I was driving under a concrete bridge one nice clear day in Chicago, and I happened to look up to see rusted rebar exposed below a concrete bridge. My beautiful wife, who is not a structural engineer, turned to me and asked, “What happened to that bridge?” I explained that there are many reasons why spalling occurs below a bridge. One common reason is the expansion of steel when it rusts or corrodes.
Tag: corrosion
Galvanic Corrosion
This week we are blogging about being “galvanic,” and we don’t mean with respect to people, but with respect to the corrosion that occurs between dissimilar metals.
Here is a question, and it is not a joke: What is one significant result that can occur when you have both electrochemical activity and intimate contact? The answer is galvanic corrosion.
Galvanic corrosion can take place when two or more metals of different electrochemical activity are in intimate contact in the presence of an electrolyte. The dissimilar metals form a galvanic couple, and with the aid of the electrolyte, a galvanic current flows between the metals of the galvanic couple. The more anodic metal corrodes in the presence of the more cathodic metal. In fastening systems, this can be a significant issue because the metal of the fastener often does not match that of the connection materials, making their electrochemical activity dissimilar.
Let’s examine the requirements for galvanic corrosion to occur.
First – In the most common instance, the metals are dissimilar, which means that the metals have different chemical potentials. You may be familiar with the galvanic series where metals are rated by their tendency to give up electrons in a salt-water solution. See Figure 1 for a chart of the galvanic series. The chart is structured with the most cathodic metals at the top and progresses to the most anodic at the bottom. The anodic index shown in the chart is normalized so that gold is the minimum numerical value, while zinc has the greatest numerical value. Stainless steel (300 series) is hidden in the terminology of “18% Chromium type corrosion-resistant steels.” In this chart, the stainless steel is assumed to be passivated.
Second – The metals must be in direct contact.
Third – An electrolyte must be present to facilitate the movement of electrons. The electrolyte in construction environments is usually plain water that occurs in the form of precipitation, condensation or water splash. Electrolytes that are solutions of chlorides (for example, salt water) are particularly effective electrolytes because they are more conductive.
The size of the anodic and cathodic parts can also be important in galvanic corrosion. If the anodic area is small relative to the cathodic exposed area, then the severity of the anodic corrosion is amplified. We can write an equation to explain the role of area in the galvanic process. We know that no corrosion will occur if the corrosion current density (icor) in μA/cm2 is the same for the anode (icor-a) and the cathode (icor-c). Here we are using a and c as subscripts to identify the anode and the cathode in the galvanic system. We know that current density is a function of total anodic current (I) in μA (where italicized A is amps), and the exposed area (A) is in cm2, which (according to ASTM G102-89) can be written as
icor = Icor/A
No galvanic corrosion transpires if icor-a for the anodic material is equivalent to icor-c of the cathodic material, which is to say Icor/Aa = Icor/Ac. However, when Ac ≠ Aa, then the corrosion function is not balanced, and relative areas can drive the severity of the galvanic reaction. Inasmuch as area can affect the galvanic process, it will help connection performance if the more anodic material is larger than the more cathodic material. And, by making the Aa>>Ac, we can arrest or minimize the galvanic process. Generally, this means it is best to have a fastener that is more cathodic than the materials being fastened.
We also know that the environment can affect galvanic activity. The differential in the anodic index of dissimilar metals is amplified in harsh environments, but in controlled environments, a greater differential in anodic index can be tolerated.
Let’s summarize some best fastening practices for preventing galvanic conditions that could undermine an otherwise good connection design (Claus, L. 2014. “Galvanic Corrosion.” Fastener Technology, April, pp. 64–66.):
- Use fasteners that are galvanically similar to the connection materials.
- Isolate the dissimilar materials by using a plastic washer or durable coating.
- Prevent entrapment of water or shield the connection from direct weather exposure.
- If the fasteners are dissimilar from the connection materials, choose a fastener that is cathodic relative to the connection materials.
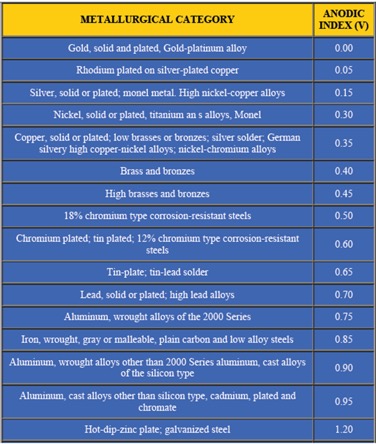
)
Some good information is available that can help to avoid a galvanic design challenge. First, see Figure 2. This chart provides color-coded galvanic compatibility that is fast and easy to use. The chart suggests material combinations where there will be galvanic action (red), material combination that might demonstrate galvanic activity (yellow), and material combinations that will have insignificant galvanic activity (green).
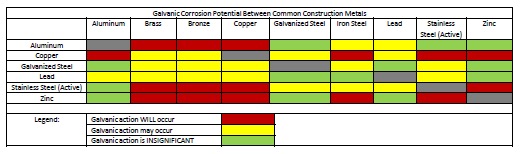
Then see Figure 3 because it gives more information about choices of materials for the fastener and connection materials. Here the probable results of galvanic corrosion to the fastener and base metals are described for various common combinations of common construction materials. It will help to explain which parts of the connection will be affected by galvanic corrosion and how severe the corrosion is likely to be.
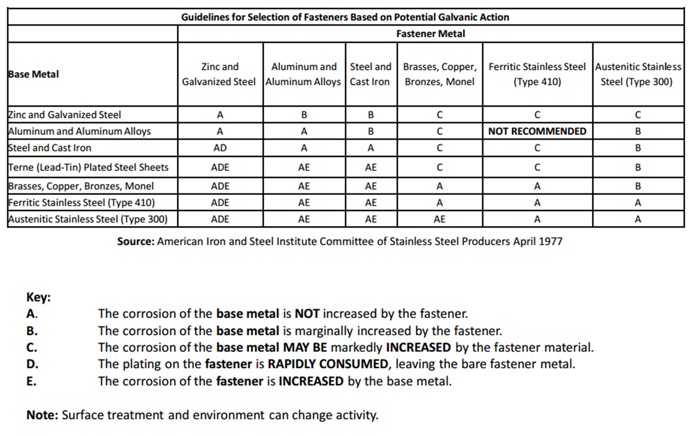
We know that you have many challenges when designing fastener connections, and it is our hope that this discussion helps you make informed choices when fastening dissimilar materials. Remember: Galvanic corrosion happens! Let us know if you have any comments.
Treated Lumber and Trusses (and the One Condition Under Which MPC Wood Trusses Shouldn’t Be Used)
What do a chicken house, a water treatment plant and a raised wood floor system all have in common? Very likely, they all involve preservative-treated lumber. They’re also all examples of common environments in which preservative-treated, metal-plate- connected (MPC) wood trusses may be specified.
Although trusses are successfully used in a variety of environments that require treated lumber, the first mention of “treated lumber” usually sends up a red flag in a truss design office. While the corrosion protection of truss plates is no different from the corrosion protection of any other steel fastener or hanger that comes in contact with treated lumber, there are a few more considerations that come into play whenever treated lumber is going to be used in a truss application.
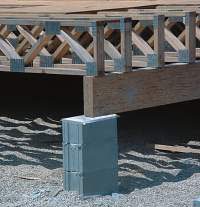
When fire-retardant-treated lumber or preservative-treated lumber is specified, the first (and easiest) step is to determine whether standard G60 truss plates are acceptable for use with the treated lumber, or whether the chemical treatment requires additional protection of the plates. Recent blog posts have discussed how fasteners are evaluated for corrosion resistance and how the Corrosion Resistance Classifications in our catalog help facilitate selection of hardware and fasteners for different types of treated wood and environmental conditions. Similar guidelines are also available for determining the proper metal connector plate for different wood treatments. For example, when using the sodium borate–based preservatives and fire retardants, standard G60 galvanized metal connector plates are acceptable. However, ammoniacal/alkaline/amine copper quaternary preservative types require more protection, such as G185, ASTM A153 galvanized- or stainless-steel truss plates. The complete guidelines – Quick Guide for Alternative Preservative Treatments with Metal Connector Plates – are available from the SBCA website.
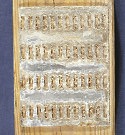
When trusses are used in particularly corrosive environments such as coastal environments or salt storage buildings, the ANSI/TPI 1 standard lists coatings that will provide increased corrosion protection for the plates (see insert, below).
The paint coating systems listed in (a) and (b) have been specified in the TPI standard since 1985. These paint coatings, which are applied to the truss plates after the trusses are manufactured, provide alternatives to the double-dipped galvanized or stainless-steel plates used in coastal high hazard areas. In fact, the ANSI/TPI 1 Commentary states that one study – SSPC Report 87-08, Evaluation of Coatings for Metal Connector Plates – concluded that the paint coating systems over standard galvanized plates would be expected to outperform the double-galvanized metal connector plates in field use.
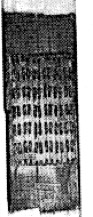
Once the necessary corrosion protection of the plates has been addressed, the next consideration is the effect of certain lumber treatments on the truss plates’ lateral resistance, or tooth-holding capacity. Fire-retardant treatments generally require strength reductions to be applied to both the lumber and metal connector plate design values. The proprietary treatment manufacturer specifies these design reductions. As soon as the specific treatment is known, the appropriate design reductions can be easily applied by the truss design software and noted on the truss design drawing accordingly.
Besides lumber treatment, there may be other reasons for plate design reductions whenever extra galvanization or special coatings are required. While extra galvanization itself does not necessarily require a reduction in plate values, if the treated lumber’s moisture content (MC) exceeds 19% at the time of truss fabrication, then a 20% reduction to the tooth-holding values is required. The same 20% reduction applies if the environment for the intended end use of the trusses is expected to result in wood moisture content exceeding 19%.
Special Considerations and Red Flags
One corrosive environment that requires special consideration is an enclosed swimming pool. ANSI/TPI 1 requires that trusses be separated from the pool environment by a vapor barrier and be separately ventilated from the pool environment. The exception to this requirement is if the truss plates are made with a stainless steel that is not susceptible to stress corrosion cracking (SCC), i.e., not Types 304 and 316. Since truss plates made with SCC-resistant stainless steel are not readily available (if at all), a vapor barrier is basically required anytime trusses are used over enclosed swimming pools.
Another important consideration in roof truss applications involving treated lumber is the effect of elevated temperatures. For example, when FRT lumber is going to be used in an environment where high moisture content will exist, an FRT formulated for exterior use may be specified. However, if the exterior FRT has not been tested with elevated temperatures as specified in TPI 1 Section 6.4.9.1, it should not be used in a roof application.
But the biggest concern when treated lumber is specified for use in metal-plate-connected wood trusses has nothing to do with corrosion at all. When a truss Designer gets a job that calls for a preservative treatment for exterior use or an exterior FRT, the very first question will be why is an exterior treatment required/what is the application? Although trusses can be adequately designed for many types of environments, there is one environment that does not mix well with metal-plate- connected wood trusses – exposed exterior applications. The TPI/WTCA Guidelines for Use of Alternative Preservative Treatments with Metal Connector Plates concludes with the following statement:
When trusses are exposed to repeated wetting and drying, the corresponding swelling/shrinkage of the wood causes what is commonly referred to as truss plate “back out”. Since the ability of a truss plate to provide lateral resistance depends on the teeth having adequate embedment into the wood members, any plate “back out” or withdrawal from the lumber due to weathering has an adverse effect on the load capacity of the truss plate.
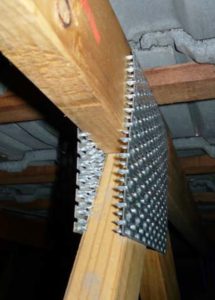
For this reason, MPC wood trusses must be protected from the elements, from the time they are built and stored through the extent of their life in service. High moisture content that is consistently high can be accounted for; but if the trusses will be exposed to moisture cycling, then it is time to consider something other than a metal-plate-connected wood truss.
What are your experiences with treated lumber and/or corrosive environments and wood trusses? Let us know in the comments section below.
Coating Evaluation for Fasteners – Code-Approved and Alternative Coatings
Who likes red rust? No one I know! How do we avoid corroding of fasteners? Corrosion can be controlled or eliminated by providing a corrosion-resistant base metal or a protective finish or coating that is capable of withstanding the exposure environment. When fasteners get corroded, they not only look bad from outside but can also lose their load capacity. To ensure continued fastener performance, we have to control for corrosion. This blog focuses on evaluating the corrosion resistance of the fasteners.
What does the building code specify?
For use in preservative-treated wood, the IBC-2015 specifies fasteners that are hot-dipped galvanized, stainless steel, silicon bronze or copper. Section 2304.10.5.1 of IBC-2015 (Figure 1) covers fastener and connector requirements for preservative-treated wood (chemically treated wood). While chemically treated wood is part of the corrosion hazard, it is not the whole corrosion hazard. Weather exposure, airborne chemicals and other environmental conditions contribute to the corrosion hazard for metal hardware. In addition, the main issue with the code-referenced requirements for fasteners and connectors used with preservative-treated wood is that not all preservative treatments deliver the same corrosion hazard and not all fasteners can be hot-dip galvanized.
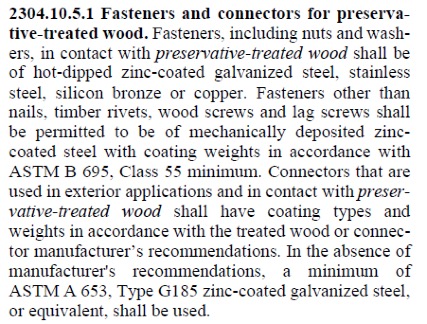
What if we want to use an alternative base material or coating for fasteners?
How do we evaluate the corrosion resistance of the alternative material or coating? The codes do not provide test methods to evaluate alternate materials and coatings. However, the International Code Council–Evaluation Service (ICC-ES) developed acceptance criteria to evaluate alternative coatings that are not code recognized for use in different environments. The purpose of acceptance criteria ICC-ES AC257, Acceptance Criteria for Corrosion-Resistant Fasteners and Evaluation of Corrosion Effects of Wood Treatment Chemicals, is twofold: (1) to establish requirements for evaluating the corrosion resistance of fasteners that are exposed to wood-treatment chemicals, weather and salt corrosion in coastal areas; and (2) to evaluate the corrosion effects of wood-treatment chemicals. In this blog post, we will concentrate on the evaluation of corrosion resistance of fasteners. The criteria provide a protocol to evaluate the corrosion resistance of fasteners where hot-dip galvanized fasteners serve as a performance benchmark. The fasteners evaluated by these criteria are nails or screws that are exposed directly to wood-treatment chemicals and that may be exposed to one or more corrosion accelerators like high humidity, elevated temperatures, high moisture or salt exposure.
The fasteners may be evaluated for any of the four exposure conditions:
- Exposure Condition 1 with high humidity. This test can be used to evaluate fasteners that could be exposed to high humidity. Typical applications that fall under this category are treated wood in dry-use applications.
- Exposure Condition 2 with untreated wood and salt water. This test can be used to evaluate fasteners that are above ground but exposed to coastal salt exposure.
- Exposure Condition 3 with chemically treated wood and moisture. This test covers all the general construction applications.
- Exposure Condition 4 with chemically treated wood and salt water. Typical applications include coastal construction applications.
Depending on the exposure condition being used for fastener evaluation, the fasteners are installed in wood that could be either chemically treated or untreated. Then the wood and the fasteners are placed in the chamber and artificially exposed to the evaluation environment. Two types of test procedures are to be completed for exposure condition 2 through 4. The purpose of these tests is not to predict the corrosion resistance of the coatings being evaluated, but to compare them to fasteners with the benchmark coating (ASTM A153, Class D) in side-by-side exposure to the accelerated corrosion environment.
ASTM B117 Continuous Salt-Spray Test
ASTM B117 is a continuous salt-spray test. For Exposure Condition 3, distilled water is used instead of salt water. The fasteners are continuously exposed to either moisture or salt spray in this test, and the test is run for about 1,440 hours after which the fasteners are evaluated for corrosion. This is an accelerated corrosion test that exposes the fasteners to a corrosive attack so the corrosion resistance of the coatings can be compared to a benchmark coating (hot-dip galvanized).
ASTM G85, Annex A5
The second test is ASTM G85, Annex A5 which is a cyclic test with alternate wet and dry cycles. The cycles are 1-hour dry-off and 1-hour fog alternatively. This is a cyclic accelerated corrosion test and relates more closely to real long-term exposure. This test is more representative of the actual environment than the continuous salt-spray test. As in the ASTM B117 test, the fasteners along with the wood are exposed to 1,440 hours, after which the corrosion on the fasteners is evaluated and compared to fasteners with the benchmark coating.
Test Method and Evaluation
The test process involves installing 10 benchmark fasteners along with 10 fasteners for each alternative coating being evaluated. The fasteners are arranged in the wood with a spacing of 12 times the fastener diameter between the fasteners. A kerf cut is provided in the wood between the fasteners to isolate the fasteners as shown in Figure 2 and to ensure elevated moisture content in the wood surrounding the fastener shank. The moisture and retention levels of the wood are measured, and the fasteners are then installed in the chamber as shown in Figure 3 and exposed to the designated condition. The test is run for the period specified, after which the fasteners are removed, cleaned and compared to the benchmark for corrosion evaluation. Figure 4 shows the wood and fastener heads after 1,440 hours (60 days). The heads and shanks of the fasteners are visually graded for corrosion in accordance with ASTM D610. If the alternate coating performs equivalent to or better than the benchmark coating — that is, if the corrosion is no greater than in the benchmark — then the coating has passed the test and can be used as an alternative to the code-approved coating. Figure 5 shows the benchmark and alternative fasteners that are removed from the chamber after 1,440 hours.
As you can see, the alternative coatings have to go through extended and rigorous testing and evaluation as part of the approval process before being specified for any of the fasteners. Some alternative coatings provide even better corrosion resistance than the code recognized options. Sometimes, also, the thickness of these alternative coatings may be smaller than the thick coating required for hot-dip galvanized parts. Some of our coatings, such as the Double-Barrier coating, the Quik Guard® coating and the ASTM B695 Class 55 Mechanically Galvanized have gone through this rigorous testing and have been approved for use in preservative-treated wood in the AC257 Exposure Conditions 1 and 3. In addition, these coatings have been qualified for use with chemical retentions that are typical of AWPA Use Category 4A – General Ground Contact. No salt is found in AC257 Exposure Conditions 1 and 3. Please refer to our Fastener Systems Catalog, C-F-14, pages 13–15 for corrosion recommendations and pages 16–17 for additional information on coatings.
What do you look for specifically in a fastener? Do you have a preference for a certain coating type or color? Let us know in the comments below!
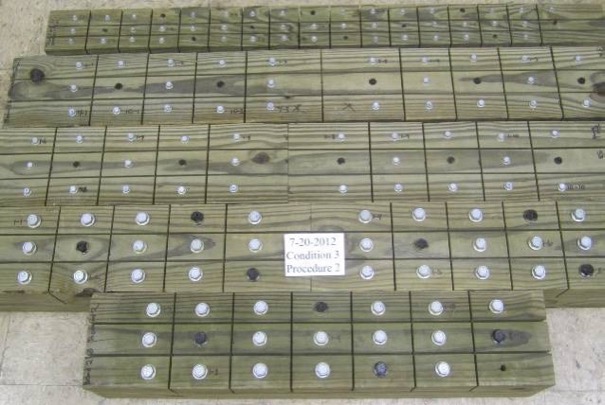
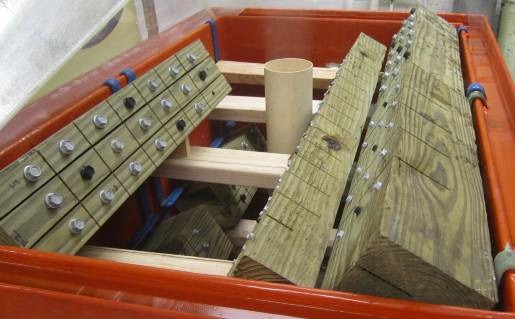
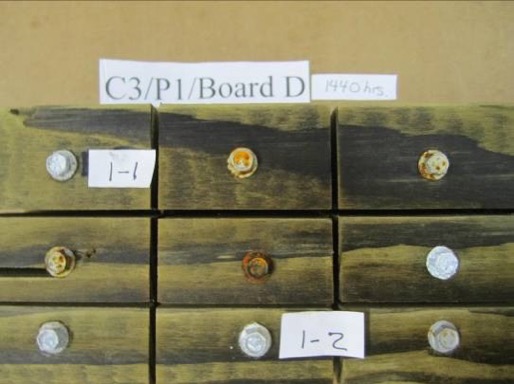

Corrosion Resistance Classification
This week we’re blogging about corrosion, and we’re not talking about rusting of the soul — we’re talking about oxidation of steel.
In 2014, we reviewed our corrosion protection recommendations for new catalog publications. In doing so, we realized that we could facilitate selection of hardware and fasteners if our Corrosion Resistance Classifications for treated wood were linked to common design conditions described in the codes. We made some revisions to our Corrosion Resistance Classifications during that exercise. This blog post talks about those changes and some current related activity in the wood treatment industry.
The common design conditions for corrosion-resistant wood construction include the wood materials with associated treatments and the environmental corrosion agents. The American Wood Protection Association (AWPA), which is an ANSI-accredited consensus standards organization, publishes the code-referenced standard, AWPA U1-15 Use Category System: User Specifications for Treated Wood.
When you specify treated wood, this is the standard that defines the appropriate treatment chemicals and chemical retentions depending on the exposure condition and bio-hazard, which the AWPA has summarized into a Use Category (UC) system. Figure 1 is a clip from the AWPA web site that gives a glimpse at the UC system. As the UC rating increases from UC1 to UC5, the chemical retention increases because the bio-hazard is increasing. Corrosion hazards are directly related to the combination of treatment chemical, treatment chemical retention and use environment.
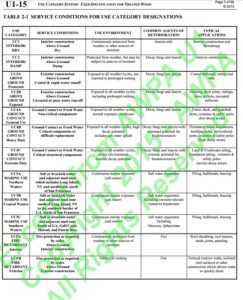
The AWPA UC system does not include environmental corrosion agents. As a result, we had to separately integrate those with treatment chemical effects as we developed the corrosion resistance classifications.
Finally, one more evaluation system had to be addressed: the exposure conditions of ICC-ES AC257 — Corrosion Resistant Fasteners and Evaluation of Corrosion Effects of Wood Treatment Chemicals. In the end, we developed Corrosion Resistance Classifications that considered the AWPA Use Categories, environmental corrosion agents and the ICC-ES AC257 exposure conditions.
Some of you may be thinking that we have not mentioned another aspect of corrosion — galvanic corrosion. Galvanic corrosion results when metals with dissimilar electrical potentials are placed in contact in the presence of an electrolyte (water). We’ll take up galvanic corrosion in a subsequent blog post.
Our basic Corrosion Resistance Classification table is shown in Figure 2.
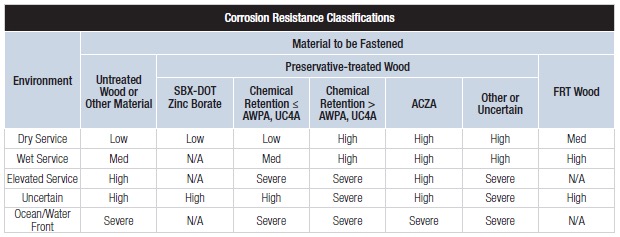
The ratings shown in the table — Low, Medium, High and Severe — refer to the corrosion resistance of Simpson Strong-Tie coating systems and base metals. An example of a coating system that is rated “Low” is paint or electro-galvanized zinc. An example of a material rated for “Severe” corrosion conditions is Type 316 stainless steel.
To use the Corrosion Resistance Classifications table, find the Environment, then move to the correct column in the Material to Be Fastened section; identify a rating. Then look in the companion table labeled “Corrosion Resistance Recommendations” to identify a coating or base metal that is appropriate for your project. Be sure to read the table notes to the Corrosion Resistance Classifications for exceptions and limitations. We implemented this system to simplify product selection. Let’s take a look at each aspect that contributes to the Corrosion Resistance Classifications table.
Environment
The environment captures the moisture, atmospheric conditions and other elements that affect corrosion rate. “Dry Service” usually means an interior space with low moisture content or dampness. No liquid water is present in this sort of environment. The absence of moisture limits the electrochemical reaction needed to produce what we see as corrosion. “Wet Service” usually means exterior exposure and involves liquid water as direct exposure or condensation and wood moisture contents that can exceed air-dry conditions and may be temporary or persist for prolonged periods. We incorporated environmental agents with the “Elevated Service and Ocean/Waterfront” conditions. These environmental agents include fumes, acid rain, airborne salinity, etc. The “Uncertain Environment” was included for the Designer who does not know the corrosive conditions in service.
Material Being Fastened
Here we distinguish between clean materials and wood treated with chemicals — wood preservatives or fire-retardant chemicals (FRT). Untreated softwoods used for framing are generally not significantly corrosive. This does not include cedars and redwood, which are a special case. Cedars tend to be corrosive and particularly prone to staining when fastened with carbon steel hardware and fasteners. As a result, our recommendations for untreated softwoods are generally a function of the environment — moisture, weather exposure and corrosion agents such as salt spray, sulfur or fertilizer fumes and acid rain are all examples.
Some treatment chemicals do not significantly increase the corrosion hazard. These are the SBX-DOT treatment chemicals (inorganic boron and borate treatments). These are not typically used in exterior environments or for high-moisture conditions. The preservatives are not chemically bound to the wood and they can leach out under exposure to liquid moisture, which would leave the wood unprotected. The corrosion hazard attendant to these chemicals is similar to that of untreated wood and the codes permit the use of bare carbon steel in contact with wood treated with these chemicals (IBC2015, Section 2304.10.5.1 and IRC2015, Section R317.3.1 (exception 3)).
Most of the waterborne chemicals in common use contribute to an elevated corrosion hazard. Some of the common wood treatment chemicals include formulations of alkaline copper quaternary (ACQ), copper azole (CA), ammoniacal copper zinc arsenate (ACZA) and micronized copper azole (MCA). The AWPA UC system defines the exposure conditions for each Use Category as well as the chemical retention required to prevent a decay failure. The MCA formulations are alternatives to those specified in the code-referenced standard through the evaluation report process and are not standardized by the AWPA. The evaluation report process for wood preservatives requires the submission of evidence in compliance with ICC-ES AC326 — Proprietary Wood Preservative Systems — Common Requirements for Treatment Process, Test Methods and Performance.
We realize that UC4A is a general-use ground-contact condition, and further, it is the maximum necessary specification for treated wood in many building applications. The Simpson Strong-Tie Corrosion Resistance Classifications recognize that the corrosion hazard of treatment chemical retentions for UC4A in Wet Service is a “Medium” corrosion condition (with the exception of ACZA, which is rated “High” in Wet Service). This means that carbon steel products with sufficient corrosion resistance (e.g., ZMAX, double barrier coating, etc.) can be used in these conditions assuming no other corrosion-causing agents are present.
On the other hand, the moisture conditions and treatment chemical retentions are elevated in UC4B and UC4C, and there is also a potential for salt exposure, which further escalates the corrosion hazard. In these conditions, stainless steel is generally recommended for connectors and fasteners as the best material for mitigating the corrosion risk.
The last column in the Corrosion Resistance Classifications table is devoted to FRT wood. Fire-retardant treatment chemicals are proprietary and are deemed to meet the requirements of the codes through the evaluation report process (ICC-ES AC66 — Acceptance Criteria for Fire-Retardant-Treated Wood). We cannot evaluate the corrosion resistance of hardware to all of the FRT formulations. However, we have reviewed most of the FRT evaluation reports for corrosion information. The corrosion effects of FRT chemicals, like preservative treatment chemicals, are minimized in dry-service conditions because the electrochemical reaction cannot progress or is slowed without an electrolyte. The Corrosion Resistance Classifications reflect that information. The Designer should always follow the FRT evaluation reports in addition to considering our recommendations.
It is important to note that the Corrosion Resistance Classifications are not associated with specific applications. Rather, the ratings are based on the integrated effects of the environment and the wood treatment where the chemical retentions given in the AWPA Use Category system play an important role in the ratings. This makes it relatively straightforward to select hardware that is adequate for a design environment.
Changes to the AWPA U1 Standard and Effects on Corrosion Resistance Classifications
As noted here and in the online JLC article, wood preservative chemicals can achieve compliance with the codes by either of two methods:
- The product is a generic product (e.g., ACQ-D or CA-B) and is listed in the AWPA U1 standard; or
- The product has an evaluation report obtained by submitting evidence in accordance with ICC-ES AC326 — Proprietary Wood Preservative Systems — Common Requirements for Treatment Process, Test Methods and Performance.
You may be aware that the AWPA is revising its code-referenced standard, AWPA U1-15, Use Category System: User Specification for Treated Wood. The consensus process is ongoing and is not complete. However, AWPA member chemical companies (Viance, Koppers, and Arch) have placed information in the market. In parallel with the AWPA, ICC-ES has modified AC326 to reflect the changes ongoing in the AWPA U1 standard. Simpson Strong-Tie has been in contact with the AWPA, other industry associations and industry professionals to understand the potential effects on metal hardware of the AWPA U1 and ICC-ES AC326 revisions.
The proposed revisions to the AWPA U1 standard modify the definitions for UC3A, UC3B, UC4A, UC4B and UC4C. The most important revisions are to UC3B and UC4A. The new definition for applications in UC3B suggests that beams and joists in decks and docks may have bio-hazards that exceed the UC3B assumptions, while the new UC4A definition will include above-ground applications with ground- contact hazards. The revised AWPA U1 standard will be published in the May–June 2016 time frame; AWPA U1-16 will be included in the 2018 codes.
The revision to ICC-ES AC326 also modifies the definitions for UC3B, UC4A and UC4B. ICC-ES AC326 has an implementation date of July 2016, which will cause some changes to specifications this summer. Micronized copper azole (MCA) formulations are the most common treatment chemicals that will be affected by this action.
Revisions to the Use Category definitions are being driven by two issues:
- Wood treated for UC3 is sometimes used in near-ground applications where the bio-hazard is more like UC4.
- Under-treatment compromises the margin of safety to bio-hazards, which can lead to decay failures.
Rather than revisit the retention specifications in AWPA U1 standard, the AWPA is modifying the definitions for the Use Categories that are involved, and that language has been carried into ICC-ES AC326 to ensure that the two systems are consistent with each other. The result of changes to the Use Category definitions will likely cause some specifications to change from UC3B to UC4A or from UC4A to UC4B. The main effects will likely be to specifications in eastern and southern states, where there may be more chemical in the wood to meet retention specifications.
The Simpson Strong-Tie Corrosion Resistance Classifications make specific reference to the corrosive levels of environmental conditions and the chemical treatment and retentions of the AWPA Use Categories, not to applications. As a result, the AWPA U1 revisions and the parallel changes to ICC-ES AC326 will not necessitate a change in our corrosion recommendations, because the chemical retentions for each Use Category have not changed. However, your hardware specifications could change for typical applications depending on the Use Category of the treated wood in your project. Our information suggests that this issue is still not settled within the industry, and we will pass along information as we learn it.
Simpson Strong-Tie is currently preparing new catalogs for the coming year and will be updating the corrosion information in those publications and our website. We’re interested in your experience with our Corrosion Resistance Classifications and whether you have suggestions for how we might make the content more useful to you.
Connectors and Fasteners in Fire-Retardant-Treated Wood
In any given year, Simpson Strong-Tie fields several questions about the use of our connectors and fasteners with pressure-treated fire-retardant wood products. Most often asked is whether this application meets the building code requirements for Type III construction, and whether there is a legitimate concern about corrosion. While there haven’t been any specific discussions on this topic in the SE Blog, there have been related discussions surrounding sources of corrosion, such as: Corrosion: The Issues, Code Requirements, Research and Solutions, Corrosion in Coastal Environments, Deck Fasteners – Deck Board to Framing Attachments. This post will explore several resources that we hope will enable you to make an informed decision about which type of pressure-treated Fire-Retardant-Treated Wood (FRTW) to choose for use with steel fasteners and connectors.
One factor contributing to the frequency of these questions is the increased height of buildings now being constructed. With increased height, there is a requirement for increased fire rating. To meet the minimum fire rating for taller buildings, the building code requires noncombustible construction for the exterior walls. As an exception to using noncombustible construction, the 2015 International Building Code (IBC®) section 602.3 allows the use of fire-retardant wood framing complying with IBC section 2303.2. This allows the use of wood-framed construction where noncombustible materials would otherwise be required.
In the 2009 IBC, Section 2304.9.5, “Fasteners in preservative-treated and fire-retardant-treated wood,” was revised to include many subsections (2304.9.5.1 through 2304.9.5.4) dealing with these wood treatments in various types of environmental applications. Section 2304.9.5.3 addressed the use of FRTW in exterior applications or wet or damp locations, and 2304.9.5.4 addressed FRTW in interior applications. These sections carried over to the 2012 IBC, and were moved to Section 2304.10.5 in the 2015 IBC. FRTW is listed in various other sections within the code. For more information about FRTW within the code (e.g., strength adjustments, testing, wood structural panels, moisture content), the Western Wood Preservers Institute has a couple of documents to consult: 2009 IBC Document and 2013 CBC Document. They also have a number of different links to various wood associations.
As shown in Figure 1 below, fasteners (including nuts and washers) used with FRTW in exterior conditions or where the wood’s service condition may include wet or damp locations need to be hot-dipped zinc-coated galvanized steel, stainless steel, silicon bronze or copper. This section does permit other fasteners (excluding nails, wood screws, timber rivets and lag screws) to be mechanically galvanized in accordance with ASTM B 695, Class 55 at a minimum. As shown in Figure 2, fasteners (including nuts and washers) used with FRTW in interior conditions need to be in accordance with the manufacturer’s recommendations, or, if no recommendations are present, to comply with 2304.9.5.3.
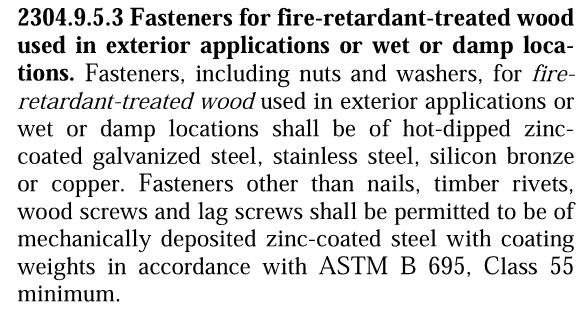
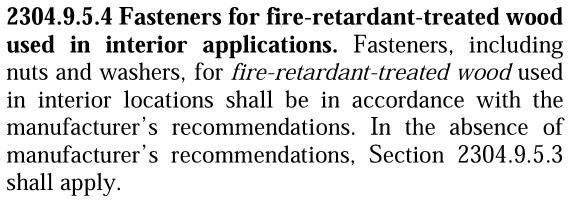
In Type III construction where the exterior walls may be FRTW in accordance with 2012 IBC Section 602.3, one question that often comes up is whether the defined “exterior wall” should comply with Section 2304.9.5.3 or 2304.9.5.4. While there are many different views on this point, it is our opinion at Simpson Strong-Tie that Section 2304.9.5.4 would apply to the exterior walls. Since the exterior finishes of the building envelope are intended to protect the wood and components within its cavity from exterior elements such as rain or moisture, the inside of the wall would be dry.
There are many FRTW product choices on the market; take a look at the American Wood Council’s list of treaters. Unlike the preservative-treated wood industry, however, the FRTW industry involves proprietary formulations and retentions. As a result, Simpson Strong-Tie has not evaluated the FRTW products. In our current connector and fastener catalogs, C-C-2015 Wood Connector Construction and C-F-14 Fastening Systems, you will find a newly revised Corrosion Resistance Classifications chart, shown in Figure 3 below, which can be found on page 15 in each catalog. The FRTW classification has been added to the chart in the last column. The corrosion protection recommendations for FRTW in various environmental applications is set to medium or high, corresponding to a number of options for connectors and fasteners as shown in the Corrosion Resistance Recommendations chart, shown in Figure 4. These general guideline recommendations are set to these levels for two reasons: (1) there are unknown variations of chemicals commercially available on the market, and (2) Simpson Strong-Tie has not conducted testing of these treated wood components.
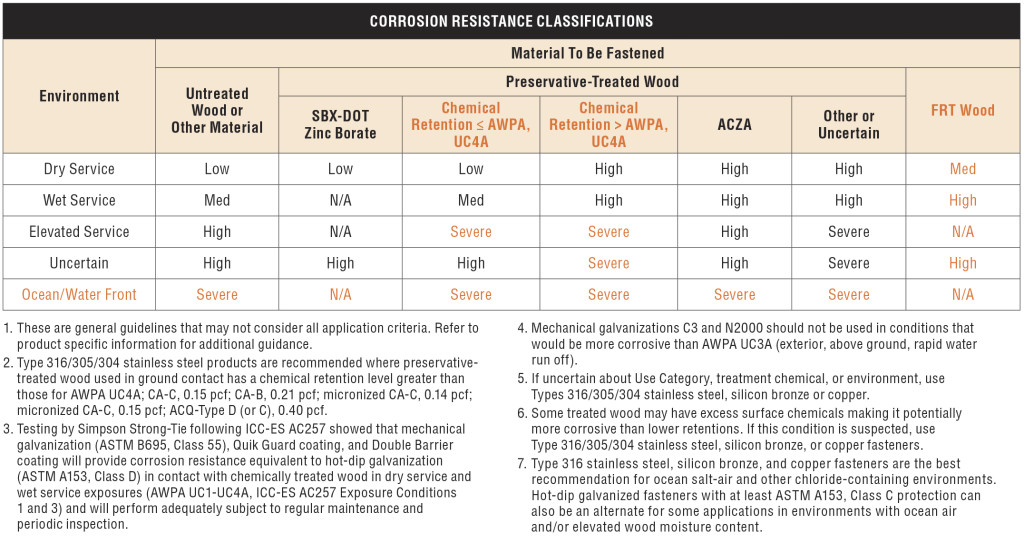
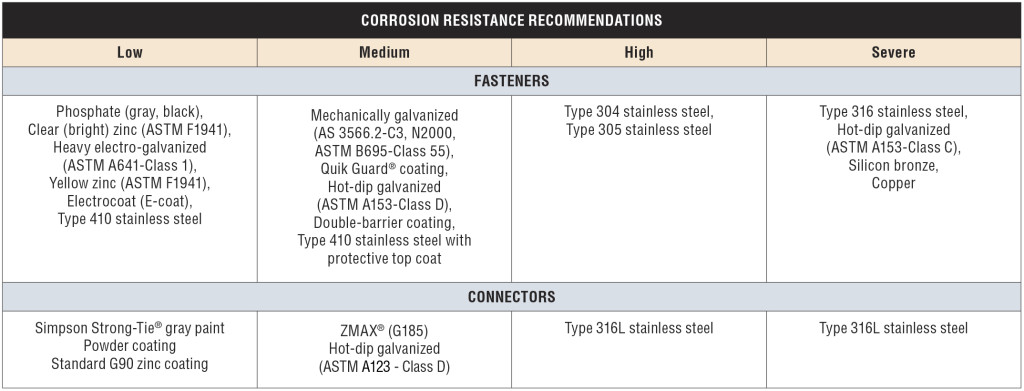
The information above is not the only information readily available. There are many different tests that can be done on FRTW, as noted in the Western Wood Preservers Institute’s document. One such test for corrosion is Military Specification MIL-1914E, which deals with lumber and plywood. Another is AWPA E12-08, Standard Method of Determining Corrosion of Metals in Contact with Treated Wood. Manufacturers of FRTW products who applied for and received an ICC-ES Evaluation Report must submit the results of testing for their specific chemicals in contact with various types of steel. ICC-ES Acceptance Criteria 66 (AC66), the Acceptance Criteria for Fire-Retardant-Treated Wood, requires applicants to submit information regarding the FRTW product in contact with metal. The result is a section published in each manufacturer’s evaluation report (typically Section 3.4) addressing the product use in contact with metal. Many published reports contain similar language, such as “The corrosion rate of aluminum, carbon steel, galvanized steel, copper or red brass in contact with wood is not increased by (name of manufacturer) fire-retardant treatment when the product is used as recommended by the manufacturer.” Structural engineers should check the architect’s specification on this type of material. Product evaluation reports should also be checked to ensure proper specification of hardware and fastener coatings to protect against corrosion. Each evaluation report also contains the applicable strength adjustment factors, which vary from one product to another.
Selecting the proper FRTW product for use in your building is crucial. There are many different options available. Be sure to select a product based on the published information and to communicate that information to the entire design team. Evaluation reports are a great source of information because the independently witnessed testing of manufacturers has been reviewed by the agency reviewing the report. Finally, understanding FRTW chemicals and their behavior when in contact with other building products will ensure expected performance of your structures.
What has been your experience with FRTW? What minimum recommendations do you provide in your construction documents?
Corrosion: The Issues, Code Requirements, Research and Solutions
When you hear $452 billion, what comes to mind? Perhaps the annual state budgets of California, Texas, Florida or New York? Maybe the combined net worth of Bill Gates, Larry Ellison, or the Walton Family? While those would be good guesses, I bet you didn’t think of corrosion! According to a May 2012 Congressional Briefing hosted by NACE International and ASM International, corrosion-related costs are a staggering 3.1% of the U.S. GDP, which is more than the individual budgets of those states above, and the combined net worth of the top 15 people listed on the Forbes 400: The Richest People in America.
Corrosion of metallic surfaces is an electrochemical process typically involving an anode, electrolyte and a cathode. An anode is a metal zone which loses electrons when exposed to an electrolyte, an electrolyte is a non-metal electrical conductor, and a cathode is the zone where an oxidizing agent (e.g., oxygen) gains the electrons. While there are many different forms of corrosion (e.g., pitting, intergranular, wet storage stain, etc.), and various sources of causes (e.g., treated lumber, moisture level, temperature, atmosphere, air quality, etc.), other factors such as exposure related to time of wetness are equally important. In a study presented in Dr. X.G. Zhang’s book Corrosion and Electrochemistry of Zinc, time of wetness is 50% greater near the top of a structure compared to the bottom, leading to greater corrosion.
Corrosion in Coastal Environments
“An ounce of prevention is worth a pound of cure”
– Benjamin Franklin
Any contractor that has ever had to replace a corroded connector or fastener will tell you this quote is an understatement. Here at Simpson Strong-Tie, we spend a lot of time refining new product designs to simplify their installation, but uninstalling a joist hanger? It never crosses our minds, and it shows by looking at all the tools you would need: claw hammer, cat’s paw, reciprocating saw, and the all-important first aid kit.
But luckily for the project owner, an ounce of prevention only costs about the price of half a pound of cure. Stainless steel connectors and fasteners are in the range of 5-10 times the cost of galvanized steel. However, connections are usually only a small part of a project’s overall budget and are a critical part of the load path, so the argument for stainless steel is an easy one to make.