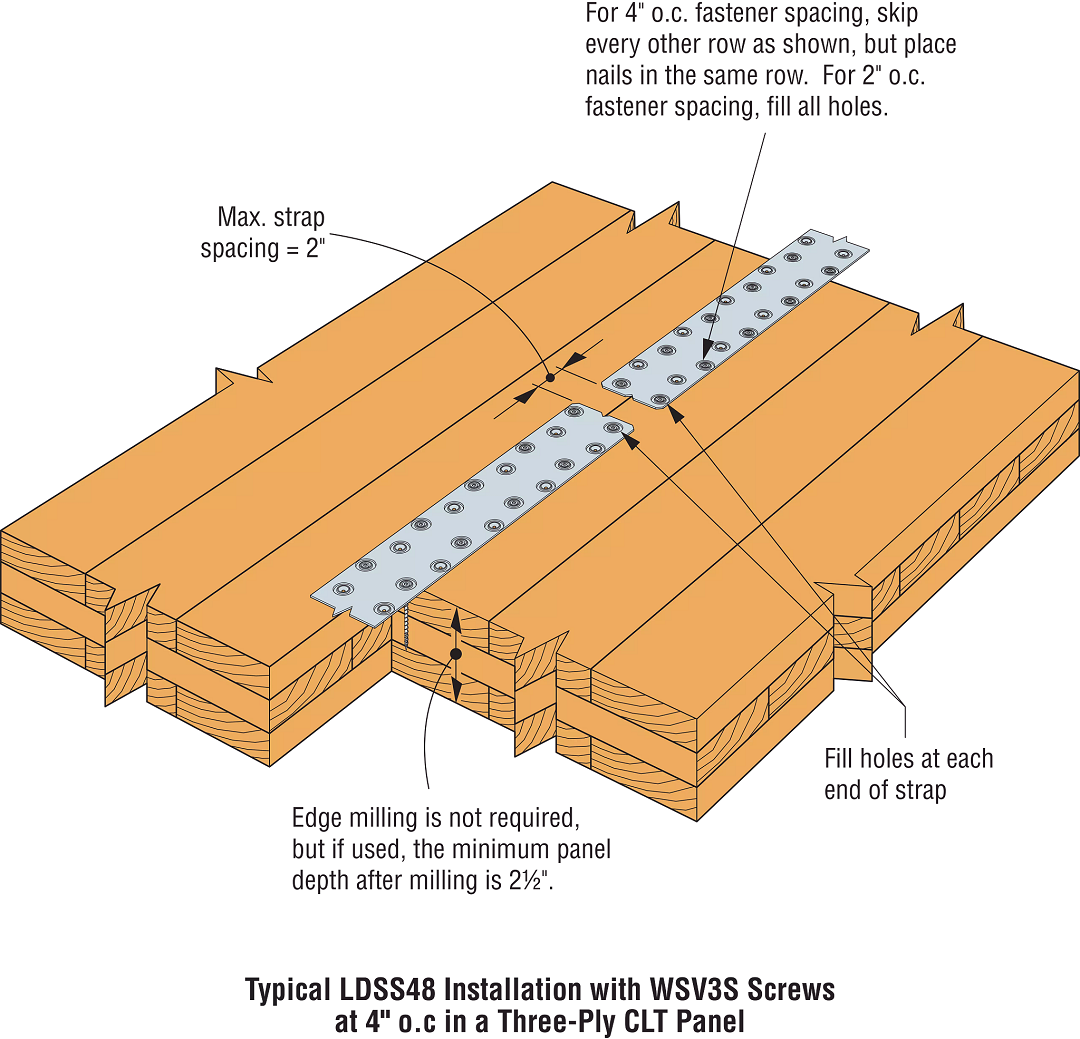
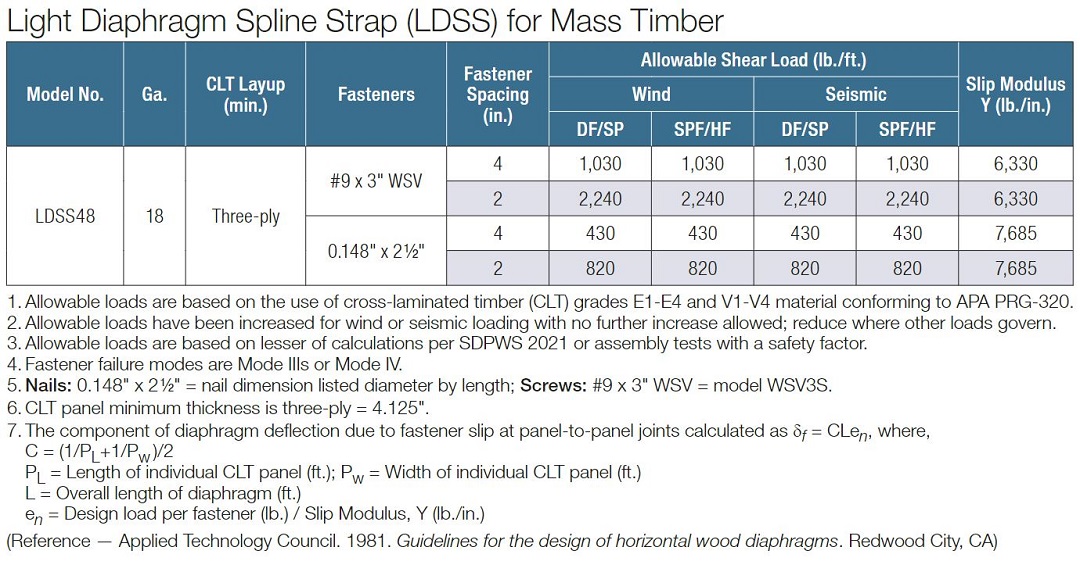