Simpson Strong-Tie has always been a leader in designing innovative products for various construction markets. As an R&D engineer, I enjoy the opportunities for continuous exploring, experimenting and learning that come with my role. There’s never a dull moment working in research and development! At present, I’m thrilled to be part of a team that works on developing products for construction using cross-laminated-timber (CLT) and other forms of mass timber. So I have the honor of introducing three amazing fastener products that are load rated for use in CLT, wood, glulam and structural composite lumber (SCL) products (e.g., LVL, PSL, LSL).
Author: Neelima Tapata
Screw Substitution Calculator Web App
At Simpson Strong-Tie, we do our best to offer tools that make your job easier. One such tool is the Screw Substitution Calculator. It’s a quick and easy-to-use web app created to help you calculate and design using Simpson Strong-Tie fasteners. The app can be used in two ways: (1) to design for a given load and (2) to provide a substitution for NDS fasteners. The app covers design for withdrawal loading, lateral loading and multi-ply connections. For each of these applications you can either design for a load or input the specified NDS fasteners and design an alternate Simpson Strong-Tie screw substitution. The app can generate detailed calculations in a PDF format for any of the selections made, and these calculations can be used for submittals.
Note that although the tool currently does not address corrosion issues, corrosion resistance should be an important consideration before selecting screws for your application.
Below is a screenshot of the Screw Substitution Calculator. As explained above, the app can design for
- Withdrawal Loading
- Lateral Loading
- Multi-Ply Connections
The input sections for Withdrawal Loading and Lateral Loading (parallel or perpendicular to grain) are similar. A screenshot of Lateral Load Parallel to Grain is shown below.
Step 1: General Information – In this section, you are requested to select either Fastener Substitution or a Load Entry. If you choose fastener substitution, the app will request in step 4, Fastener Information, that you enter the original fastener design. The fastener substitution calculator will provide Simpson Strong-Tie fastener alternatives for the NDS fasteners. The NDS fasteners covered in this app are bolts, lag screws, wood screws and nails.
If you choose Load Entry, you will notice that the Fastener Information step will disappear and no longer be available for input. Next, select a category from the Design Method section. Available options are Allowable Stress Design (ASD), Load and Resistance Factor Design (LRFD) and Not Specified, if you are not sure of the design method. If the Not Specified option is selected, the design assumes the Load and Resistance Factor Design method, and it further prompts you to answer a few more questions related to Wood Moisture Content, Connection Temperature and End Grain Insertion.
Step 2: Side Member – In this section, all the information regarding the side member is entered. You can either select a species from the drop-down list or enter the specific gravity of the member manually in the text box. The information button lists all the available specific gravities for wood species combinations from NDS. Then enter the (actual, not nominal) thickness of the side member.
Step 3: Main Member – Similar to step 2, enter all information regarding the main member.
Step 4: Fastener Information – If the Fastener Substitution option is selected in step 1, step 4 will require you to enter information about the NDS fasteners used in the initial design. Enter the fastener type (bolt, lag screw, screw or nail), along with its diameter and length. From the fastener option list you can either select one fastener substitute at a time for each NDS fastener or enter the number of rows and the spacing of NDS-designed fasteners to determine Simpson Strong-Tie fastener options and their spacing requirements.
Step 5: Factors – Enter all factors required for designing the connection. Information pertaining to each factor is provided by clicking the information (i) button. You can use this as a guide for entering the factors.
Once all the input is entered, click on the FASTENER SUBSTITUTION OPTIONS button.
Clicking FASTENER SUBSTITUTION OPTIONS reveals the available solutions. As a default, the All Types box is checked under Fastener Type, as shown above. You can refine the solutions by unchecking this box and selecting any of the specific fasteners listed – SDWH TIMBER-HEX Screw solutions, for example. On the right, the available solutions are displayed for selection. When a selection is made, the app displays all the input and output for that solution as shown in the screenshot below. You can also create a PDF copy for any of the solutions by clicking on CREATE PDF button.
For Multi-Ply Connections, the input for side members and main members is combined into Member Information as shown in the screenshot below. Once the input is entered, click the FASTENER SUBSTITUTION OPTIONS button to display results. Similar to withdrawal loading or lateral loading, you can create a PDF copy of the calculations.
Let’s design a 3-ply connection with (3) 2 x 12 DF members for a load of 1,000 plf.
By clicking FASTENER SUBSTITUTION OPTIONS, you can see all the available Simpson Strong-Tie fastener solutions. You can then select any of the options to generate detailed output. A screenshot of the output, solution and information regarding the selected fastener is displayed below. You can create a PDF copy of the solution by clicking the CREATE PDF button.
Now that you know how easy it is to design using our Screw Substitution Calculator, you can start using this tool for your future projects. We welcome your feedback on the features you find useful as well as on how we could make this program better suit your needs. Let us know in the comments below.
Coating Evaluation for Fasteners – Code-Approved and Alternative Coatings
Who likes red rust? No one I know! How do we avoid corroding of fasteners? Corrosion can be controlled or eliminated by providing a corrosion-resistant base metal or a protective finish or coating that is capable of withstanding the exposure environment. When fasteners get corroded, they not only look bad from outside but can also lose their load capacity. To ensure continued fastener performance, we have to control for corrosion. This blog focuses on evaluating the corrosion resistance of the fasteners.
What does the building code specify?
For use in preservative-treated wood, the IBC-2015 specifies fasteners that are hot-dipped galvanized, stainless steel, silicon bronze or copper. Section 2304.10.5.1 of IBC-2015 (Figure 1) covers fastener and connector requirements for preservative-treated wood (chemically treated wood). While chemically treated wood is part of the corrosion hazard, it is not the whole corrosion hazard. Weather exposure, airborne chemicals and other environmental conditions contribute to the corrosion hazard for metal hardware. In addition, the main issue with the code-referenced requirements for fasteners and connectors used with preservative-treated wood is that not all preservative treatments deliver the same corrosion hazard and not all fasteners can be hot-dip galvanized.
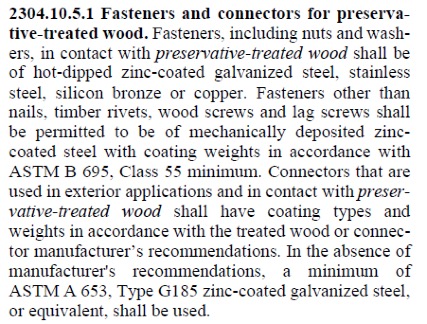
What if we want to use an alternative base material or coating for fasteners?
How do we evaluate the corrosion resistance of the alternative material or coating? The codes do not provide test methods to evaluate alternate materials and coatings. However, the International Code Council–Evaluation Service (ICC-ES) developed acceptance criteria to evaluate alternative coatings that are not code recognized for use in different environments. The purpose of acceptance criteria ICC-ES AC257, Acceptance Criteria for Corrosion-Resistant Fasteners and Evaluation of Corrosion Effects of Wood Treatment Chemicals, is twofold: (1) to establish requirements for evaluating the corrosion resistance of fasteners that are exposed to wood-treatment chemicals, weather and salt corrosion in coastal areas; and (2) to evaluate the corrosion effects of wood-treatment chemicals. In this blog post, we will concentrate on the evaluation of corrosion resistance of fasteners. The criteria provide a protocol to evaluate the corrosion resistance of fasteners where hot-dip galvanized fasteners serve as a performance benchmark. The fasteners evaluated by these criteria are nails or screws that are exposed directly to wood-treatment chemicals and that may be exposed to one or more corrosion accelerators like high humidity, elevated temperatures, high moisture or salt exposure.
The fasteners may be evaluated for any of the four exposure conditions:
- Exposure Condition 1 with high humidity. This test can be used to evaluate fasteners that could be exposed to high humidity. Typical applications that fall under this category are treated wood in dry-use applications.
- Exposure Condition 2 with untreated wood and salt water. This test can be used to evaluate fasteners that are above ground but exposed to coastal salt exposure.
- Exposure Condition 3 with chemically treated wood and moisture. This test covers all the general construction applications.
- Exposure Condition 4 with chemically treated wood and salt water. Typical applications include coastal construction applications.
Depending on the exposure condition being used for fastener evaluation, the fasteners are installed in wood that could be either chemically treated or untreated. Then the wood and the fasteners are placed in the chamber and artificially exposed to the evaluation environment. Two types of test procedures are to be completed for exposure condition 2 through 4. The purpose of these tests is not to predict the corrosion resistance of the coatings being evaluated, but to compare them to fasteners with the benchmark coating (ASTM A153, Class D) in side-by-side exposure to the accelerated corrosion environment.
ASTM B117 Continuous Salt-Spray Test
ASTM B117 is a continuous salt-spray test. For Exposure Condition 3, distilled water is used instead of salt water. The fasteners are continuously exposed to either moisture or salt spray in this test, and the test is run for about 1,440 hours after which the fasteners are evaluated for corrosion. This is an accelerated corrosion test that exposes the fasteners to a corrosive attack so the corrosion resistance of the coatings can be compared to a benchmark coating (hot-dip galvanized).
ASTM G85, Annex A5
The second test is ASTM G85, Annex A5 which is a cyclic test with alternate wet and dry cycles. The cycles are 1-hour dry-off and 1-hour fog alternatively. This is a cyclic accelerated corrosion test and relates more closely to real long-term exposure. This test is more representative of the actual environment than the continuous salt-spray test. As in the ASTM B117 test, the fasteners along with the wood are exposed to 1,440 hours, after which the corrosion on the fasteners is evaluated and compared to fasteners with the benchmark coating.
Test Method and Evaluation
The test process involves installing 10 benchmark fasteners along with 10 fasteners for each alternative coating being evaluated. The fasteners are arranged in the wood with a spacing of 12 times the fastener diameter between the fasteners. A kerf cut is provided in the wood between the fasteners to isolate the fasteners as shown in Figure 2 and to ensure elevated moisture content in the wood surrounding the fastener shank. The moisture and retention levels of the wood are measured, and the fasteners are then installed in the chamber as shown in Figure 3 and exposed to the designated condition. The test is run for the period specified, after which the fasteners are removed, cleaned and compared to the benchmark for corrosion evaluation. Figure 4 shows the wood and fastener heads after 1,440 hours (60 days). The heads and shanks of the fasteners are visually graded for corrosion in accordance with ASTM D610. If the alternate coating performs equivalent to or better than the benchmark coating — that is, if the corrosion is no greater than in the benchmark — then the coating has passed the test and can be used as an alternative to the code-approved coating. Figure 5 shows the benchmark and alternative fasteners that are removed from the chamber after 1,440 hours.
As you can see, the alternative coatings have to go through extended and rigorous testing and evaluation as part of the approval process before being specified for any of the fasteners. Some alternative coatings provide even better corrosion resistance than the code recognized options. Sometimes, also, the thickness of these alternative coatings may be smaller than the thick coating required for hot-dip galvanized parts. Some of our coatings, such as the Double-Barrier coating, the Quik Guard® coating and the ASTM B695 Class 55 Mechanically Galvanized have gone through this rigorous testing and have been approved for use in preservative-treated wood in the AC257 Exposure Conditions 1 and 3. In addition, these coatings have been qualified for use with chemical retentions that are typical of AWPA Use Category 4A – General Ground Contact. No salt is found in AC257 Exposure Conditions 1 and 3. Please refer to our Fastener Systems Catalog, C-F-14, pages 13–15 for corrosion recommendations and pages 16–17 for additional information on coatings.
What do you look for specifically in a fastener? Do you have a preference for a certain coating type or color? Let us know in the comments below!
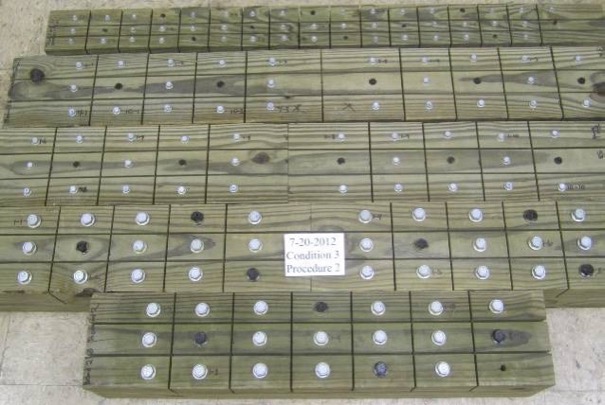
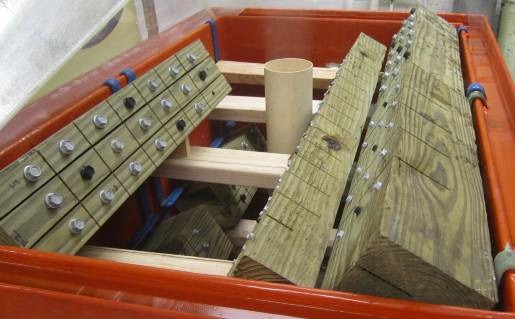
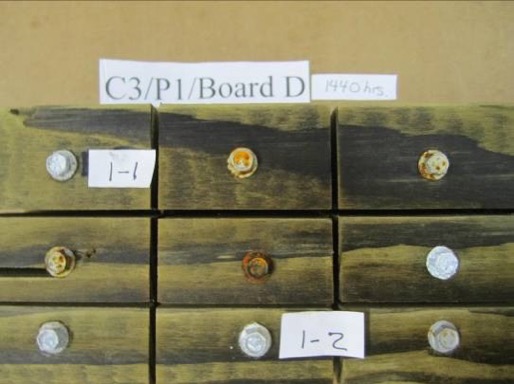

Specifying Self-Drilling Screws: “Standard” vs. “Engineered”
In my past life as a Design Engineer, when specifying a screw the size of the screw was the key feature that I considered. In my mind, a #10 screw performed better than #8, and a #12 was better than #10 and all #10 screws were the same. But that is not always true. Just as a shoe size or a dress size may not be exactly the same for all brands, a screw of the same size from different manufacturers may perform differently. The head type, head design, thread design (fine, coarse, thread angle, pitch), thread type (like box threads, buttress threads, unified, square) and drill point type (like #1, #3, #5 drill point) can influence the performance of a screw. When innovatively designed, a #10 engineered screw can meet or exceed the performance of a #12 or #14 screw in loads and drill time and could result in cost savings. You can use fewer screws, which would mean labor savings. For example, our newly designed XU34B1016 screw, which is a #10 screw with 16 threads per inch, a hex washer head and a #1 drill point, that performs better than a #14 standard screw in lighter gauge steels.
What Are Self-Drilling Tapping Screws?
Self-drilling tapping screws, or self-drilling screws, as the name implies, drill their own hole, eliminating the need for predrilling, and form or cut internal mating threads. They are relatively fast to instal compared to bolts or welds. Unlike pins, they do not require a thick support material to be used. They can be used in very thin steel, such as 26 gauge, up to steel that is ½” thick. Self-drilling screws may be a perfect choice for most applications involving cold-formed steel (CFS). They are most commonly used for CFS connections: either attaching CFS to CFS, wood to CFS or CFS to wood. They are a logical choice when the other side of the connection or material is not accessible.
Most self-drilling screws are made of steel wire that meets the specification of ASTM A510 minimum grade 1018 material as specified in ASTM C1513 standard. Self-drilling screws are heat treated to case harden then so that they meet the hardness, ductility, torsional strength and drill drive requirements as specified in ASTM C1513 standard. ASTM C1513 refers to SAE J78 for the dimensional and performance requirements of self-drilling screws.
Screw Selection
While selecting the screw, you need to figure out the head type that works for the application. For example, a flat-head screw would be a good choice for wood-to-steel applications, but for steel-to-steel applications, a hex head or a pan head may be a better choice. Similarly, the length of the screw should be sufficient to fasten the members of the connection together. According to Section D1.3 of AISI S200, the screw should be at least equal in length to the total thickness of the material including gaps with a minimum of three exposed threads. The length of the drill point is another important feature to consider. It should be long enough to drill through the entire thickness of the material before engaging the threads. This is because thread forming occurs with fewer revolutions than the drilling process. if the drill point length is not long enough, the screw threads can engage the connection material and the screw can bind and break.
Some drill points also have “wings” to drill a hole in the material that is larger in diameter than the threaded shank. Screws with this kind of point are mainly used for wood-to-steel applications. The blog post by Jeff Ellis titled “Wings or No Wings” provides some useful insights for screws with wings when used in shearwall applications.
The Test Standards and Evaluation Criteria for Standard and Engineered Screws
Per Section D1 of AISI S200, screws used for steel-to-steel connections or sheathing-to-steel connections shall be in compliance with ASTM C1513 or an approved design or design standard.
For ASTM C1513–compliant screws (per AISI S100), Section E4 provides equations to calculate shear, pullout and pullover of screws used in steel-to-steel connections. It also provides safety and resistance factors for calculating allowable strength or design strength. These equations are based on the results of tests done worldwide and the many different types of screws used in the tests. As a result, these equations seem to have a great degree of conservatism.
As discussed earlier, many factors, such as the head type and washer diameter, thread profile, drill point type and length, installation torque and the installation method affect or influence the performance of a screw. In order to qualify the screws as ASTM C1513–compliant or better performing, manufacturers need to have their screws evaluated per Acceptance criteria for Tapping Screw Fasteners AC118 developed by International Code Council – Evaluation Service. The criteria have different requirements depending on whether the intention is to qualify as standard screws or proprietary screws. For proprietary screws, connection shear, pullout and pullover tests are performed in accordance with the AISI S905 test method. The shear strength and tensile strength of the screw itself are evaluated per test standard AISI S904. The safety and resistance factors are calculated in accordance with Section F of AISI S100. The pictures below are some test set-ups per AISI S905 and AISI S904 test procedures.
Another important consideration is corrosion resistance. AC118 has a requirement for testing the fasteners for corrosion resistance in accordance with ASTM B117 for a minimum of 12 hours. The screws tested shall not show any white rust after 3 hours or any red rust after 12 hours of the test. At the same time, it is important to keep in mind that hardened screws are prone to hydrogen embrittlement and are not recommended for exterior or wet condition applications. Also, these screws are not recommended for use with dissimilar metals. If self-drilling screws are to be used in exterior environments, the screws need to be selectively heat treated to keep the core and surface hardness in a range that reduces the susceptibility to hydrogen embrittlement. Other fastener options for exterior environments are stainless-steel screws.
This table shows are some of our screw offerings for CFS applications. Our stainless-screw options can be found in Fastening Systems Catalog (C-F-14) or at www.strongtie.com.
What are the screws that you most commonly specify? Share your screw preferences and your ideas on self-drilling screws in your comments below.
Designing Built-Up Columns
Designing built-up columns? Now there’s a way to mechanically laminate multiple 2x members to meet the specifications in the National Design Specifications for wood. Simpson Strong-Tie evaluated Strong-Drive® SDW Truss-Ply screws for attaching multiple laminations with easier installation methods. With these screws, there’s no longer a need to nail from both sides of the column, or to use not-so-common 30d nails as specified in the NDS, or to pre-drill for bolts. Instead, installers can now install all the screws from one side of the built-up column, which provides time and cost savings.