Early this summer a package arrived at my office that I knew right away was either a copy of a new building code or design standard. Some codes or standards are more exciting than others to open up and see what’s new and different. As it turns out, this package was the just-published 2015 International Residential Code (IRC). With my interest in wood decks, I have to admit that this was new information that I was happy to see.
Why? Similar to my blog post in May mentioning the limited design resources currently available to engineers, the IRC itself is also a work in progress when it comes to the prescriptive details included for decks. Performance requirements for the framing and guards has always been included in Chapter 3, but it wasn’t until the 2009 and 2012 editions that prescriptive information for attaching a deck ledger to a wood band joist with lag screws or bolts, and a detail for transferring lateral loads to a support structure, were included. Key improvements for the 2015 IRC include provisions for composite materials, clarification of the prescriptive ledger information, and prescriptive information for decking, joist and beam allowable spans, post heights and foundations.
Lateral load connections at the support structure were a significant topic during the development of the 2015 IRC. The permitted method already in the code involves constructing the Figure 507.2.3(1) detail with 1,500 pound hold-downs, in two or more locations per deck. The detail transfers the lateral load by bypassing the joist hanger and ledger connections, and ultimately transfers it into the floor diaphragm of the support structure. The concentrated nailing on the floor joist and the need to have access from below to the install the hold-down can cause undesirable complications for builders with existing conditions. A number of common conditions also differ significantly from the detail, such as the floor joists running parallel to the deck ledger and alternate floor joist types, including i-joists or trusses. In response to frequently-asked-questions from the industry, our technical bulletin T-DECKLATLOAD provides commentary to consider for these situations. The technical bulletin also offers an alternate floor joist-to-sheathing connection that may save the builder from removing a finished floor in an existing condition or from adding additional sheathing nailing from above.
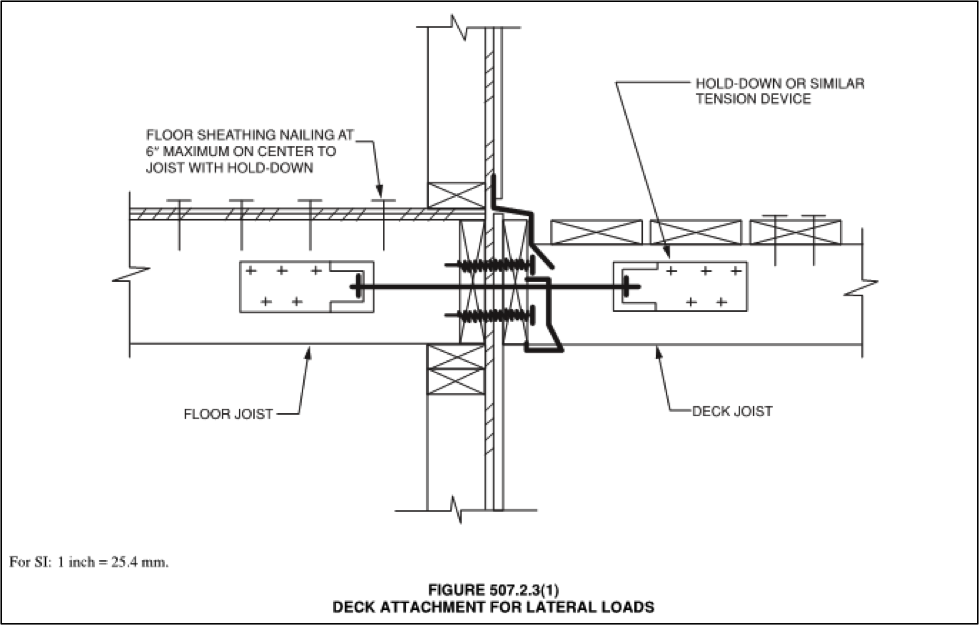
In order to provide greater flexibility, a second option is now included in the 2015 IRC: constructing Figure R507.2.3(2) with 750 pound hold-downs in four locations per deck. This detail also transfers the lateral load in bypassing the joist hanger and ledger connections, but transfers the load to the wall plates, studs, or wall header by means of a screw anchoring the hold-down. In some cases, builders will hope this detail can save removing interior portions of an existing structure, but close attention will be required in terms of the deck joist elevation with respect to components of the wall and ensuring that hold-down anchor has proper penetration into the wall framing.
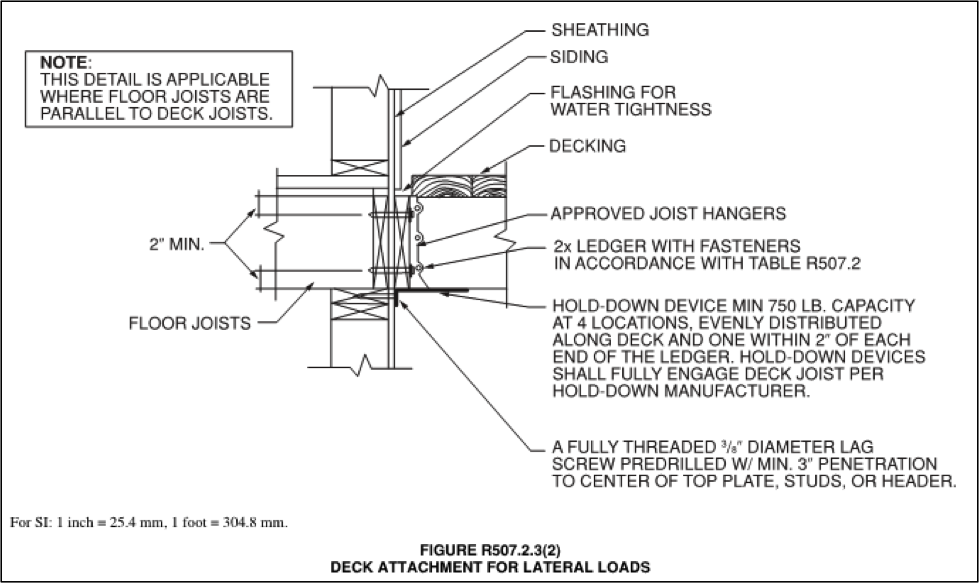
There are still a number of scenarios where a residential deck builder may need or want to consider hiring a structural engineer. Prescriptive details for guards and stairs are still not included in the code, as well as lateral considerations such as the deck diaphragm or the stability of a freestanding deck. Alternate loading conditions, such as the future presence of a hot tub, are also outside the scope of the current code. The allowance for alternative means and methods permitted by Chapter 3 of the 2015 IRC, is also something to keep in mind when the prescriptive options do not fit well with the project conditions. For example, the IRC ledger fastening table applies for connections to a band joist only and not to wall studs or other members of the adjacent support structure.
Have you been involved with any residential deck projects? Let us know in the comments section below.