As a Composite Strengthening Systems™ Field Engineer at Simpson Strong-Tie, I’ve supported many composite strengthening projects from design through construction and had hands-on experience troubleshooting issues with FRP witness panels. Through these experiences, I’ve learned a few lessons and developed some best practices worth sharing with anyone in the engineering and construction communities who may encounter similar issues.
Tag: fiber reinforced polymer
Simpson Strong-Tie and Structural Technologies Offer Workshop on Seismic Strengthening Solutions for Concrete, CMU and URM
Did you know that Simpson Strong-Tie offers free education and training to the structural engineering and building industries? On May 18, 2022, a team of Simpson engineers and technical sales reps, in conjunction with Structural Technologies, hosted a workshop in Portland on fiber-reinforced polymer (FRP) and fabric-reinforced cementitious matrix (FRCM) seismic strengthening solutions for concrete, reinforced masonry and unreinforced masonry structures. The workshop educated engineers on how Composite Strengthening Systems™ (our FRP and FRCM solutions) can be used to strengthen structural concrete and masonry elements in their projects. This was our first workshop event since COVID restrictions were placed, and we were excited to host the industry again.
Project Profile: Reinforcing Concrete Joists to Increase Load Rating
We’re excited to share another fiber-reinforced polymer (FRP) project that required both flexural and shear strengthening (photo below) of reinforced concrete joists to enable the slab floors to carry more live load. The structure is in Southern California, and appears to have been built in the 1950s or 1960s when pan joist construction was common. The EOR for this project, Structural Focus, is an experienced structural engineering firm known for seismic retrofit solutions. The FRP applicator was FD Thomas Structural Specialties, a contractor with decades of FRP installation experience.
Case Study: Gruening Middle School’s Seismic Damage Repair Solution
It can be a challenge to repair an earthquake-damaged structure.
During the 7.1-magnitude 2018 Anchorage earthquake, Gruening Middle School in Eagle River sustained more damage than any other school in the Anchorage School District. Review of the school showed the existing masonry walls suffered damage and separation from the roof. During the retrofit design, the Reid Middleton structural engineering team (Anchorage) determined the masonry walls weren’t adequately reinforced to meet current code requirements. They were seeking an easy-to-install strengthening solution that wouldn’t add significant weight to the building.
A New Way to See Whether FRP Is Right for Your Project
Specifying our Composite Strengthening Systems™ (CSS) is unlike choosing any other product we offer. In light of the unique variables involved with selecting and using fiber-reinforced polymer (FRP) solutions, we encourage you to leverage our expertise to help with your FRP strengthening designs. To get started, we first need to determine whether FRP is right for your project. The fastest way to do that is for you to fill out our FRP Design Questionnaire. Our new Excel-based questionnaire collects your project information and helps you use the existing capacity check to evaluate whether or not FRP is suitable for your project per the requirements of ACI 562-16 Section 5.5.2. After the feasibility study, the questionnaire creates input sheets specifically for your project.
Continue Reading
4 Common FRP Myths and Misconceptions: The Stuff Not Everyone Talks About
The primary benefit of fiber-reinforced polymer (FRP) systems as compared with traditional retrofit methods is that significant flexural, axial or shear strength gains can be realized using an easy-to-apply composite that does not add significant weight or section to the structure. Many times it is the most economical choice given the reduced preparation and labor costs and may be installed without taking the structure out of service. However, it is important to make sure the composite is properly designed following industry standards in order to ensure that it is the right product for the application.
To provide you with a better understanding of the topic, it’s important to dispel some common myths and misconceptions that you might hear about FRP:
FRP Concrete Strengthening – Five Case Studies
Fiber-reinforced polymer (FRP) composite systems can be used to strengthen walls, slabs and other concrete or masonry members in buildings and other structures. The case studies below show ways in which Composite Strengthening Systems™ (CSS) provide valuable solutions for strengthening buildings and other structures for our customers.
Residential Project in San Francisco
The homeowner for this project wanted to repair some spalling concrete on his concrete piers and also wrap the piers with FRP. We worked with the contractor and homeowner to design a cost-effective solution. This was a successful project for all involved, since the alternative was to jacket the piers with costly and unsightly steel jackets.
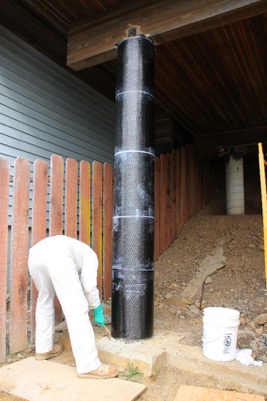
School Project in Argentina
The goal of the project was to analyze a standard design of approximately 400 schools in Argentina that were built in the 1980s and to make recommendations to retrofit the structures to meet current seismic code requirements. On analysis, it was found that columns were in need of shear reinforcement for the schools to meet the new seismic requirements.
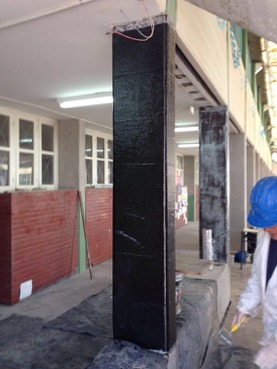
Hospital Project in Butler, PA
The Engineer of Record on this project wanted to provide continuity across the slab construction joints, something which the existing rebar did not provide. We provided a design of Near-Surface-Mounted (NSM) laminates, which are installed in saw-cut grooves in the top of the concrete slab. This installation allows a flush finished surface, important for allowing the floor finishes to be installed on the slab.
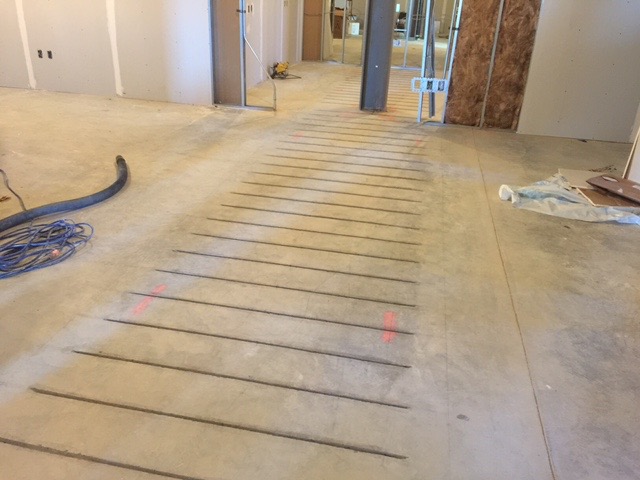
Silo Project in Garden City, IA
The concrete silos on this project had spalling at the top portion, which caused a hazard at this site. After repairing the concrete, we provided a ring of carbon fabric to assist in keeping the top concrete of the silos solid for years to come.
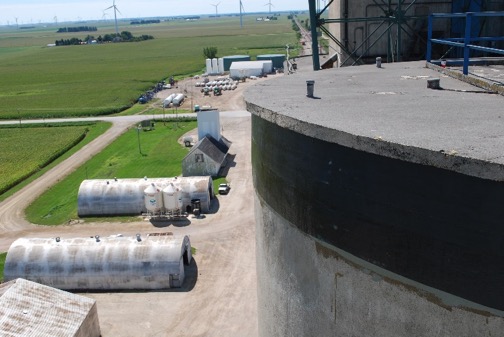
Bridge Project in MN
MNDOT wanted to gain experience working with our CSS products on one of their bridges. We worked with their staff to design several types of strengthening solutions for bridge pier caps and columns. We then provided onsite installation training for the MNDOT maintenance staff to install the FRP products on the bridge.
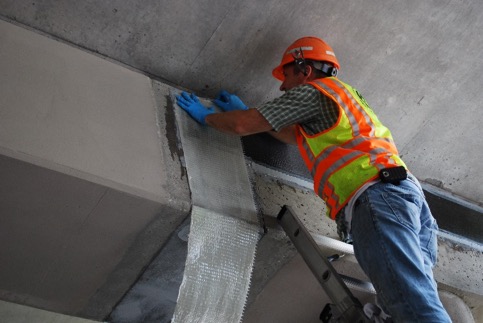
We recognize that specifying Simpson Strong-Tie® Composite Strengthening Systems™ is unlike choosing any other product we offer. Leverage our expertise to help with your FRP strengthening designs. Our experienced technical representatives and licensed professional engineers provide complimentary design services and support – serving as your partner throughout the entire project cycle. Since no two buildings are alike, each project is optimally designed to the Designer’s individual specifications. Our pledge is to address your specific condition with a complete strengthening plan tailored to your needs, while minimizing downtime or loss of use, at the lowest possible installed cost.
Your Partner During the Project Design Phase
During the Designer’s initial evaluation or preparation of the construction documents, Simpson Strong-Tie can be contacted to help create the most cost-effective customized solution. These plans include detailed design calculations for each strengthening requirement and design drawings with all the necessary details to install the CSS system. Simpson Strong-Tie Engineering Services will work closely with the Design Engineer to provide all the necessary information required to design the system.
Why Use Our Design Services?
- Assess feasibility studies to ensure suitable solutions to your application
- Receive customized FRP strengthening solutions
- Work with our trained contractor partners to provide rough-order-of-magnitude (ROM) budget estimates
- Collaborate during the project design phase
- Receive a full set of drawings and calculations to add to your submittal
- Maintain the flexibility to provide the most cost-effective solution for your project
- Gain trusted technical expertise in critical FRP design considerations
Learn more: Webinar – Introducing Fabric-Reinforced Cementitious Matrix (FRCM)
In this free webinar we dive into some very important considerations including the latest industry standards, material properties and key governing limits when designing with FRCM.
Continuing education credits will be offered for this webinar.
Participants can earn one professional development hour (PDH) or 0.1 continuing education unit (CEU).
For complete information regarding specific products suitable to your unique situation or condition, please visit strongtie.com/css or call your local Simpson Strong-Tie RPS specialist at (800) 999-5099.
Fiber Reinforced Polymer (FRP) Design Example
The following FRP Design example walks the reader through the typical process for designing an FRP strengthening solution for a concrete T-beam per ACI 440.2R Guide for the Design and Construction of Externally Bonded FRP Systems for Strengthening Concrete Structures.
One of the most important initial checks for an Engineer of Record is to confirm that the unstrengthened structure can support the load combination shown in Equation 5.5.1 in ACI 562 Code Requirements for Evaluation, Repair, and Rehabilitation of Concrete Buildings:
Eq. 5.5.1: (φRn)existing ≥ (1.2SDL + 0.5SLL)new
This check is to prevent a structural failure in case that the strengthening is damaged in an extraordinary event. If the structural element cannot pass this check, then external reinforcement is not recommended.
We have a Design Questionnaire where we ask Engineers of Record for more specific information related to the element to be strengthened:
For this particular example, the following information was provided for the concrete T-beam.
1. Structure Type (e.g., building, bridge, pier, garage):
- 5-story commercial concrete building
2. Element(s) to be Strengthened/Repaired (e.g., beam, column, slab, wall):
- Reinforced concrete beams
3. Type of Deficiency (e.g., shear, flexural, axial):
- Flexural
4. Existing Factored Capacity of Section (e.g., kips, kip-ft):
- 265 kip-ft
5. Ultimate Demand to be Supported (e.g., kips, kip-ft):
- 320 kip-ft
6. Existing Concrete Compressive Strength:
- 4,000 psi
7. Existing Rebar Yield Strength:
- 60 ksi
8. Existing Reinforcement Layout:
- 3 #7s 2.6875 inches from bottom of web to centroid of steel
9. Existing Dimensions:
- 36 inches total beam height, 8 inches slab, 24 inches web width, 120 inches effective slab width
10. Relevant Existing Drawing Sheets and/or Pictures:
- See attached
11. Finish Coating Requirements/Preferences:
- None
12. For Flexural Strengthening:
- Dead Load Moment Applied at Time of Installation
- 60 kip-ft
- Service Dead Load Moment After Installation
- 80 kip-ft
- Service Live Load Moment After Installation
- 140 kip-ft
We then plug this information into our design program to come up with an FRP solution that meets the needs of the member:
For a beam that was at 83% of the capacity required for the new loading, we specified a simple, low-impact FRP solution to maintain clearances under the beams. If a traditional fix of adding cross-section to the beam had been specified instead, then additional concrete and rebar would need to be added to the beam, which would impact clearances under the beam and also increase the seismic weight of the building. The additional weight could also translate all the way through the building and even impact footing designs.
FRP can be used to increase the flexural strength up to 40% per ACI 440.
For your next retrofit project, please contact Simpson Strong-Tie to see if FRP would be an economical choice for strengthening your concrete or masonry element.
Add Simpson Strong-Tie to Your Design Team
Simpson Strong-Tie Composite Strengthening Systems™ is unlike choosing any other product we offer.
For your next retrofit project, please contact Simpson Strong-Tie to see if FRP would be an economical choice for strengthening your concrete or masonry element.
Unreinforced Masonry (URM) Buildings: Seismic Retrofit
Unreinforced masonry (URM) buildings in moderate- to high-seismic areas can be a disaster in waiting. These types of structures have very little of the ductility required of structures to prevent loss of life or business disruption in a seismic event. (Consult our Structural Engineering Blog post “Building Drift – Do You Check It?” for a discussion on ductility.) Many of these buildings are in densely populated areas, have historical meaning, provide important living or business spaces, and can be costly to retrofit. In this blog, Simpson Strong-Tie engineers discuss tools available for engineers to assess these buildings and design the retrofits needed to mitigate a potential loss of life and increase seismic resiliency.